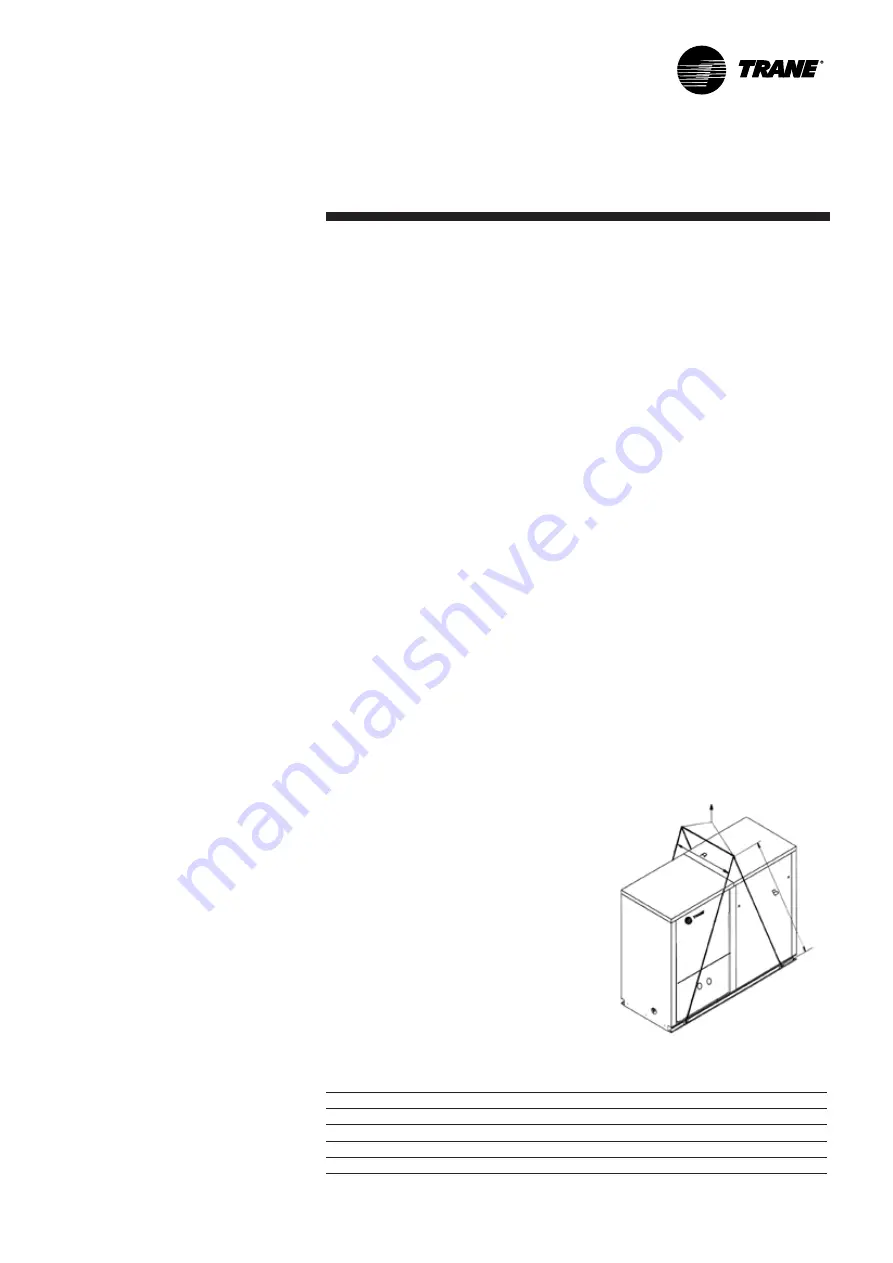
CGWH-SVX01D-E4
5
Installation
Unit nameplate
The unit nameplate gives the
complete model reference numbers.
The unit power rating is shown, and
power supplies should not deviate by
more than 5 % from the rated power.
Compressor motor amperage is
shown in box I.MAX.
The customer’s electrical installation
must be able to withstand this
current.
Installation instructions
Foundations
No special foundations are required,
provided the supporting surface is
flat and level, and can withstand the
weight of the unit.
Isolation rubber pads
They are supplied as standard with
the machine, and should be placed
between the supporting floor and
the unit to isolate the unit from the
ground (4 pads for the sizes 115 to
125 and 6 pads for the sized 225
to 250). To reduce vibration, Trane
recommends the use of neoprene
pads (not included) but does not
allow the use of spring isolators.
Water drain hole
Install a drain hole wide enough to
drain away water from the unit in the
event of shut-down or repair.
Clearance
Respect recommended clearance
around the unit to allow maintenance
operation to take place without
obstruction. Submittals are available
on request from your local Trane
Sales Office.
Handling
A specific lifting method is
recommended as follows:
1. 4 lifting points are built into the
unit.
2. Slings and spreader bar to be
provided by rigger and attached
to the 4 lifting points.
3. Minimum rated lifting capacity
(vertical) of each sling and
spreader bar shall be no less
than the tabulated unit shipping
weight.
CAUTION!
The plates welded at the end of the
bases must not be used for handling.
Use the ones at 237 mm from the
ends.
Figure 1 - Handling
Table 1 - Dimensions of recommended slings and swing-bar :
Unit size
115
120
125
225
230
235
240
250
A (mm)
1400
1400
1400
1400
1400
1400
1400
1400
B (mm)
1900
1900
1900
1900
1900
1900
1900
1900
Weight (kg) CGWH
412
444
476
668
702
739
803
873
Weight (kg) CCUH
389
416
443
626
655
679
757
815