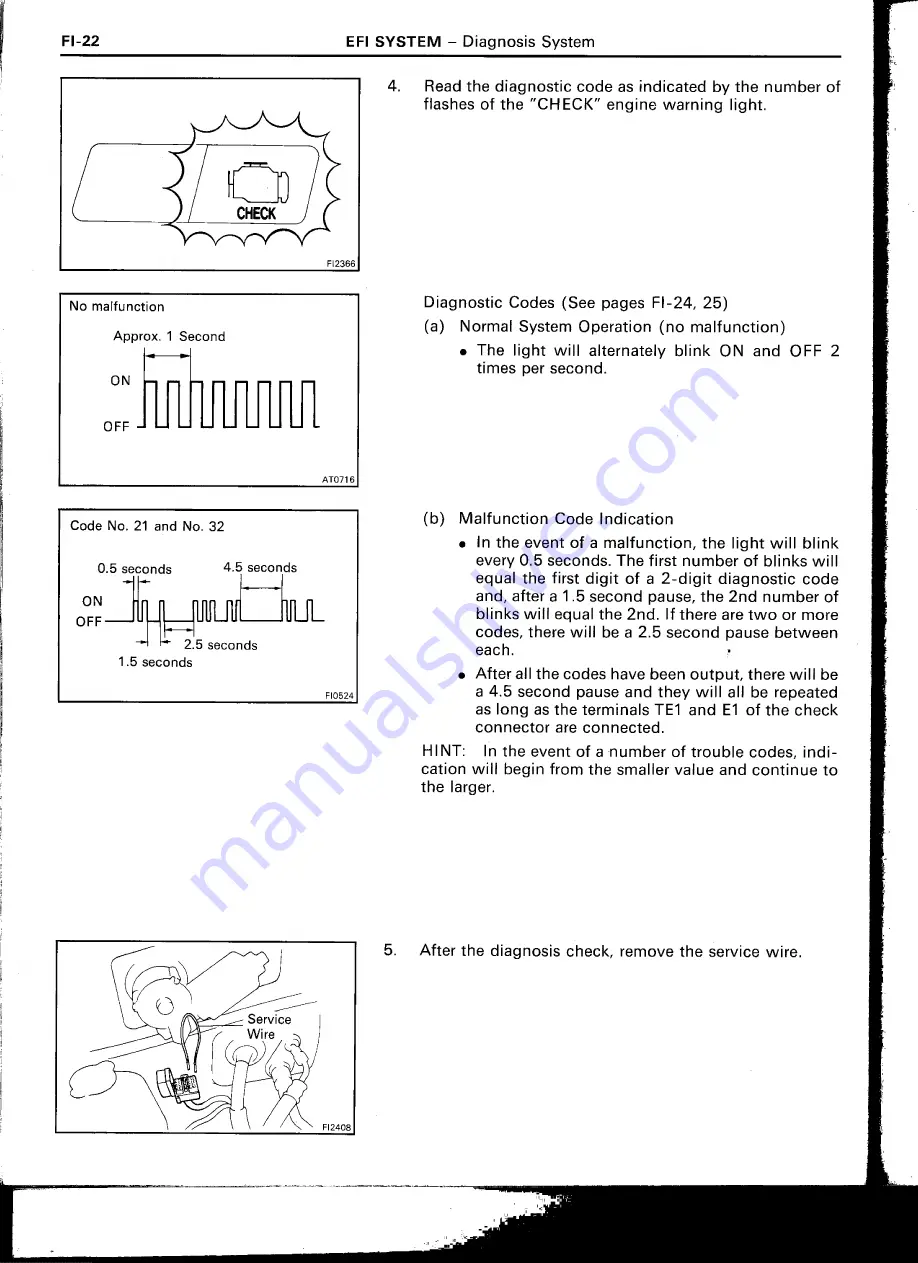
4.
Read the diagnostic code as indicated by the number of
flashes of the "CHECK" engine warning light.
Diagnostic Codes (See pages FI-24, 25)
(a) Normal System Operation (no malfunction)
• The light will alternately blink ON and OFF 2
ti mes per second.
(b) Malfunction Code Indication
• In the event of a malfunction, the light will blink
every 0.5 seconds. The first number of blinks will
equal the first digit of a 2-digit diagnostic code
and, after a 1.5 second pause, the 2nd number of
blinks will equal the 2nd. If there are two or more
codes, there will be a 2.5 second pause between
each.
• After all the codes have been output, there will be
a 4.5 second pause and they will all be repeated
as long as the terminals TE1 and El of the check
connector are connected.
HINT: In the event of a number of trouble codes, indi-
cation will begin from the smaller value and continue to
the larger.
No malfunction
Approx. 1 Second
ON
OFF
AT0716
Code No. 21 and No. 32
0.5 seconds
ON
OFF -
4.5 seconds
2.5 seconds
1.5 seconds
I
J
F10524
FI-22
EFI SYSTEM —
Diagnosis System
5.
After the diagnosis check, remove the service wire.
Summary of Contents for 3F-E
Page 1: ...ProCarManuals com ...