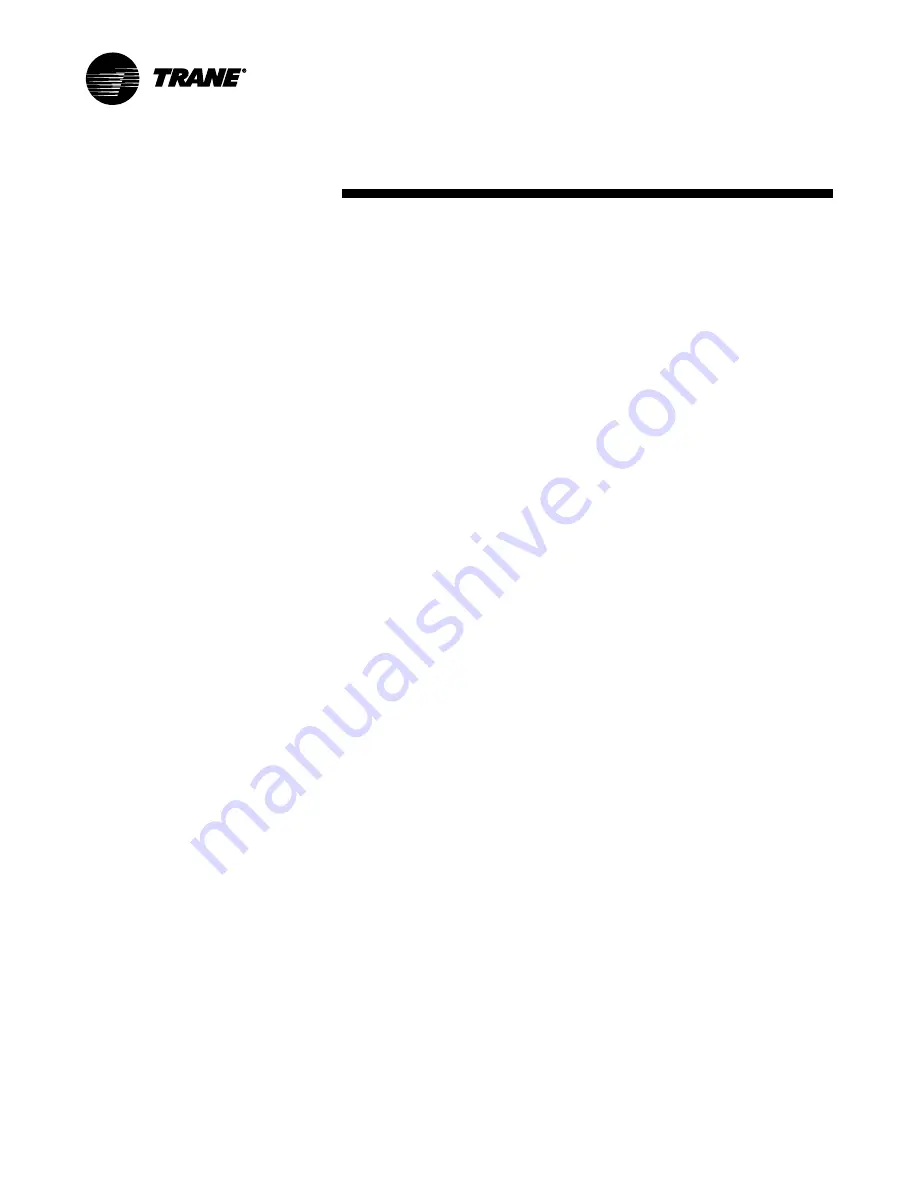
CDQ-SVX01A-EN
7
Operation
WARNING
Rotating Components!
Disconnect all electrical power,
including remote disconnects before
servicing. Follow proper lockout/
tagout procedures to ensure the
power can not be inadvertently
energized. Secure drive sheaves to
ensure rotor cannot freewheel.
Failure to secure drive sheaves or
disconnect power before servicing
could result in death or serious
injury.
CAUTION
Do Not Exceed Maximum
Airflow!
Do not exceed the maximum rated
airflow. Excess pressure could
accelerate wear and cause damage
to the wheel.
CDQ Wheel Startup
1. Set seals. See “Seal Adjustment”
on page 17.
2. With hands and objects away
from moving parts, activate the
wheel and confirm the wheel
rotation. The correct rotation
direction is counter-clockwise as
viewed from the pulley side.
3. Verify rotational speed 8-10
rotations per hour. The wheel
should be a 1/4 turn in 100-150
seconds.
4. If the wheel has difficulty starting,
confirm seals adjustment and belt
tension. See “Seal Adjustment”
on page 17. If belt slips, see
“Drive Belt Adjustment/
Replacement” on page 16.
5. Start and stop the wheel several
times to confirm seal adjustment
and proper belt tracking on the
wheel rim.
WARNING
Hazardous Voltage!
Disconnect all electric power,
including remote disconnects before
servicing. Follow proper lockout/
tagout procedures to ensure the
power can not be inadvertently
energized. Failure to disconnect
power before servicing could result
in death or serious injury.
6. If the wheel has difficulty starting,
turn off the power and inspect for
excessive interference between
the wheel surface and the four
diameter seals. To correct, loosen
the diameter seal adjusting
screws and back the diameter
seals away from the surface of
the wheel. Apply power to
confirm that the wheel rotates
freely. Readjust and tighten the
seals according to instructions in
“Seal Adjustment” on page 17.
7.
Damper actuators (if so equipped):
Stroke the actuators to observe
full open and full closure of
dampers. Adjust the actuator and/
or linkage to prevent “over-
stroking” so excessive pressure is
not placed on the damper at the
full open or full closed position.
Note: Do not exceed the maximum
rated airflow for the wheel. The
pressure drop across the wheel is not
to exceed 1.5 inches w.g.