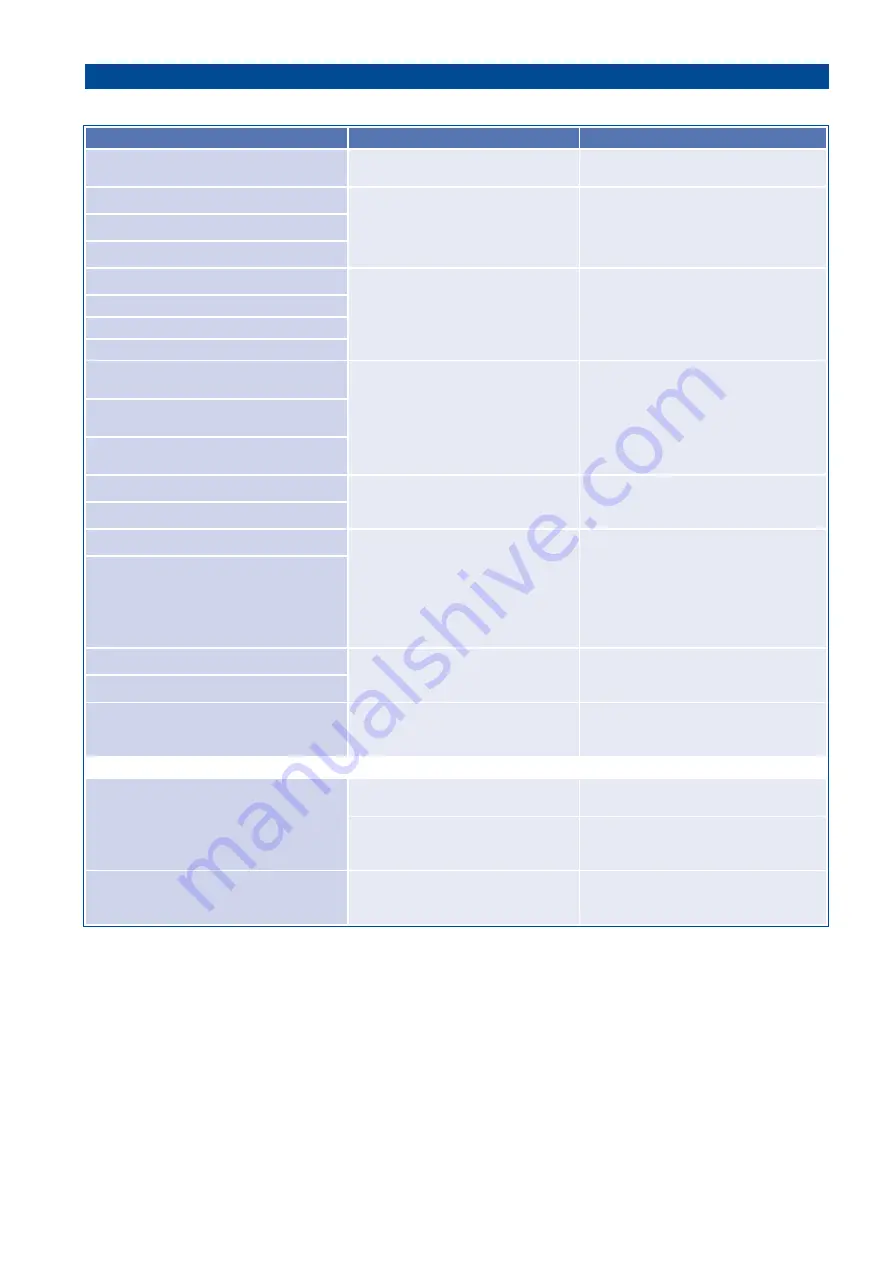
tousek
/ EN_REX-Force_01 / 25. 03. 2020
- 47 -
7. troubleshooting guide
REX Force
error
possible reason
solution
display: „Stop-switch triggered“
stop-button not connected or not
bridged
Stop-button connect or bridge → use
status display for help
display: „PHC inside triggered“
concerned photocell interrupted
check correct connection hence
remove obstacle →
use status dispaly for help
display: „PHC outside triggered“
display: „PHC back area triggered“
display: „safety edge LL1 triggered“
concerned safety edge
interrupted or hot-wired
check correct connection hence
remove obstacle →
use status dispaly for help
display: „safety edge LL2 triggered“
display: „safety edge RL1 triggered“
display: „safety edge RL2 triggered“
display: „PHi ON negative“
„PHi OFF negative“
concerned photocell
interrupted or hot-wired
check correct connection hence
remove obstacle →
use status dispaly for help
display: „PHa ON negative“
„PHa OFF negative“
display: „PHb ON negative“
„PHb OFF negative“
display: „left sensor triggered“
no communication with
absolute-sensor
check correct connection → use sta
-
tus dispaly for help
display: „right sensor triggered“
display: „searching motor L...“
no connection to the affected
ST REX smart control board
check correct connection of the bus
system → check status LED on the ST
REX smart control board
check correct addressing from the ST
REX smart control board →
Jumper on ST REX smart
display: „searching motor R..“
display: „FC error left“
no connection between
ST REX smart and
frequency converter
check correct connection of the FC →
check for BUS-RDY and BUS-ERR
display: „FC error right“
display: „search traffic light“
(only when traffic light is activated)
no connection to the traffic light
control board STA11
check correct connection of the traffic
light control board → check status
LED´s on the STA11
No reaction when giving an impulse
no line voltage hence
safety fuse broken
check line voltage as well as safety
fuses.
error of transmitter/control device/
impulse button, e.g. transmitter not
programmed
check transmitter/control device,
e.g. program transmitter and
check battery
Entry to control menu not possible
Duration command is present
(Impulse-, pedestrian button)
Check the commander teminals →
see status display