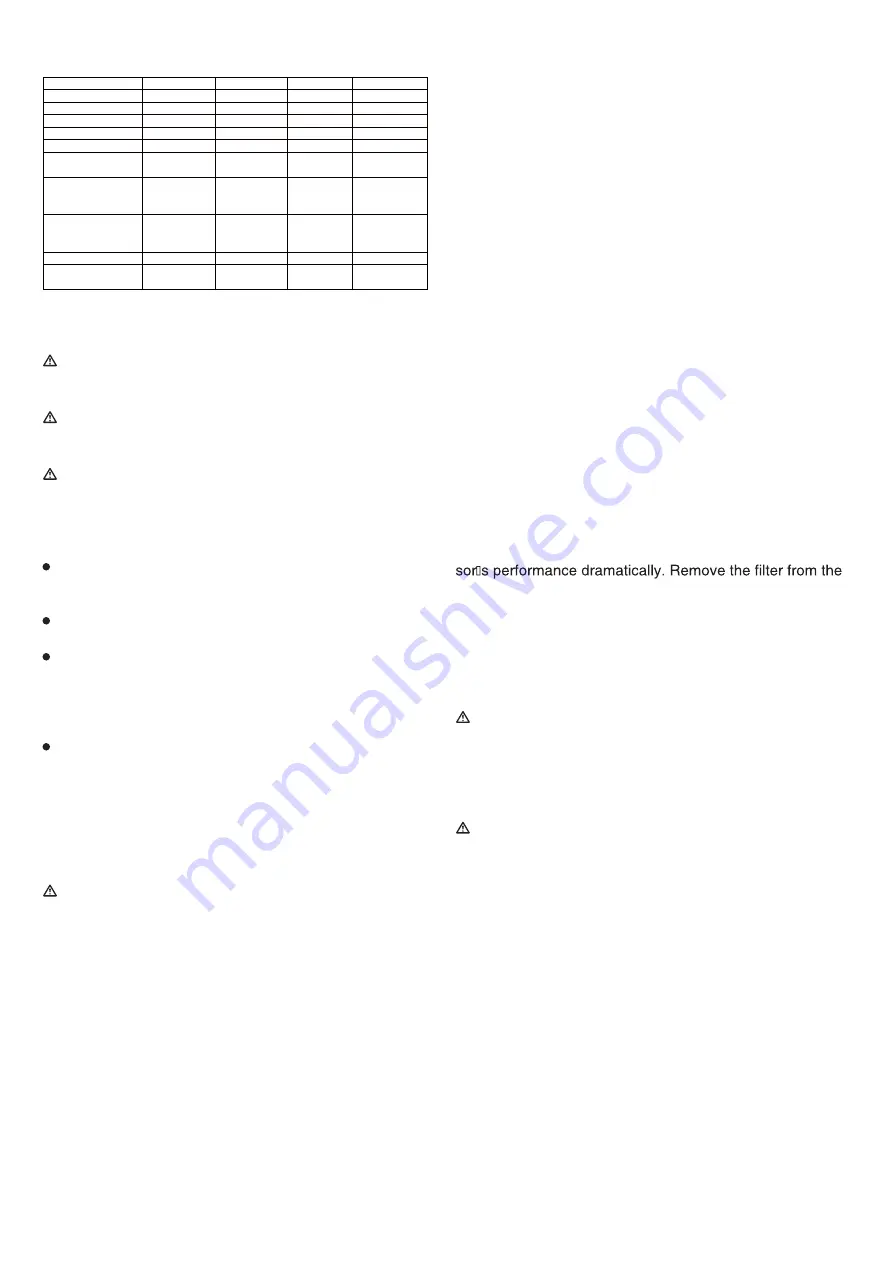
6. Technical data
7. Cleaning and maintenance
Important!
Pull the power plug before doing any cleaning and
maintenance work on the appliance.
Important!
Wait until the compressor has completely cooled
down. Risk of burns!
Important!
Always depressurize the tank before carrying out any
cleaning and maintenance work.
7.1 Cleaning
Keep the safety devices free of dirt and dust as far as
possible. Wipe the equipment with a clean cloth or blow
it with compressed air at low pressure.
We recommend that you clean the appliance immedia-
tely after you use it.
Clean the appliance regularly with a damp cloth and so-
me soft soap. Do not use cleaning agents or solvents;
these may be aggressive to the plastic parts in the ap-
pliance. Ensure that no water can get into the interior of
the appliance.
You must disconnect the hose and any spraying tools
from the compressor before cleaning. Do not clean the
compressor with water, solvents or the like.
7.2 Condensation water
The condensation water must be drained off each day by
opening the drain valve (4) (on the floor of the pressure
vessel).
Important! The condensation water from the pressu-
re vessel will contain residual oil.
Dispose of the condensation water in an environmen-
tally compatible manner at the appropriate collection
point.
7.3 Safety valve (7)
The safety valve has been set for the highest permitted
pressure of the pressure vessel. It is prohibited to adjust
the safety valve or remove its seal. Actuate the safety valve
from time to time to ensure that it works when required.
Pull the ring with sufficient force until you can hear the
compressed air being released. Then release the ring
again.
7.4 Check the oil level at regular intervals
You must be able to see that the oil level on the oil level
gauge (6) is between the red oil level check mark and the
top edge of the oil level window. Changing the oil: Recom-
mended hydraulic oil: SAE 15W/40 or an alternative of the
same quality. It should be refilled for the first time after 100
hours of operation. Thereafter the oil should be drained
and refilled after every 500 hours in service.
7.5 Changing the oil
Switch off the motor and pull the power plug out of the
socket-outlet. After letting off any air pressure you can re-
move the oil drain plug from the compressor pump by un-
screwing. To prevent the oil escaping out of control, hold a
small piece of metal guttering underneath the drain plug to
direct the oil into a container.If any oil still remains inside,
tilt the compressor a little.
Take the old oil to an official old oil disposal station.
If the oil ever escapes, fit the oil drainage screw (6) back
on. Top up with new oil through the oil filler opening (9) un-
til it comes up to the red mark in the oil level window (6).
Then fit the oil sealing plug (9) again.
7.6 Cleaning the intake filter (1)
The intake filter prevents dust and dirt being drawn in. It is
essential to clean this filter after at least every 300 hours in
service. A clogged intake filter will decrease the compres-
compressor by unscrewing the thumb screw on the air fil-
ter. You can then remove the filter from the two halves of
the plastic housing, tap it to remove the dirt and then blast
it down with low pressure compressed air (approx. 3 bar)
before reinserting it.
7.7 Storage
Important!
Pull the mains plug out of the socket and ventilate the ap-
pliance and all connected pneumatic tools. Switch off the
compressor and make sure that it is secured in such a way
that it cannot be started up again by any unauthorized per-
son.
Important!
Store the compressor only in a dry location which is
not accessible to unauthorized persons. Always store
upright, never tilted!
Model
TC120242 UTC120242 TC125502 UTC125502
Rated Voltage(V)
220-240
110-120
220-240
110-120
Rated Frequency(Hz)
50
60
50
60
Input power(Kw/PH)
1.5Kw(2HP)
1.5Kw(2HP)
1.8Kw(2.5HP) 1.8Kw(2.5HP)
No load speed(rpm)
2800
3400
2800
3400
Tank capacity(L/Gal)
24(6.3)
24(6.3)
50(13.2)
50(13.2)
Max. operating
pressure(Bar/PSI)
8(116)
8(116)
8(116)
8(116)
Air
displacement@6.2bar(
L/min)
82
82
93
93
Air
displacement@2.7bar(
L/min)
93
93
119
119
Protection type
IP 20
IP 20
IP 20
IP 20
Machine weight(Kg)
21.5
21.5
28
28
Summary of Contents for TC120242
Page 1: ...AIR COMPRESSOR TC120242 UTC120242 TC125502 UTC125502...
Page 4: ...1 11 10 3 12 1 5 4 6 9 8 2 13 2 3 11 12 8 13 9 1 6 7...
Page 12: ...TC120242 UTC120242 Exploding view...
Page 13: ...TC120242 UTC120242 Exploding view...
Page 15: ...AIR COMPRESSOR T0512 V01 MADE IN CHINA www totaltools cn TOTAL TOOLS CO LIMITED...