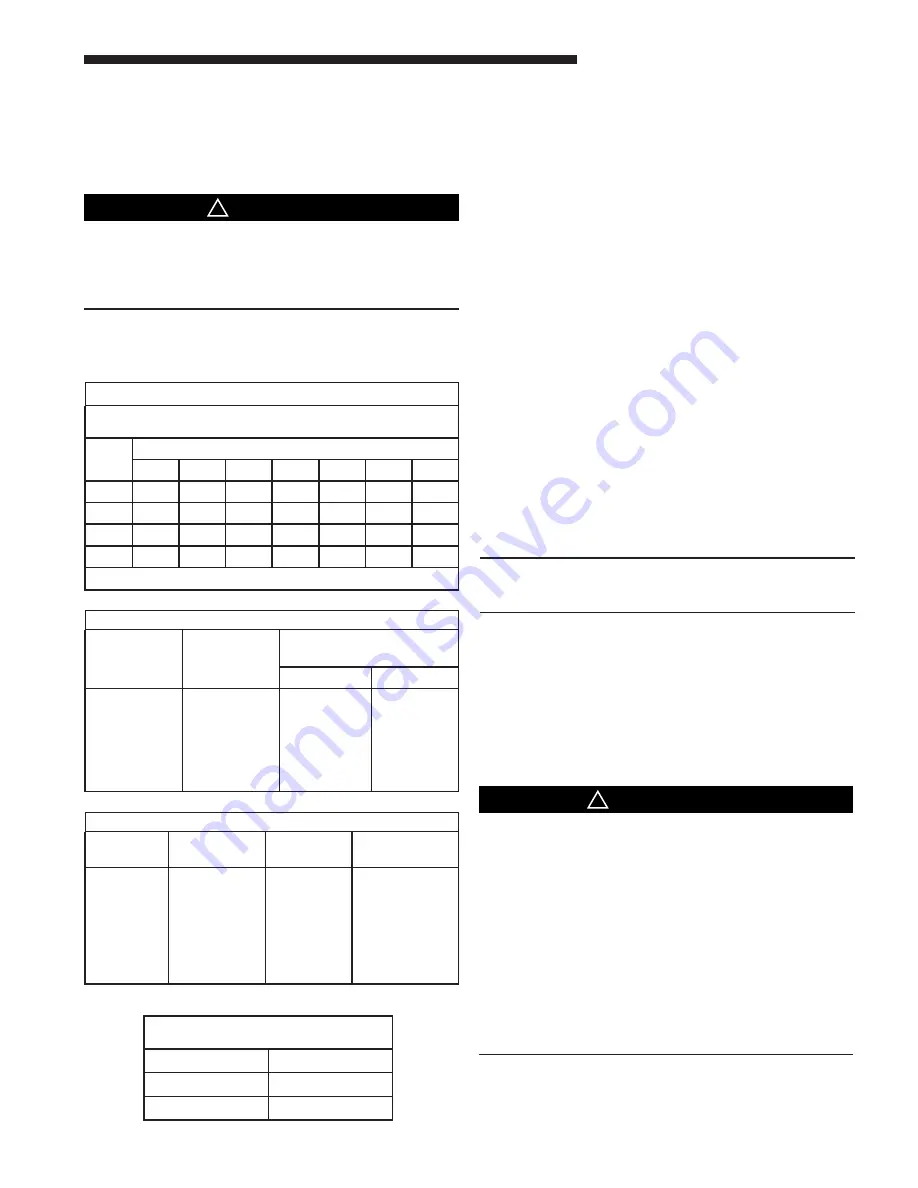
Installer’s Guide
18-CD21D1-12
9. Using a leak detection solution or soap suds, check
for leaks at the pressure outlet boss and pressure
tap test screw.
10. Turn on system power and check operation of the
unit.
▲
CAUTION
!
Replace and/ or tighten all plugs removed or loosened
when adjusting gas pressure. Leak check the fittings
before placing the furnace into regular service.
Failure to follow this warning could result in fire, explo-
sion, or property damage.
Table 10 lists the main burner orifices shipped with
the furnace. If a change of orifices is required to cor-
rect the input rate, refer to Table 11.
TABLE 9
NATURAL GAS ONLY
TABLE OF CUBIC FEET PER HOUR OF GASFOR VARIOUS PIPE
SIZES AND LENGTHS
PIPE-
SIZE
LENGTH OF PIPE
10
20
30
40
50
60
70
1/2
132
92
73
63
56
50
46
3/4
278
190
152
130
115
105
96
1
520
350
285
245
215
195
180
1-1/4
1050
730
590
520
440
400
370
This table is based on pressure drop of 0.3 inch W.C. and 0.6 SP.GR. gas
TABLE 10
ORIFICE SIZES
INPUT
RATING
BTUH
NUMBER
OF
BURNERS
MAIN BURNER ORIFICE
DRILL SIZE
NAT. GAS
LP GAS
40,000
60,000
80,000
100,000
120,000
140,000
2
3
4
5
6
7
45
45
45
45
45
45
56
56
56
56
56
56
TABLE 11
PART NUMBERS FOR REPLACEMENT ORIFICES
DRILL
SIZE
PART
NUMBER
DRILL
SIZE
PART
NUMBER
44
45
46
47
48
49
50
ORF00501
ORF00644
ORF00909
ORF00910
ORF01099
ORF00503
ORF00493
54
55
56
57
58
59
ORF00555
ORF00693
ORF00907
ORF00908
ORF01338
ORF01339
HIGH ALTITUDE DERATE
Input ratings (BTUH) of these furnaces are based on
sea level operation and should not be changed at eleva-
tions up to 2,000 ft.
If the installation is 2,000 ft. or above, the furnace in-
put rate (BTUH) shall be reduced 4% for each 1,000
ft. above sea level. The furnace input rate shall be
checked by clocking the gas flow rate (CFH) and mul-
tiplying by the heating value obtained from the local
utility supplier for the gas being delivered at the in-
stalled altitude. Input rate changes can be made by
adjusting the manifold pressure (min 3.0 - max 3.7 in.
W.C. - Natural Gas) or changing orifices (orifice change
may not always be required). If the desired input rate
cannot be achieved with a change in manifold pressure,
then the orifices must be changed. LP installations will
require an orifice change.
Installation of this furnace at altitudes above 2,000 ft.
(610m) shall be in accordance with local codes, the
Na-
tional Fuel Gas Code, ANSI Z223.1/ NFPA 54 or Na-
tional Standard of Canada, Natural Gas and Propane
Installation Code, CSA B149.1.
Installation of this fur-
nace at altitudes above 2,000 ft. (610m) shall be made
in accordance with the listed high Altitude Conversion
Kit available with this furnace.
IMPORTANT:
Re-install the propane orifices to the same depth as the
orifices supplied with the equipment.
See Table 14 for help in selecting orifices if orifice
change is required. Furnace input rate and tempera-
ture rise should be checked again after changing ori-
fices to confirm the proper rate for the altitude.
Installations above 4,000 feet may require a pressure
switch change. If required, use the BAYHALT*** Kit
(High Altitude Accessory Kit) listed in PRODUCT
DATA.
▲
WARNING
!
EXPLOSION HAZARD!
PROPANE GAS IS HEAVIER THAN AIR AND MAY
COLLECT IN ANY LOW AREAS OR CONFINED SPAC-
ES. IN ADDITION, ODORANT FADE MAY MAKE THE
GAS UNDETECTABLE EXCEPT WITH A WARNING
DEVICE. IF THE GAS FURNACE IS INSTALLED IN A
BASEMENT, AN EXCAVATED AREA OR A CONFINED
SPACE, IT IS STRONGLY RECOMMENDED TO CON-
TACT A GAS SUPPLIER TO INSTALL A GAS DETECT-
ING WARNING DEVICE IN CASE OF A GAS LEAK
.
NOTE:
The manufacturer of your furnace does NOT test
any detectors and makes no representations regarding
any brand or type of detector.
FINAL MANIFOLD PRESSURE SET-
TINGS (inches w.c.)
FUEL
PRESSURE
NATURAL GAS
3.5" W.C.
LP GAS
10.5" W.C.
TABLE 12