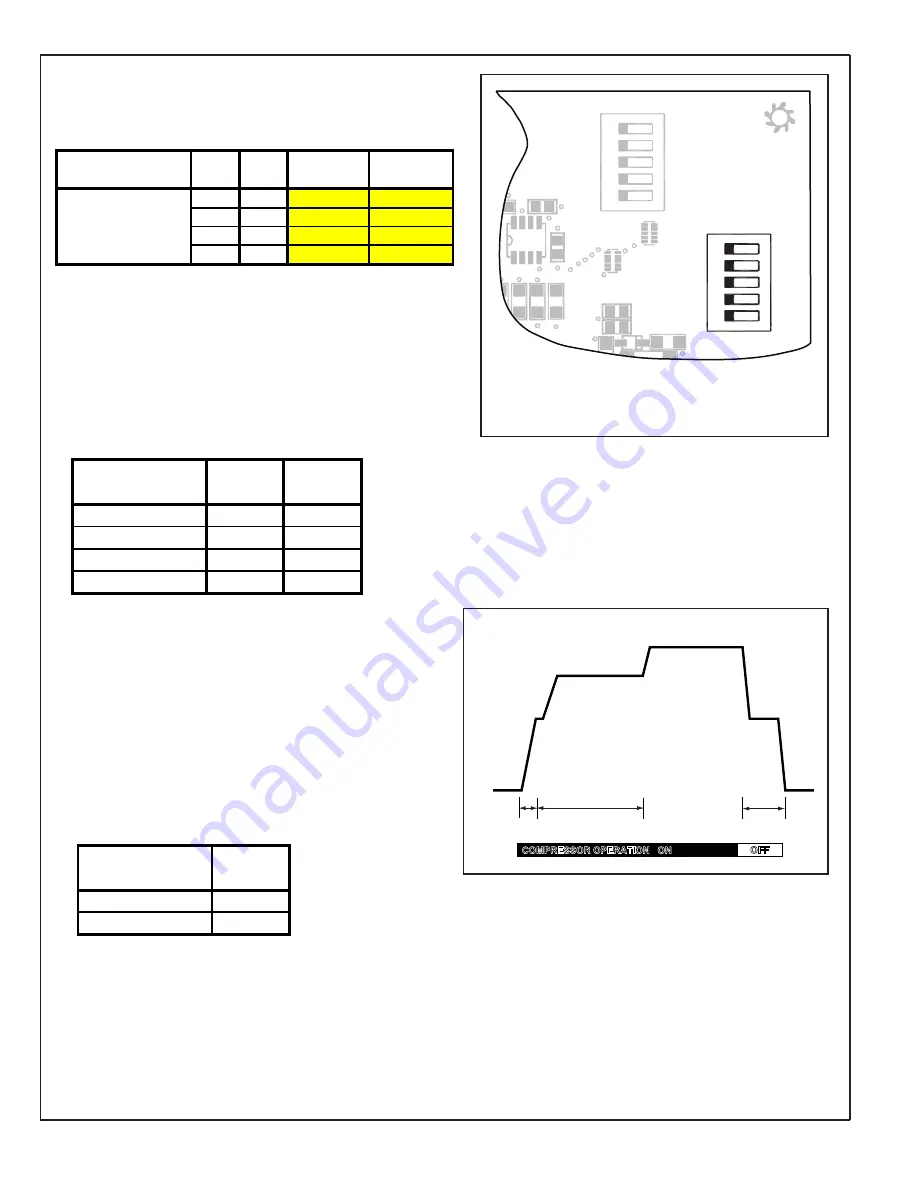
AM7A0C36H31-SF-1A
8
dip Switch S2
Set the S2-1 and S2-2 dip switches for the
•
Cooling and Heating CFM/Ton.
Set the S2-3 and S2-4 dip switches for the Cool
•
Off Delay.
COOL
OFF
DELAY
S2
‐
3
S2
‐
4
1.5m
@
100%
OFF
OFF
NO
DELAY
OFF
ON
3m
@
50%
ON
OFF
ENHANCED
ON
ON
AIRFLOW
MODE
S2
‐
5
*TORQUE
OFF
CONSTANT
CFM
ON
Set the S2-5 dip switch for the airflow mode.
•
Indoor Blower Timing
This ENHANCED MODE selection provides a
ramping up and ramping down of the blower
speed to provide improved comfort, quietness,
and potential energy savings. The graph on the
right shows the ramping process.
OFF
OFF
50%
80%
100% if necessary
50%
Dehumidify
Fast Coil Cooling
Efficiency
7.5
minutes
3
minutes
1
minute
FAN OPERATION (CFM)
COMPRESSOR OPERATION ON
OFF
as required
S2
1
1
1
2
3
4
5
1
2
3
4
5
HP
2 (Compressor)
2 (Stages)
AC (System)
}
OUTDOOR
Capacity (Tons)
OUTDOOR
}
Torque
CFM/Ton
Cool Off Delay
}
INDOOR
CFM
+12V
R13
R14
R1
R4
1
U1
R NET 1
S1
on
on
S2
R NET 2
R
6
C
22
C
19
C
15
C
12
C
18
C
21
C10
D9
L1
R22
Airflow Control (AFC)
* Torque mode is optional and is recommended for high static
applications. High static conditions dramatically increase energy
consumption with variable speed motors. Evaluate the blower
performance table in relationship to the duct system to determine
the benefit of each installation.
* Torque mode will reduce airflow when static is above approxi-
mately 0.4" water column.
* All heating modes default to Constant CFM.
INDOOR
MODEL
S2
‐
1
S2
‐
2
COOLING
CFM/TON
HEATING
CFM/TON
OFF
OFF
370
420
OFF
ON
350
400
ON
OFF
390
440
ON
ON
410
450
*
May
be
"A"
or
"T"
*AM7A0C36H31SA