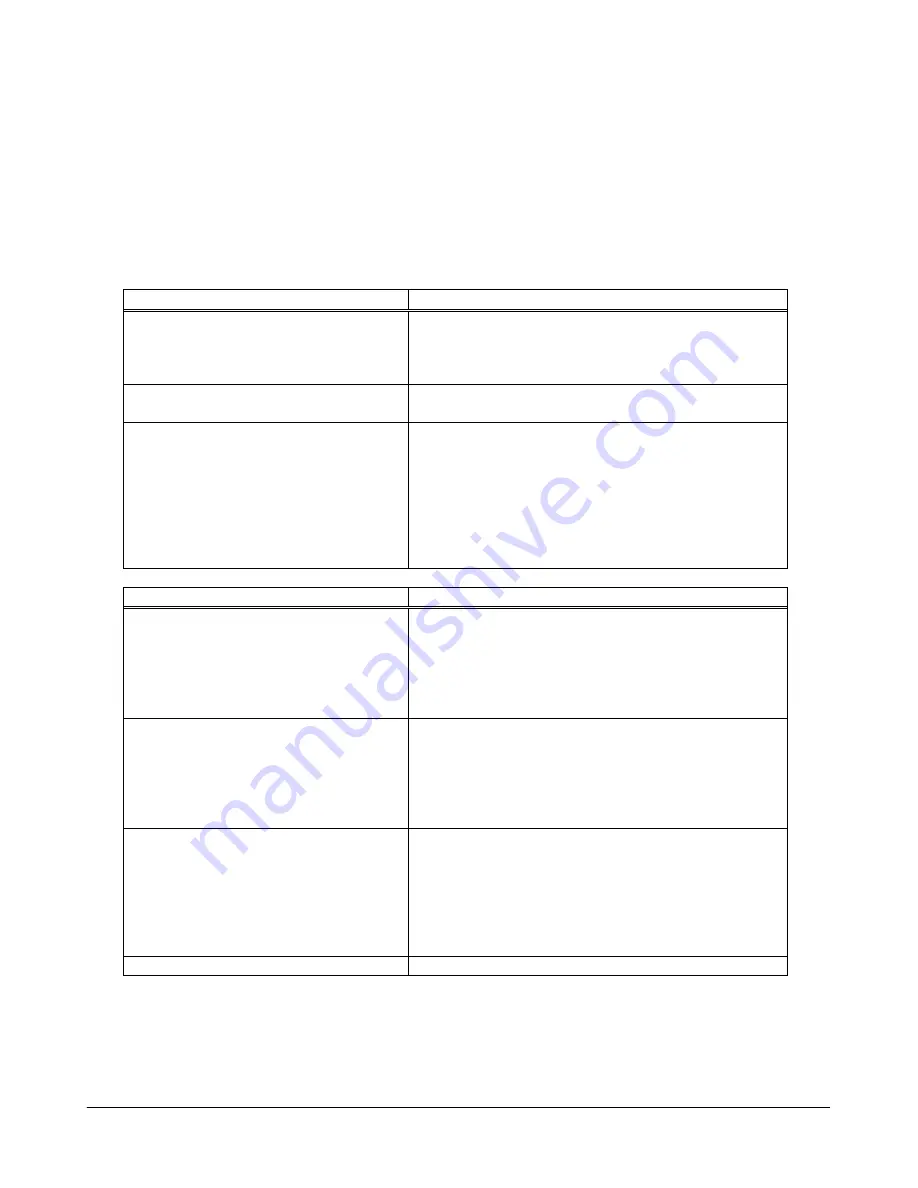
49
TRAK Machine Tools
Southwestern Industries, Inc.
ProtoTRAK SMX, K2, K3 & K4 & Retrofit Safety, Installation, Maintenance, Service and Parts List Manual
Test for accumulative error by moving the axis a number of times to see if the error gradually grows by a small amount.
If so, it may be caused by a misaligned sensor or scale. If the error abruptly changes by a large amount, it may be
caused by a bad encoder.
Expected repeatability numbers should be 0.0005” or less.
Do the following service codes and procedures:
Code 304
Toggle X sensor/glass scale on/off
Code 305
Toggle Y sensor/glass scale on/off
Possible Cause
Check This
Machine Tool & Setup problem
Check for any looseness in the setup (Tool, Tool
holder, Part, Vise, or Fixture). Make sure there is
sufficient contact between the tool holder and the
spindle. See Machine Tool & Setup Section 4.1
X and Y Gibs are loose
Check the adjustment of the X and Y Gibs using the X
and Y Gib adjustment procedures.
TRAK Sensor or Glass Scale problem
Make sure that the Sensor or Glass Scale is installed
correctly according to the Sensor or Glass Scale
Installation procedures. Check for any loose brackets
or misalignment etc. Also, check to make sure the
Sensor or Glass Scale assemblies are functioning
correctly. Use service codes 304 for X and 305 for Y
to turn off the suspect encoder. Does problem still
exist after turning it off?
Possible Cause
Check This
X and Y-axis Drive Trains are loose
Check Repeatability using the Repeatability and
Positional Accuracy procedure. Step by step, carefully
inspect the Drive Train for any looseness. It may be
necessary to disassemble and then reassemble the
Drive Train. See Mechanical Drive Train (X, Y) Section
4.2
Encoder Disk or Reader Head on motor
are loose
Swap the motor in question with a known good motor.
For example, swap the X-axis motor with the Y-axis
motor. If the symptom stays with the motor in
question, then replace the motor. If not, then the
motor is not at fault and something else is causing the
problem.
Spindle and/or Quill are loose
Use a Dial Indicator and check for side-to-side
movement between the Spindle and the Head. Next,
check for side-to-side movement between the Quill
and the Head. There should be no more than 0.0003"
of side-to-side movement. Make sure that there is a
few thousandths gap between the Spindle Collar and
the Quill after tightening.
Head bolts are loose
Tighten Ram bolts