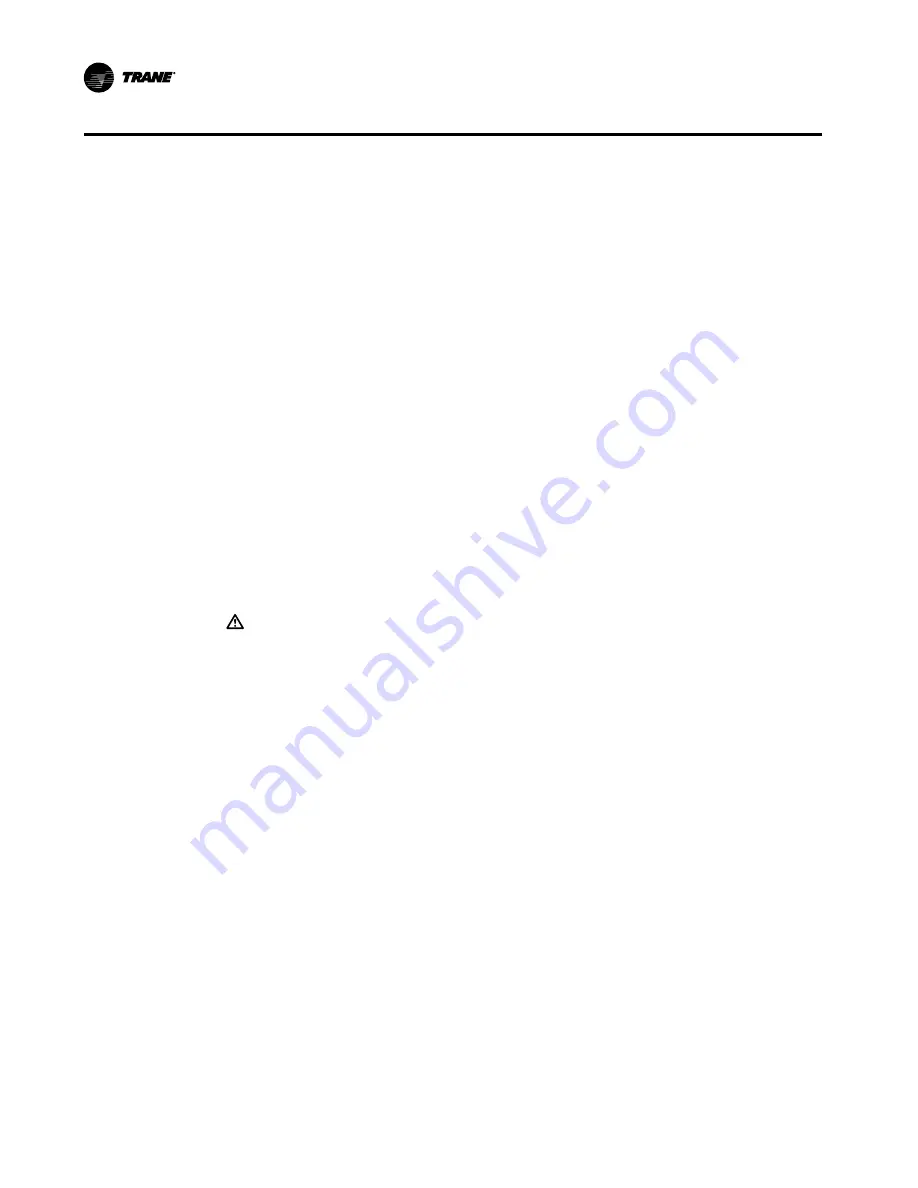
fore the chiller can be returned to operation.
Diagnostic Codes
A Latching diagnostic will shut down the machine or a part of the machine if so in-
dicated. A latching diagnostic will require a manual reset to restore operation. A
Non-latching diagnostic will shut down the machine or a part of the machine if so in-
dicated. A non-latching diagnostic will automatically reset when the condition causing
the diagnostic goes away. If a diagnostic is informative only, no machine action is tak-
en except to load a diagnostic code into the last diagnostic register. Unless otherwise
stated, all active diagnostics will be lost on loss of power.
Leak Testing Procedure
To leak-test the CVGF, weigh a one-pound charge of trace gas and bring the pressure
up to a maximum of 75 psig (517 kPa) using dry nitrogen. This pressure has been
found to be adequate to find leaks in a CVGF when using a sensitive electronic leak
detector. Set the scale to “medium” which corresponds to a 1/2-ounce (.015l) per year
leak rate and probe all joints thoroughly. Be sure and relieve the pressure in the unit
before evacuation or leak repair. Local codes take precedence when conducting evac-
uation.
WARNING
Hazard of Explosion!
Use only dry nitrogen with a pressure regulator for pressurizing unit. Do not use acet-
ylene, oxygen or compressed air or mixtures containing them for pressure testing. Do
not use mixtures of a hydrogen containing refrigerant and air above atmospheric pres-
sure for pressure testing as they may become flammable and could result in an explo-
sion. Refrigerant, when used as a trace gas should only be mixed with dry nitrogen
for pressurizing units. Failure to follow these recommendations could result in death
or serious injury or equipment or property-only damage.
Taking an Oil Sample
To obtain an accurate oil sample, the chiller must be operating for a minimum of 30
minutes. An approved oil sample cylinder for R134a should be used. Make sure the
upstream oil filter isolation angle valve is completely backseated in order to close the
1/4 inch Schrader valve port. Attach a low loss hose or line with a Schrader valve de-
pressor to the oil sampling 1/4 inch Schrader valve located on the upstream oil filter
isolation valve.
Attach the other end of the hose or the line to the oil-sampling cylinder. Evacuate the
cylinder and hose or line to remove any non-condensables or moisture. Open the
valve on the sample cylinder. Turn the upstream oil isolation angle valve stem approx-
imately one turn clockwise to allow oil under pressure to enter the sample cylinder.
Weigh the cylinder as the oil is being transferred and shut off the cylinder valve when
the desired weight of oil has been transferred. Backseat the angle valve to shut off oil
flow and remove the hose from the Schrader valve. Be sure to replace the Schrader
and angle valve cap and secure them when sampling is complete. Recover the oil and
refrigerant from the oil sample hose or line with an approved R134a recovery unit.
When oil analysis indicates the need to change the oil (high acidity, moisture, and so
CVGF-SVX03B-EN
118
Periodic Maintenance
Summary of Contents for CVGF1000
Page 6: ...TRMM Tracer Communications UCP Unit Control Panel CVGF SVX03B EN 6 General Information...
Page 125: ......
Page 126: ......
Page 127: ......