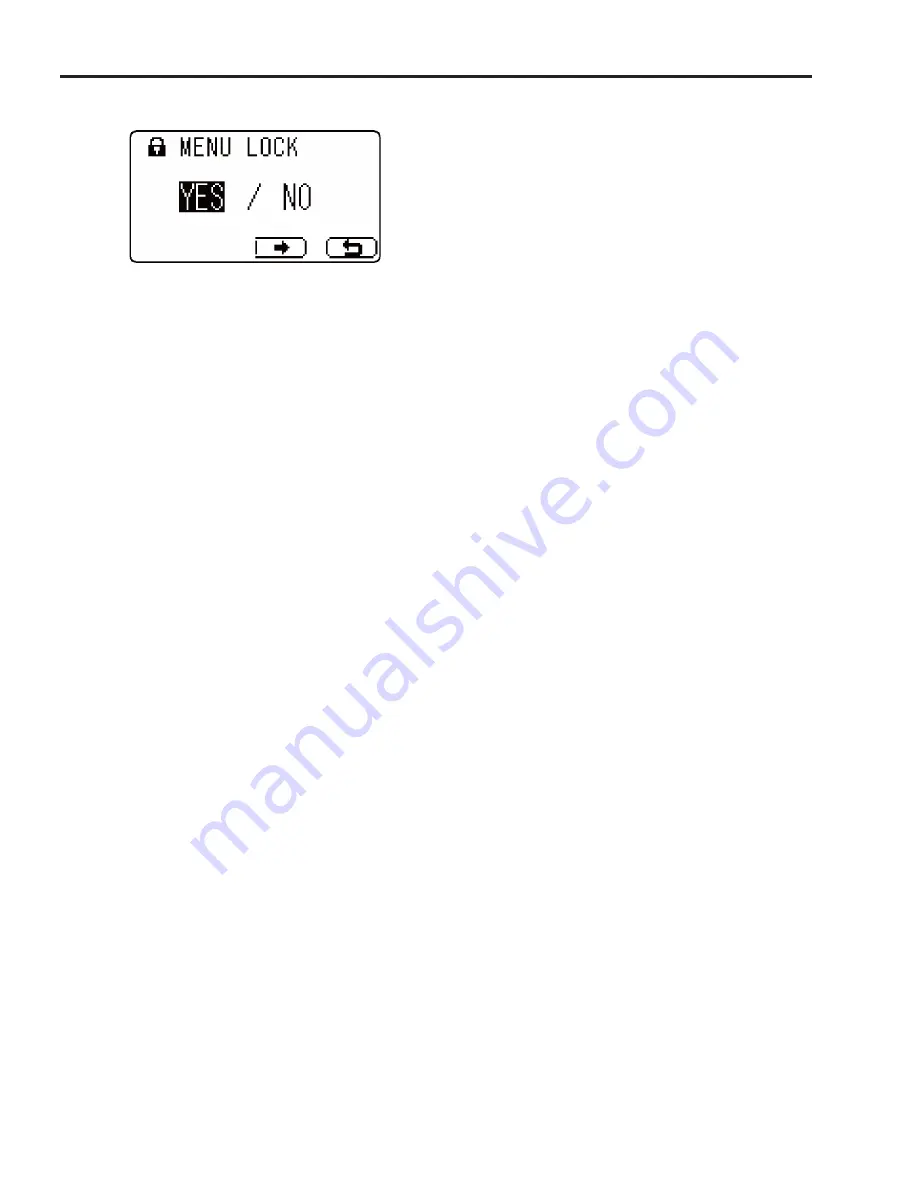
7-70
7 DISPLAY
7.1.6.3.3 Menu Lock setting screen
▪ This function can limit the change of the vehicle setting by
the operator.
When menu lock setting is "YES”, the following items are
limited.
・
Setting menu for operator is NOT displayed.
・
Eco-mode is NOT changed.
▪ Menu lock indicator is displayed on the status screen when
menu lock setting is “YES”.
Switch (2): Selecting "Yes"
Switch (3): Selecting "No"
Switch (4): Returning to menu screen
Conditions to release Menu lock vary by optionset items, "MENULOCK SPEC". In factory setting, "MENU-
LOCK SPEC" is preset in "A" on US domestic models and CANADA SPEC [OPT] models, and is preset in
"B" on export models [OPT] (except for CANADA SPEC [OPT]) and E.E.C. spec [OPT].
MENULOCK SPEC : A
The lock release setting (“NO”) is effective till key-OFF. (It means set “YES” automatically when the key
switch is turned off.)
MENULOCK SPEC : B
The lock release setting (”NO”) is effective till setting "YES" with a setting screen again.
Summary of Contents for 62-8FDU15
Page 5: ...1 3 1 GENERAL 1 2 FRAME NUMBER Frame No Punching Position Punching position 1...
Page 8: ...2 6 2 STEERING 4YM and 1DZ engine W synchronized steering B B A A B B C C C C...
Page 11: ...2 9 2 STEERING 2 3 COMPONENTS 1ZS and 4YE engine 4507 4YM and 1DZ II engine 4507 2...
Page 13: ...2 11 2 STEERING 4YM and 1DZ II engine W synchronized steering 4503 2...
Page 23: ...3 21 3 MATERIAL HANDLING SYSTEM 3 2 COMPONENTS 6801 3...
Page 46: ...5 44 5 OIL CONTROL VALVE 5 2 3 COMPONENTS 1ZS and 4YE engine ASSY FITTING 6705...
Page 55: ...6 53 6 SAS OPS 6...
Page 56: ...6 54 6 SAS OPS Load Sensor 1DZ II engine 5803...
Page 157: ...8 155 8 TROUBLESHOOTING 8 3 WHEN NO ERROR CODE IS DISPLAYED Defect causes related to SAS OPS 8...
Page 191: ...8 189 8 TROUBLESHOOTING 8 4 WHEN ERROR CODE IS DISPLAYED 8...
Page 221: ...Published by 1st Printing Mar 2016 Pub No CE118 Printed in USA...
Page 222: ...PRINTED IN USA Pub No CE118...