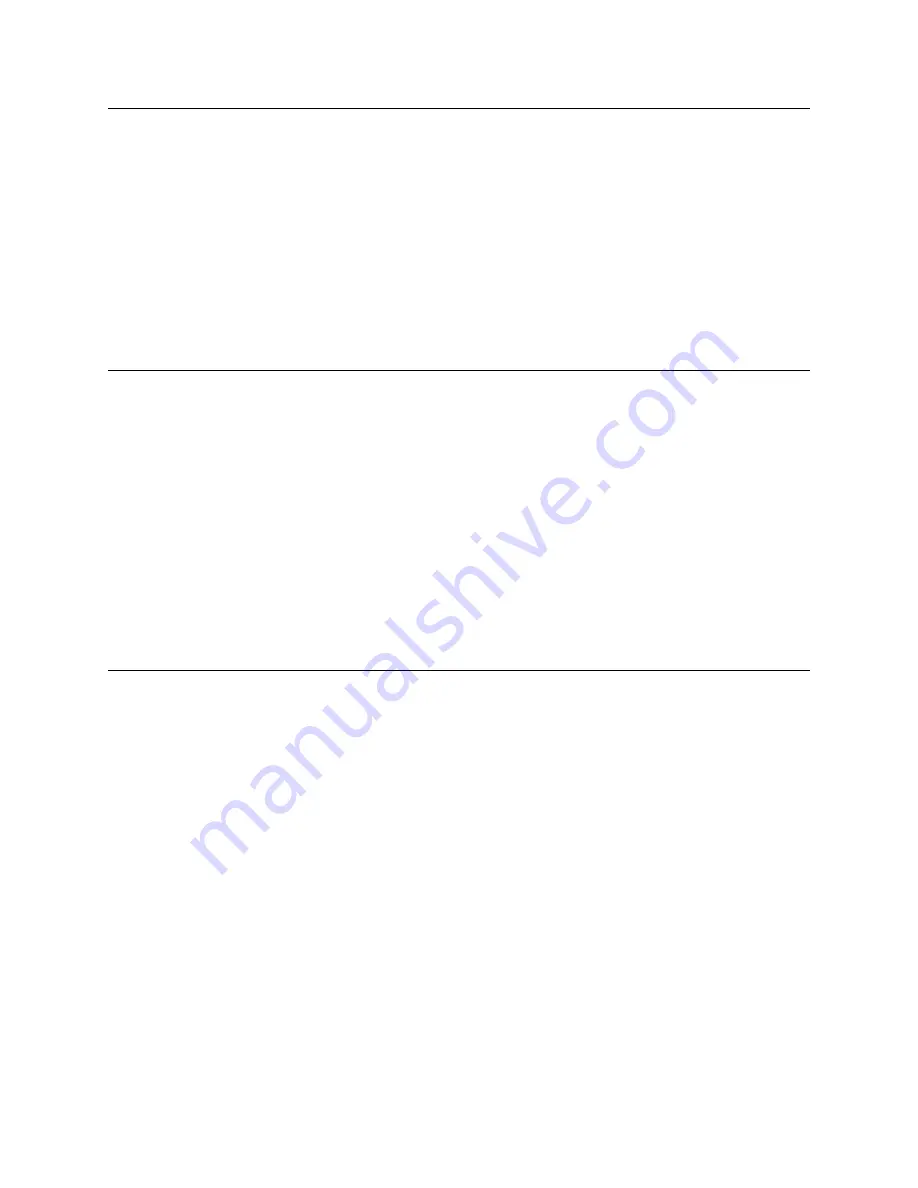
Q9 Plus ASD Installation and Operation Manual
161
Stall Prevention Control Switching
Program
Feedback
PG Settings
While running or during deceleration, the
Over-Voltage Stall
function may be
controlled by either of two profile settings as selected at this parameter.
The first profile (Stall Prevention Control 1) increases the output frequency at a
maximum of 5 Hz intervals (quick response) in response to the over-voltage
condition.
The second profile (Stall Prevention Control 2) increases the output frequency
at an interval of 0.5 Hz maximum in response to the over-voltage condition.
Settings:
0 — Stall Prevention Control 1
1 — Stall Prevention Control 2
Direct Access Number — F468
Parameter Type —
Selection List
Factory Default —
Stall Prevention
Control 1
Changeable During Run —
No
Over-Voltage Limit (Time) Constant
Program
Protection
Stall
This parameter is used in conjunction with parameters
F305
(Over-Voltage
Limit Operation) and
F626
(Over-Voltage Limit Operation Level) to set a
running window of time. The window of time is used to create an average value
to be used in calculating the DC bus voltage upper threshold value that, once
exceeded, will cause an
Over-Voltage Stall
.
While running or during deceleration, the
Over-Voltage Stall
function
increases the output frequency of the ASD for a specified time in an attempt to
prevent an
Over-Voltage Trip
.
If the over-voltage threshold level setting of parameter
F626
is exceeded for
over 4 mS, an
Over-Voltage Trip
will be incurred.
Select zero (0) for automatic value selection for this parameter.
Note:
This parameter setting may increase deceleration times.
Note:
Over-voltage alarms will display OP to convey Over-Potential.
Direct Access Number — F469
Parameter Type —
Numerical
Factory Default —
0
Changeable During Run —
No
Minimum — 0
Maximum — 1000
V/I Input Bias
Program
Frequency
Speed Reference Setpoints
This parameter is used to fine-tune the bias of the
V/I
input terminals.
Note:
See note on
pg. 44
for additional information on the
V/I
terminal.
This setting may be used to ensure that the zero level of the input source (pot,
pressure transducer, flow meter, etc.) is also the zero level setting of the ASD
system.
This is accomplished by setting the input source to zero and adjusting this
setting to provide an output of zero from the ASD.
Direct Access Number — F470
Parameter Type —
Numerical
Factory Default —
128
Changeable During Run —
Yes
Minimum — 0
Maximum — 255
F468
F470
Buy: www.ValinOnline.com | Phone 844-385-3099 | Email: CustomerService@valin.com