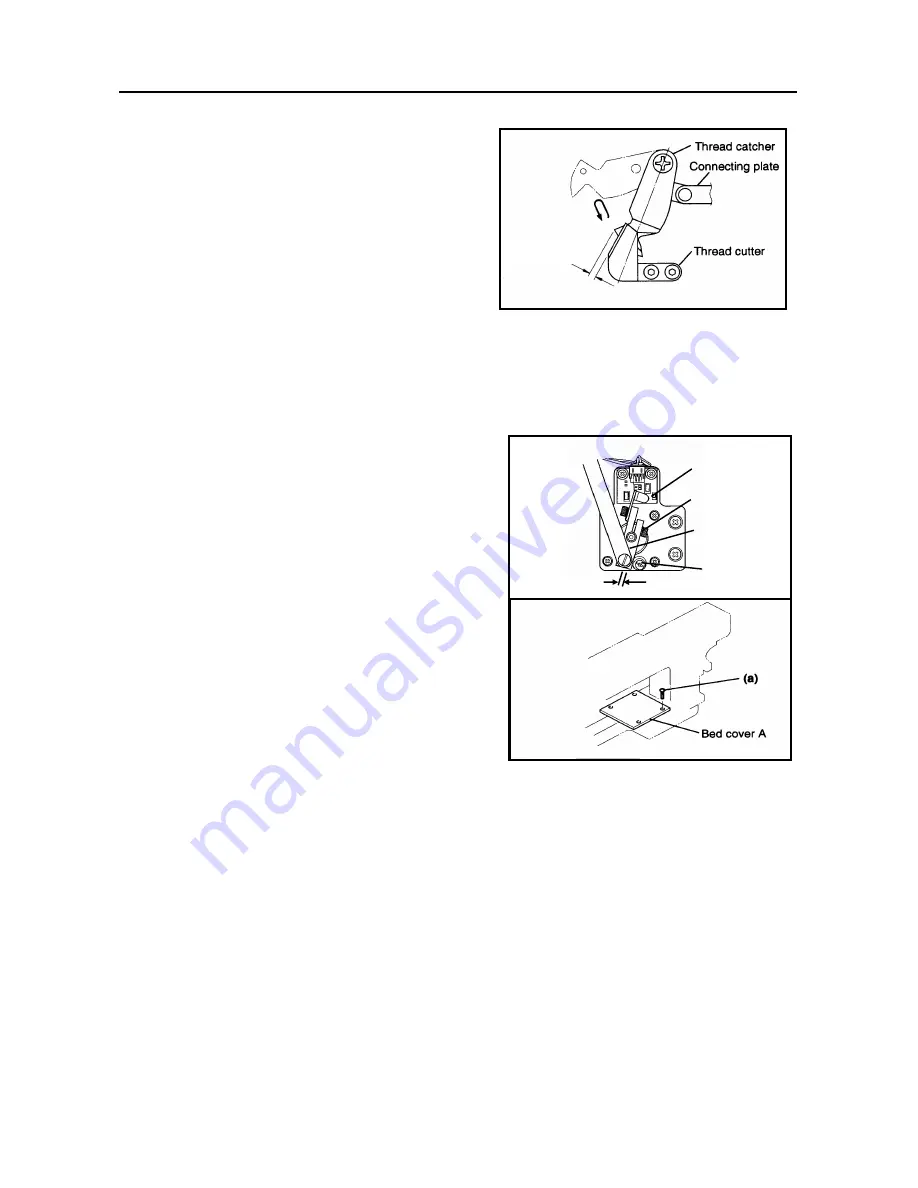
3.ADJUSTMENT
3-3 Standby position of thread
catcher
[Inspection]
(1) Remove the needle plate.
(2) Remove the table set.
(3) Turn the power on and press the
thread trim key to perform the thread
trimming.
(4) The relative positions of the thread
catcher and the thread cutter must be a
clearance of 0 ± 0.5mm. (Fig.1)
(5) At that point, LED must be turned on.
(Fig.2)
[Adjustment]
(1) Loosen four set screws (a) and remove
bed cover A. (Fig.3)
(2) Remove four set screws (b) and remove
the base cover rear L.. (Fig.4)
(3) Remove three set screws (c) and
remove the base cover front L. (Fig.4)
(4) If the LED is not turned on, loosen the
set screw (d) of the thread trimming drive
lever and adjust the clearance between
the lever and stopper to 0.5mm. (Fig.2)
Then perform the thread trimming to
check the standby position of the thread
catcher.
Note: At this time, vertical position of the
thread trimming drive lever must be 0 to
0.1mm from the motor spacer.
(5) If the LED is not turned on and the
clearance between the lever and
stopper is 0.5mm, loosen the set screw
of the drive arm, set the thread catcher
at 0 ± 0.5mm from the thread cutter and
tighten the set screw of the drive arm.
Then perform the thread trimming to
check the standby position of the thread
catcher. (Fig.5)
0
±
0.5mm
FIG.1
FIG.2
FIG.3
LED
(d)
Thread
Trimming
drive lever
0.5mm
Stopper
-26-
Summary of Contents for ESP9000
Page 1: ...SERVICE MANUAL Embroidery Machine ESP9000 15 needles...
Page 2: ......
Page 13: ...FIG 3 48...
Page 24: ...FIG 4 59...
Page 36: ...Connection of connector CN 10 Must be connected correctly Replace See P 47 CN10 11...
Page 40: ...Picker height C 7 9 mm when piker solenoid is ON Adjust See P 27 15...
Page 58: ...FIG 2 FIG 3 201 3 0 1 0 3 mm 22...
Page 63: ...FIG 4 e Drive arm FIG 5 27...
Page 70: ...FIG 3 34...
Page 72: ...FIG 2 FIG 3 201 3 0 1 0 3 mm 22...
Page 74: ...FIG 2 FIG 3 Needle bar Stopper Needle bar Connecting stud 24...
Page 77: ...FIG 4 e Drive arm FIG 5 27...
Page 84: ...FIG 3 34...
Page 86: ...FIG 4 31...
Page 88: ...FIG 4 33...
Page 90: ...FIG 2 35...
Page 93: ...2 a Sensor arm 3 38...
Page 95: ...FIG 3 FIG 4 VR6 Power supply board 40...
Page 97: ...FIG 3 FIG 4 0 5 to 0 8mm 0 2mm or less Hook support hook support 37...
Page 100: ...FIG 4 40...
Page 103: ...FIG 2 Needle bar c Top dead center stopper needle bar connecting stud FIG 3 43...
Page 105: ...FIG 5 45...
Page 111: ...Printed in Japan 2002 8...