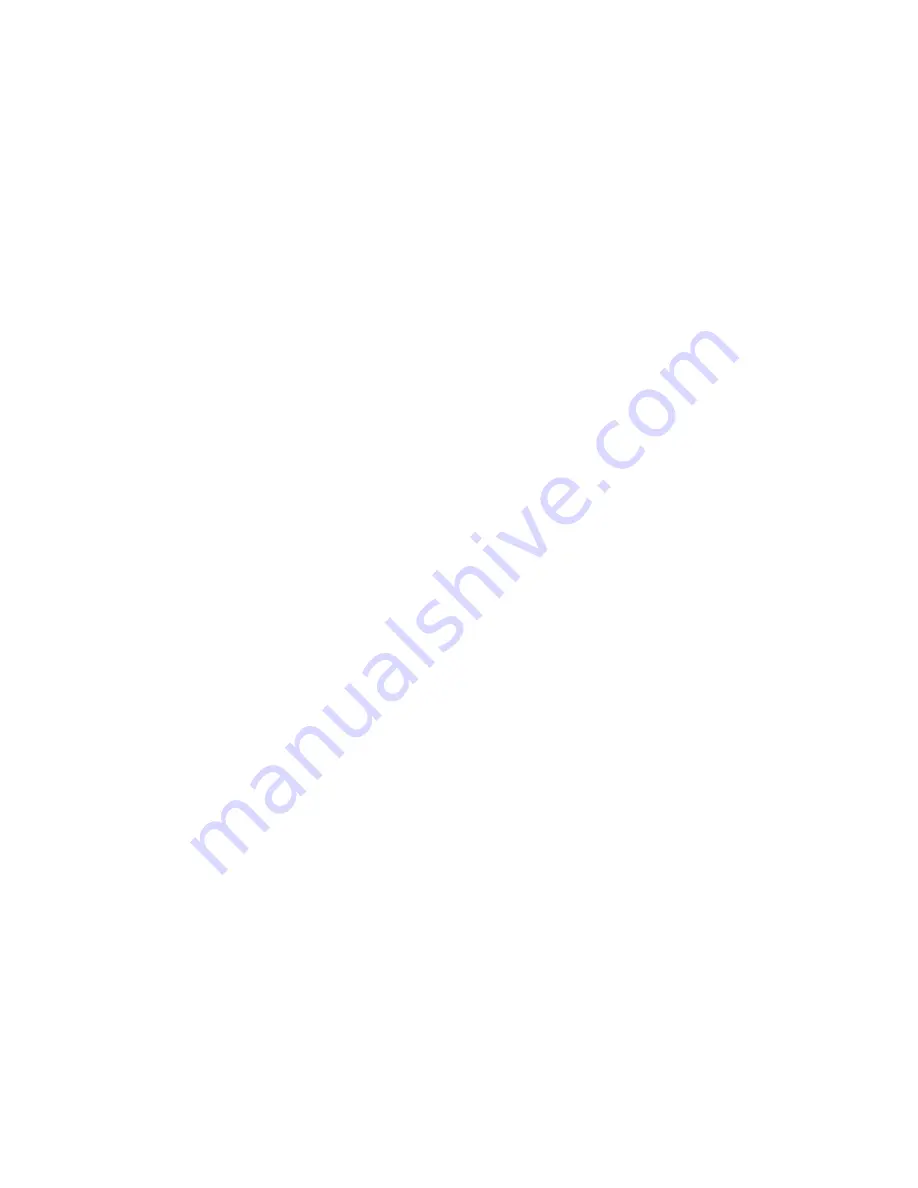
DRILL PRESS SAFETY
CAUTION!
For your own safety, do not try to use your drill press or plug it
in until it is completely assembled and installed according to the
instructions, and until you have read and understood this
instruction manual:
1. YOUR DRILL PRESS MUST BE BOLTED
securely to
a workbench. In addition, if there is any tendency for your
drill press to move during certain operations, bolt the
workbench to the floor.
2. THIS DRILL PRESS
is intended for use in dry conditions,
indoor only.
3. WEAR EYE PROTECTION.
USE A face or dust mask
along with safety goggles if drilling operation is dusty. USE
ear protectors, especially during extended periods of
operation.
4. DO
NOT
wear gloves, neckties, or loose clothing.
5. DO
NOT
try to drill material too small to be securely held.
6. ALWAYS
keep hands out of the path of a drill bit. Avoid
awkward hand positions where a sudden slip could cause
your hand to move into the drill bit.
7. DO
NOT
install or use any drill bit that exceeds 175 mm
(7”) in length or extends 150 mm (6”) below the chuck jaws.
They can suddenly bend outward or break.
8. DO NOT USE
wire wheels, router bits, shaper cutters,
circle (fly) cutters, or rotary planers on this drill press.
9. WHEN
cutting a large piece of material ,make sure it is
fully supported at the table height.
10. DO NOT
perform any operation freehand. ALWAYS use
clamps or a vise.
11. MAKE SURE
there are no nails or foreign objects in the
part of the workpiece to be drilled.
12. CLAMP THE WORKPIECE OR BRACE IT
against the
left side of the column to prevent rotation. If it is too short
or the table is tilted, clamp it solidly to the table.
13. IF THE WORKPIECE
overhangs the table such that it
will fall or tip if not held, clamp it to the table or provide
auxiliary support.
14. SECURE THE WORK.
Use clamps or a vise to hold the
work when practical. It’s safer than using your hand and it
frees both hands to operate tool.
15. WHEN
using a drill press vise, always fasten to the table.
16. MAKE SURE
all clamps and locks are firmly tightened
before drilling.
17. SECURELY LOCK THE HEAD
and table support to the
column, and the table to the table support before operating
the drill press.
18. NEVER
turn your drill press on before clearing the table of
all objects (tools, scraps of wood, etc.)
19. BEFORE STARTING
the operation, jog the motor switch
to make sure the drill bit does not wobble or vibrate.
20. LET THE SPINDLE REACH FULL SPEED
before
starting to drill. If your drill press makes an unfamiliar
noise or if it vibrates excessively, stop immediately, turn
the drill press off and unplug. If do not restart the unit until
the problem is corrected.
21. DO NOT
perform layout assembly or set up work on the
table while the drill press is in operation.
22. USE THE RECOMMENDED SPEED
for any drill press
accessory and for different workpiece material. READ THE
INSTRUCTIONS that come with the accessory.
23. WHEN DRILLING
large diameter holes, clamp the
workpiece firmly to the table. Otherwise, the bit may grap
and spin the workpiece at high speeds. DO NOT USE fly
cutters or multiple-part hole cutters, as they can come apart
or become unbalanced in use.
24. MAKE SURE
the spindle has come to a complete stop
before touching the workpiece.
25. TO AVOID INJURY
from accidental starting, always turn
the switch “OFF” and unplug the drill press before
installing or removing any accessory or attachment or
making any adjustment.
26. KEEP GUARDS IN PLACE
and in working order.
27.
USE ONLY THE SELF-EJECTING TYPE CHUCK
KEY
as provided with the drill press.
4
Summary of Contents for DP12LW
Page 7: ...CARTON CONTENTS 7 L M N O ...
Page 22: ...22 ...