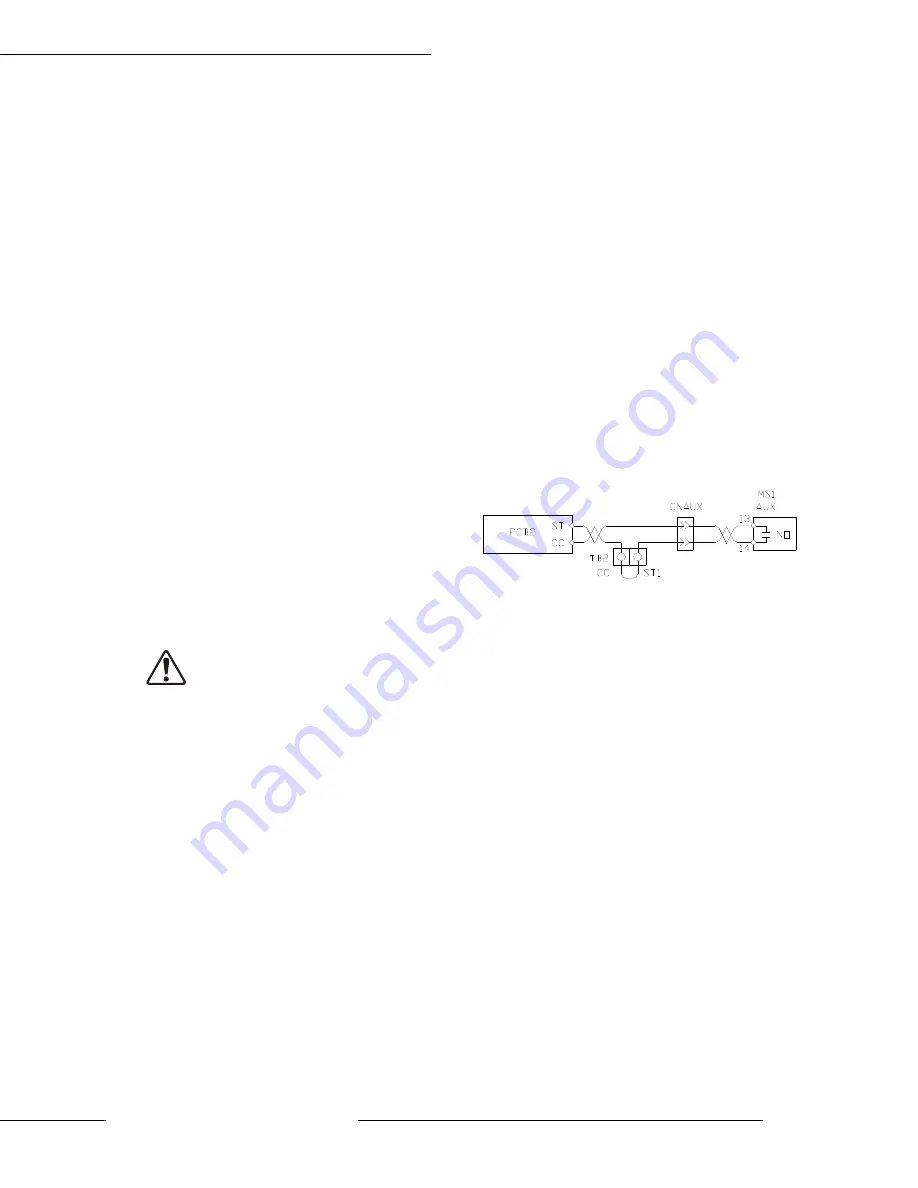
https://www.toshiba.com/tic/
13
Installation and Connections
W7B ASD Installation & Operation Manual
Installation and Connections
The ASD may be set up initially by performing a few
simple configuration settings. To operate properly,
the ASD must be securely mounted and connected
to a power source (3-phase AC input at the L1/R,
L2/S, and L3/T terminals). The control terminals of
the ASD may be used by connecting the terminals
of the Terminal Board (P/N 48570) to the proper
sensors or signal input sources (see the section
titled
System performance may be further enhanced by
assigning a function to the output terminals of the
Terminal Board and connecting the terminals to the
proper indicators or actuators (relays, contactors,
LEDs, etc.).
The output terminals of the ASD (T1/U, T2/V, and
T3/W) must be connected to the motor that is to be
controlled (see
As a minimum, the installation of the ASD shall
conform to Article 110 of the NEC, the Occupational
Safety and Health Administration requirements, and
to any other local and regional industry codes and
standards.
Installation Notes
When a brake-equipped motor is connected to the
ASD, it is possible that the brake may not release at
startup because of insufficient voltage. To avoid
this,
DO NOT
connect the brake or the brake
contactor to the output of the ASD.
If an output contactor is used for bypass operation,
it must be interlocked such that commercial power
is never applied to the output terminals of the ASD
(T1/U, T2/V, or T3/W).
DO NOT
apply commercial power to the output
terminals T1/U, T2/V, or T3/W.
If a secondary magnetic contactor
(MC) is used
between the output of the ASD and the motor, it
should be interlocked such that the ST – CC
connection is disconnected before the output
contactor is opened.
DO NOT
open and then close a secondary
magnetic contactor between the ASD and the
motor unless the ASD is off and the motor is not
rotating.
Note:
Re-application of power via a secondary
contact while the ASD is on or while the motor is
still turning may cause ASD damage.
On some devices, the ST – CC connection is
further enhanced by the operation of the MS1 AUX
relay circuit. The MS1 AUX relay circuit is normally
open and closes the ST-to-CC connection (via ST1)
only after normal system power is available. The
MS1 AUX relay circuit prohibits the ST-to-CC
connection in the event that the MS1 contactor fails
to close during startup or if MS1 opens while the
ASD is running. For the 460 Volt ASD, this feature is
available on the 75 HP and above systems.
The ASD input voltage should remain within 10% of
the specified input voltage range. Input voltages
approaching the lower or upper-limit settings may
require that the under-voltage and over-voltage stall
protection level parameters be adjusted. Voltages
outside of the permissible tolerance should be
avoided.
The frequency of the input power should be ±2 Hz
of the specified input frequency.
DO NOT
use an ASD with a motor that has a power
rating that is higher than the rated output of the
ASD.
The ASD is designed to operate NEMA B motors.
Consult the TIC Customer Support Center before
using the ASD for special applications such as with
an explosion-proof motor or applications with a
piston load.
Disconnect the ASD from the motor before megging
or applying a bypass voltage to the motor.
Interface problems may occur when an ASD is used
in conjunction with some types of process
controllers. Signal isolation may be required to
prevent controller and/or ASD malfunction (contact
CAUTION
Figure 1. Alternative ST Activation using the MS1
AUX Circuit Configuration.
Summary of Contents for W7 DN-57442-006
Page 1: ...ADJUSTABLE SPEED DRIVES W7 DN 57442 006 INSTALLATION OPERATION MANUAL June 2020 ...
Page 2: ......
Page 3: ...Document Number 57442 006 Date June 2020 W7 ASD Installation and Operation Manual ...
Page 4: ......
Page 60: ......
Page 221: ......