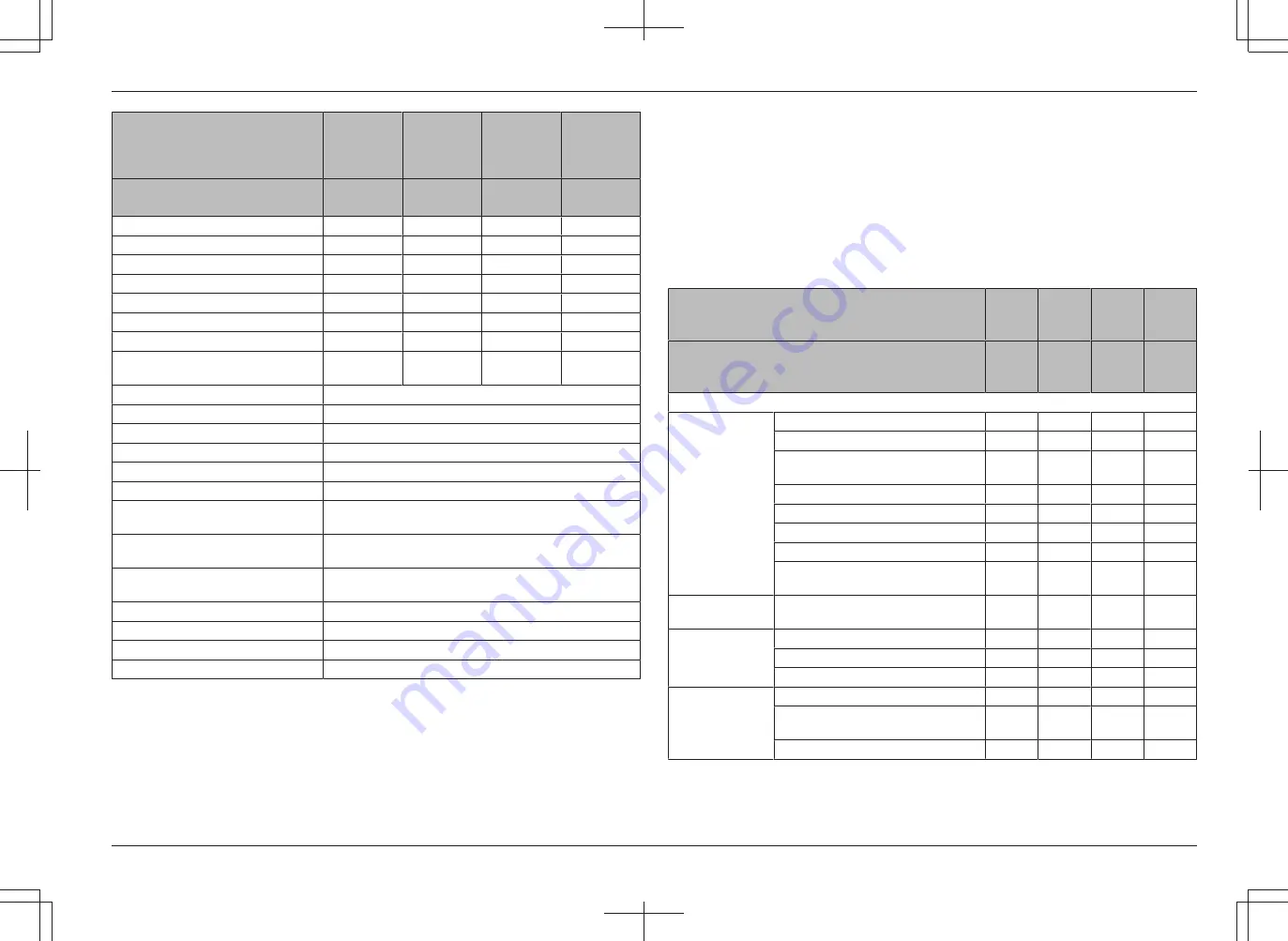
18 PLANNED MAINTENANCE
en‐80
Inspection Period
(Accumulated hours of operation
or monthly periods of operation,
whichever comes sooner.)
Every
6 weeks
Every
3 months
Every
6 months
Every
12 months
Item
Every
250 hours
Every
500 hours
Every
1000 hours
Every
2000 hours
Differential gear oil
●
Planetary gear oil
●
Hydraulic oil
●
●
Hydraulic oil filter
●*
●
●
Wheel bearing grease
●
Spark plugs
●
●
Air cleaner element
●
Cups and seals for brake booster
and wheel cylinders
●
Power steering hoses
Every 2 years
Power steering rubbers parts
Every 2 years
Hydraulic hoses
Every 2 years
Fuel hoses
Every 2 years
Torque converter rubber hoses
Every 2 years
Oring for LPG tank valve (Option)
Every 2 years
LPG high and lowpressure rubber
hoses (Option)
Every 2 years
LPG regulator diaphragm and gas
ket, Oring (Option)
Every 2 years
LPG filter & shutoff valve dia
phragm and gasket (Option)
Every 2 years
Chains
Every 3 years
Timing belt of 1KD *
1
Every 4000 hours
Hydraulic oil pump seal
Every 3 years or 6000 hours
SAS Swing lock cylinder
Every 10000 hours
*
1
: The timing belt caution function will inform the operator when the timing belt needs to be
replaced. Refer to the INSTRUMENT chapter of this manual for details.
NOTICE! In case of the harsh or severe operating condition, the service interval of 170
hours or 1 month may be recommended.
18.4.2 Periodic maintenance table
INSPECTION METHOD
I : Inspection. Repair or replacement if required.
M : Measurement. Repair or adjustment if required.
T : Retightening
C : Cleaning
L : Lubrication
*: Same as the left column
*
1
: For new truck
*
2
: Fissure and crack detector
Inspection Period
(Based on operating hours or months, whichever is
soonest.)
Every
6
weeks
Every
3
months
Every
6
months
Every
12
months
Item
Every
250
hours
Every
500
hours
Every
1000
hours
Every
2000
hours
ENGINE
Basic
compon
ents
Proper starting and abnormal noise
I*
1
I
*
*
Rotating condition at idling
M*
1
M
*
*
Rotating condition during accelera
tion
M*
1
M
*
*
Exhaust gas condition
I*
1
I
*
*
Air cleaner element
C*
1
C
*
*
Valve clearance
M*
1
M
Muffler rubber mount
I
Engine ancillary drive belt tension,
looseness and damage
I
*
*
*
PCV system
Clogging and damage in PCV valve
and piping
I*
1
I
*
*
Lubrication
sys
tem
Oil leak
I*
1
I
*
*
Oil level
I*
1
I
*
*
Clogging and dirt of oil filter
I
*
*
Fuel system
Fuel leak
I*
1
I
*
*
Dirt and clogging of fuel filter ele
ment
I
*
*
Draining of sedimenter
I
*
Summary of Contents for 40--8FD35N
Page 92: ...19 TRUCK DIMENSIONS en 93 19...