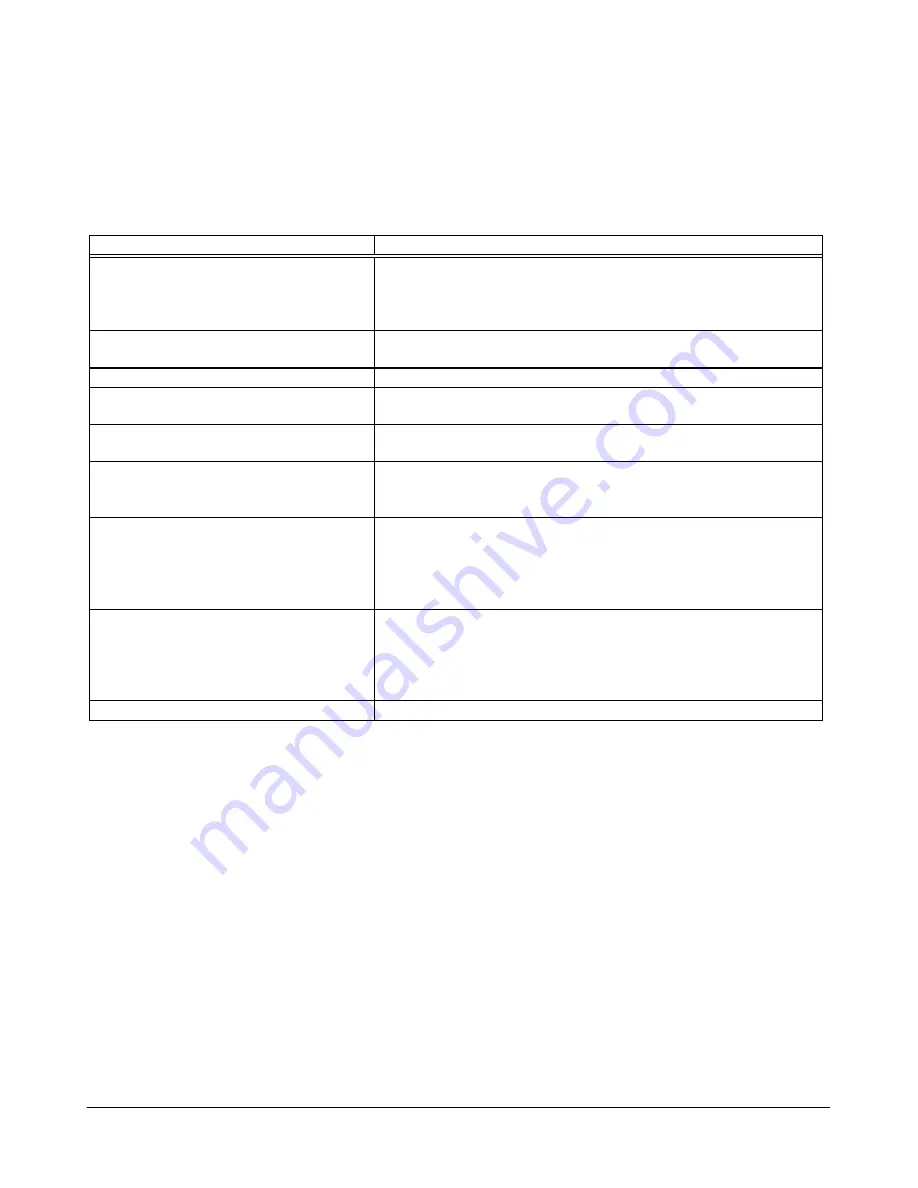
39
TRAK Machine Tools
Southwestern Industries, Inc.
ProtoTRAK SMX, K2, K3 & K4 & Retrofit Safety, Installation, Maintenance, Service and Parts List Manual
Do the following Service Codes and document values:
Code 33
Software Identification. This is needed if you call SWI Customer Service.
Code 11
Measures backlash in the system (Only used on Dual Feedback systems)
Code 12
Feed Forward Constant.
Code 127
Measures backlash in the system (not used on Dual Feedback systems).
Code 128
Enter backlash compensation.
Possible Cause
Check This
Torque values on X and Y-axis are too
high.
Make sure torque is lower than 20 in-lbs. Normal values for a
machine that is aligned and adjusted properly should be
between 10 and 15 in-lbs. Make sure torque is consistent across
axis travel.
Machine Tool and Setup problem
Check for any looseness in the setup (Tool, Tool holder, Part,
Vise, or Fixture). See Machine Tool & Setup - Section 4.1
Machine not level
Verify that the machine is level to specification.
Head is not Trammed
Verify that the Head is Trammed to specification. See Tramming
the Head Sec 5.2.3
X and Y Gibs are not adjusted properly
Check the adjustment of the X and Y Gibs using the X and Y Gib
adjustment procedures.
Calibration or Backlash problem
Recalibrate the machine. Reset the Backlash. Check
Repeatability and Positional Accuracy. See Calibration &
Backlash Constants Section 5.2.2
TRAK Sensor or Glass Scale problem
Make sure that the Sensor or Glass Scale is installed correctly
according to the Sensor or Glass Scale Installation procedures.
Check for any loose brackets or misalignment etc. Also, check to
make sure the Sensor or Glass Scale assemblies are functioning
correctly. See TRAK Sensors or Glass Scales Sections 4.6 & 4.7.
X & Y-axis Drive Trains are loose
Check Repeatability using the Repeatability and Positional
Accuracy procedure. Step by step, carefully inspect the Drive
Train for any looseness. It may be necessary to disassemble and
then reassemble the Drive Train. See Mechanical Drive Train (X,
Y) Section 4.2
Head Bolts are loose
Verify that all the head bolts are tight. 50 lbs.
3.1.3 Taper Cut on a Programmed Straight Line Move
An unwanted tapered cut occurs, when the machine is programmed to move in a straight line along either the X or Y-
axis. The DRO shows motion of a few thousandths of an inch in the axis that is not supposed to be moving.
Explanation: For straight line cuts along the X or Y-axis, the control is designed to lock the motor of the axis that is not
moving. A taper is created when there is play in the system. The force of the tool shoves the table or saddle out of
position.
The system will respond to being pushed out of position by making an adjustment at the end of the move.
An unwanted tapered cut is the result of looseness in the system.
Do the following Service Codes and document values:
Code 33
Software Identification. This is needed if you call SWI Customer Service.
Code 11
Measure's the backlash in the system. Only used on machines with Dual Feedback systems.
Code 12
Feed Forward Constant.
Code 127
Measure's the backlash in the system. Only used on machines with single Feedback.
Code 128
Enter backlash compensation.