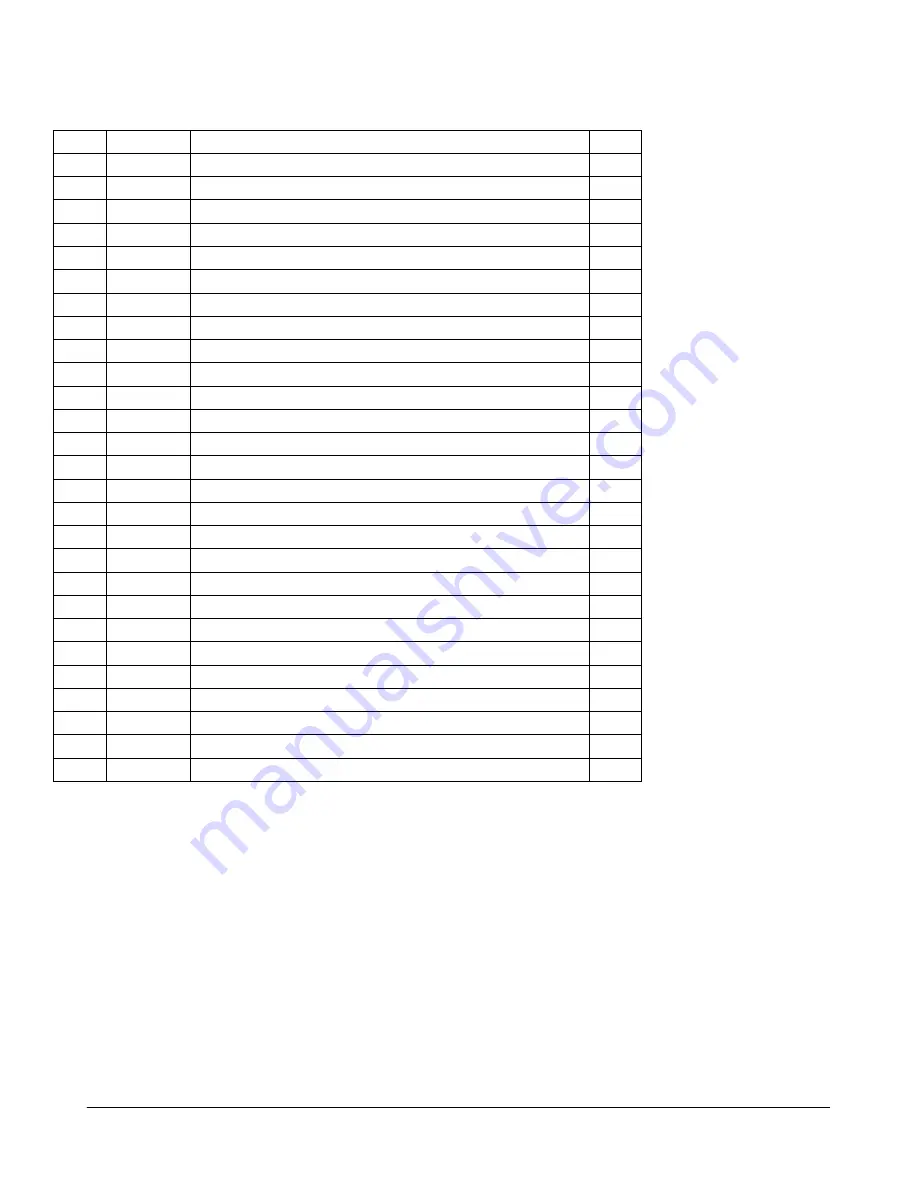
186
TRAK Machine Tools
Southwestern Industries, Inc.
ProtoTRAK SMX, K2, K3 & K4 & Retrofit Safety, Installation, Maintenance, Service and Parts List Manual
Parts List – K2/K3 Lower Vari-Disc Drive (Figure 123)
Item P/N
Title
Qty
1
VS50
FRU-K3-BELT HOUSING BASE
1
2
VS59
FRU-K3-BRAKE BLOCK
2
3
VS58
FRU-K3-TURNING BLOCK SHAFT
1
4
VS103
FRU-K3-RETAINING RING Ø 7
1
5
VS51
FRU-K3-SET SCREW M6-1.0X6L
2
6
VS53
FRU-K3-BRAKE LOCK BUSHING
1
7
VS52
FRU-K3-BRAKE LOCK SHAFT
1
8
VS52-2
FRU-K3-BRAKE LOCK PIN DIA 3 X 5/8"L
1
9
VS47
FRU-K3-BRAKE SHOE
2
10
VS48
FRU-K3-BRAKE SHOE PIVOT SLEEVE
1
11
VS17
FRU-K3-SOCKET CAP SCREW M6-P1.0x35L
1
12
VS17-1
FRU-K3-WASHER Ø 6
1
13
VS17-2
FRU-K3-NUT M6-P1.0
1
14
VS49
FRU-K3-BRAKE SPRING
2
15
VS122
FRU-K3-WASHER DIA 3.3
4
16
VS120
FRU-K3-SCREW-PAN HEAD PHILIP 5-40NC
4
17
VS46
FRU-K3-BRAKE BEARING CAP
1
18
VS43-1
FRU-K3-BALL BEARING 6010ZZ
1
19
VS14
FRU-K3-SOCKET CAP SCREW M5-0.8x12L
4
20
VS45
FRU-K3-STATIONARY DRIVEN VARIDISC
1
21
VS70
FRU-K3-SPINDLE PULLY ASSY
1
22
VS100
FRU-K3-SPINDLE PULLY SPACER
1
23
VS71
FRU-K3-KEY 8x7x20L
1
24
VS97
FRU-K3-SNAP RING Ø 40
1
25
VS50-1
FRU-K3-DUST COVER
1
26
VS50-2
FRU-K3-SCREW-FH-PH-STL-BO M6-1.0X6L
4
27
24055
BRAKE SHOE ASSY
(1)
i20778-5