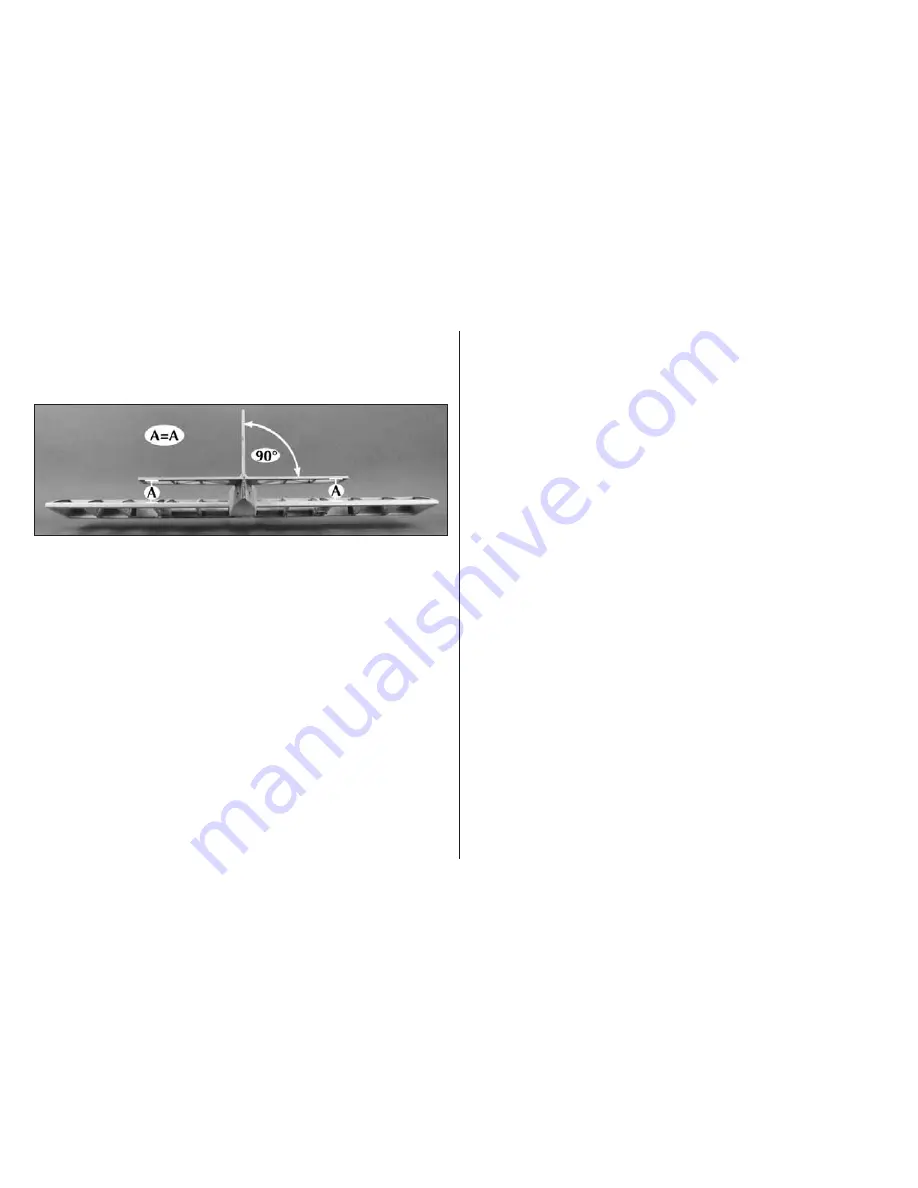
16
If not,
lightly
sand the
high side
of the stab saddle to correct the
problem. Once fully aligned, use 30-minute epoxy to glue the
stab in position. Hold it in position with masking tape and pins
until the epoxy has cured.
❍
4. Pin the fin on the centerline of the stab. Check its
alignment with the centerline of the fuse with a long
straightedge, then mark its aligned location. Glue the fin to
the stab with 6-minute epoxy. Make sure the fin is square to
the stab with a drafting triangle, then pin and tape the fin in
position until the epoxy cures.
❍
5. Cut pieces of 3/8" triangular balsa to fit on both sides of
the fin, as shown on the plans. Round off the front and rear
ends for better appearance. Glue them securely in position
to the stab and fin.
❍
6. Finish sheeting the bottom of the fuse with 3/32" x 4"
balsa sheet from F2 to just past the front edge of the front
bottom hatch rail.
❍
7. Cut the bottom hatch cover from 3/32" x 4" balsa. Fit the
hatch, then drill 1/16" pilot holes through the hatch and hatch
rails.
TIP:
Use leftover balsa to reinforce the hatch cover by
applying two or three cross-grain strips to the inside surface.
COVERING AND FINISHING
We recommend using a lightweight film covering material
such as
TowerKote
™
film to finish your Uproar. For best
results, apply the film following the manufacturer’s
instructions using the sequence we suggest on page 17.
REPAIRING SURFACE DINGS
Many surface blemishes on a framed model are caused by
bumps and balsa chips on the work surface. This type of ding
is best repaired by applying a drop or two of window cleaner
or tap water to the blemish, then running a
hot
sealing iron
over the spot to expand the wood fibers. After the surface has
dried, sand the
expanded
area smooth.
FINAL SANDING
Fill any scuffs, dings and the forward end of the pushrod tube
exit slots with balsa filler. After the filler has hardened, cut
and sand the pushrod tubes flush with the fuse sides, then
sand the entire structure with progressively finer grades of
sandpaper, ending with 320-grit.
FUELPROOFING
Fuelproof the firewall and fuel tank compartment by painting
them with thinned 30-minute epoxy. Prevent the epoxy
from
clogging the blind nuts by first packing the holes with
petroleum jelly applied with a toothpick. Be sure to
clean
off
any “external” petroleum jelly “messes” with rubbing alcohol
before fuelproofing.
Summary of Contents for UPROAR
Page 5: ...5 DIE CUT PAGE ...