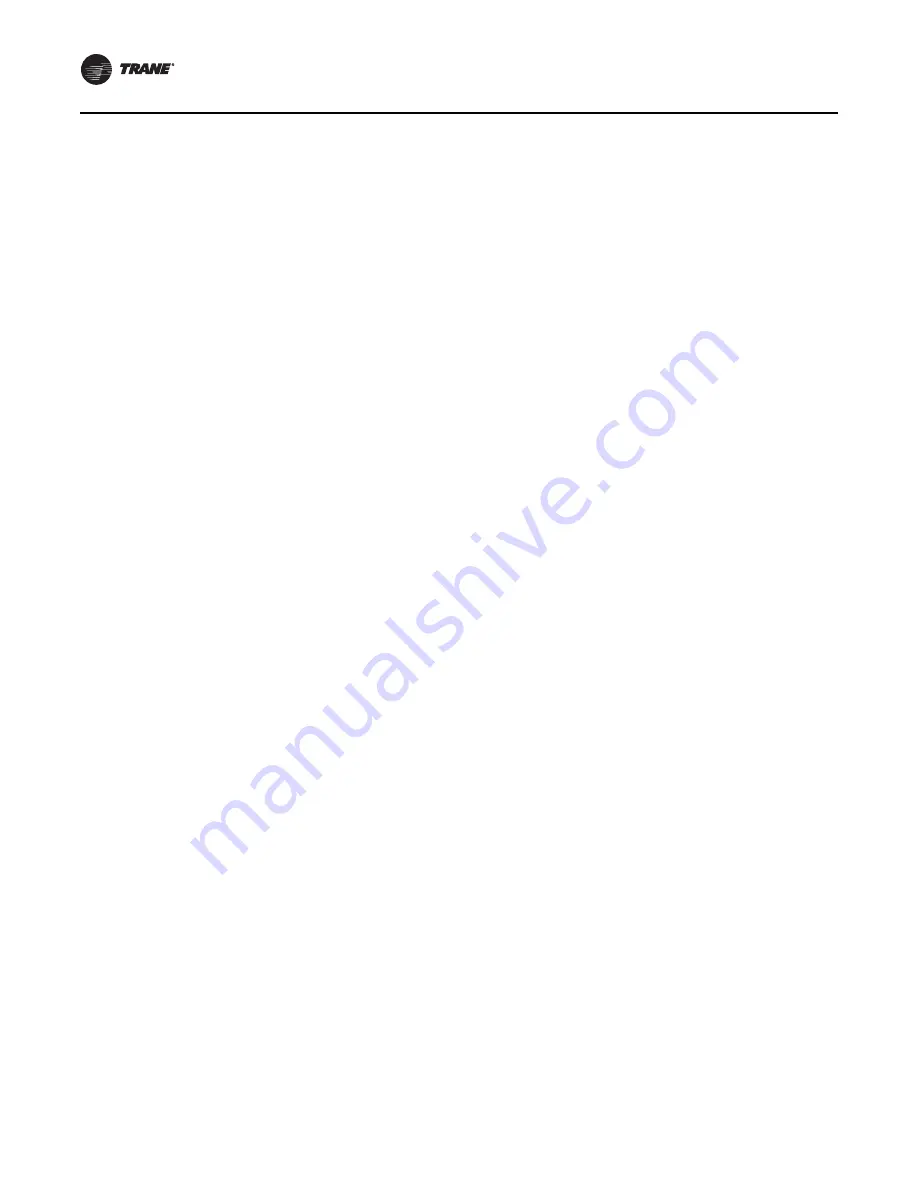
Installation
32
AH-SVX008C-EN
System Settings and
Adjustments
Low/High Pressure Limit Switch
Air conditioning systems using DX refrigerant are
equipped with hermetically sealed high-pressure and low-
pressure switches. These switches are pre-set by the
manufacturer and cannot be adjusted.
R407C Pressure Switch Settings
High-pressure switch: opens at 410 psig and has a manual
reset.
Low-pressure switch: opens at 10 psig (± 4) and closes at
32 psig (± 5) and has an automatic reset.
Head Pressure Controls-Air Cooled
Systems
Condenser Fan Cycling (Condenser Model
SCS-AA, 0°F)
Used for outdoor installations where ambient condenser
air inlet temperatures are 0°F or higher, this method
utilizes a high-pressure differential control switch with
SPST (Single Pole, Single Throw) contacts and an
automatic reset. The switch activates the condenser fan
contactor when the dis- charge pressure reaches a
predetermined value to maintain the condensing
temperature.
See the Head Pressure Controls section of the SCS Series
Remote Air Cooled Condensers IOM for information about
the fan cycling pressure control settings (cut-in and cut-out
pressures) for the supported refrigerants. Note that the
pressure values vary according to both the refrigerant type
and the number of fans in the SCS unit.
Condenser Multi-Speed Fan Switch (Model
HES-CAA, 0°F)
Used for indoor installations where ambient condenser air
inlet temperatures are 0°F or higher, the condenser fan
speed switch senses refrigerant discharge pressure and
changes the condenser fan speed to maintain proper
condenser pressures.
The condenser fan speed switch changes the fan from low
to high speed when pressure rises and returns the fan
from high speed to low speed when the pressure lowers.
Variable Condenser Fan Speed (Condenser
Model SCS-SA, -20°F)
Used for outdoor installations where ambient
temperatures may fall to -20°F, a variable speed condenser
fan motor control is used to maintain head pressure. The
variable speed motor is located closest to the header end
of the condenser. The fan speed control is a continual
modulation of the motor's speed. The controller is factory
installed in the outdoor condenser/condensing unit. The
fan speed controller requires no adjustment.
The fan speed controller will automatically control the
head pressure at a level to maintain design refrigerant
discharge pressures. On systems with more than one fan
on the condenser, the remaining motors cycle on and off
based on pressure.
Intelligent Control (Condenser Model SCS-EC
Only, -20°F)
Used for outdoor installations where ambient condenser
air inlet temperatures may fall to -20°F, intelligent pressure
control is designed to maintain discharge pressure by
constantly modulating condenser fan speed. SCS outdoor
condensers are equipped with highly efficient,
electronically commutated (EC), axial fan(s). The EC fan
speed is infinitely variable up to full speed. The control
system uses refrigerant pressure transducer(s) to monitor
refrigerant discharge pressure and control the EC fan(s) to
the precise speed needed to maintain design refrigerant
discharge pressures.
Flooded Head Pressure Control
(Condenser Model SCS-AA With Fan Cycling, -30°F)
Used for outdoor installations where ambient condenser
air inlet temperatures may fall to -30°F, flooded head
pressure control is designed to maintain head pressure
during low ambient conditions. A head pressure control
valve and a receiver are used in the refrigeration circuit to
back up liquid refrigerant into the condenser coil. The head
pressure control valve is a 3-way modulating valve
controlled by discharge pressure.
When the A/C unit begins to operate, the discharge
pressure rises (to approximately 320 psig for R407C) and
the condenser fan is cycled on, as described in
“Condenser Fan Cycling (Condenser Model SCS-AA, 0°F),”
p. 32
. When ambient temperature drops, the discharge
pressure drops also. When the discharge pressure drops,
the head pressure control valve diverts discharge gas
away from the condenser to the receiver. Liquid flow from
the condenser is restricted, causing liquid to back up in the
condenser.
Flooding the condenser reduces the area available for heat
transfer. The desired result is to increase the pressure into
the condenser, maintaining a minimum discharge
pressure during low ambient operation, thus ensuring
proper condensing temperature. The head pressure
control valve requires no adjustment.
While the fan is running, the flooded head pressure control
valve modulates the amount of discharge gas entering the
receiver. As the pressure increases, the valve diverts more
discharge gas to the condenser, allowing more liquid to
flow from the condenser to the receiver.
When using this method of head pressure regulation there
must be enough refrigerant in the system to ensure
adequate charge at the lowest expected ambient
temperature in which the system will be operating. A
receiver is used to store the extra refrigerant when the
condenser is not using it.
Summary of Contents for CeilAir CW
Page 51: ......