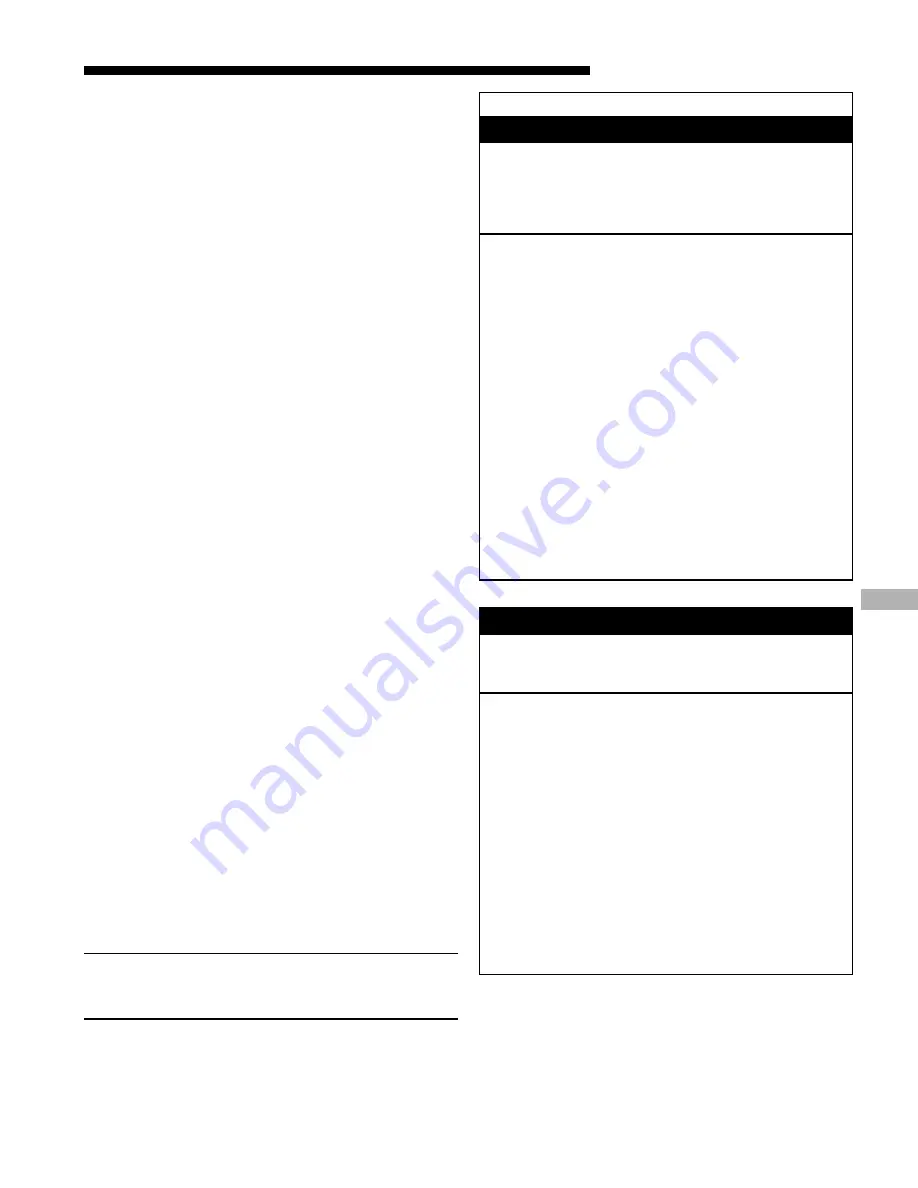
18-CD20D1-18
23
Installer’s Guide
Failure to follow safety warnings exactly, could result
in a fire or explosion causing property damage,
personal injury or loss of life.
— Do not store or use gasoline or other flammable
vapors and liquids in the vicinity of this or any
other appliance.
— WHAT TO DO IF YOU SMELL GAS
• Do not try to light any appliance.
• Do not touch any electrical switch;
do not use any phone in your building.
• Immediately call your gas supplier from a
neighbor’s phone. Follow the gas supplier’s
instructions.
• If you cannot reach your gas supplier,
call the fire department.
— Installation and service must be performed by
a qualified installer, service agency or the gas
supplier.
▲
WARNING
!
ABNORMAL CONDITIONS
1. EXCESSIVE COMBUSTION PRESSURE (WIND IN
EXCESS OF 40 M.P.H.) VENT OR FLUE BLOCKAGE
If pressure against induced draft blower outlet becomes
excessive, the pressure switch will open and shut off the
gas valve until acceptable combustion pressure is again
available.
2. LOSS OF FLAME
If loss of flame occurs during a heating cycle, or flame is
not present at the sensor, the flame control module will
close the gas valve. The flame control module will then
recycle the ignition sequence, then if ignition is not
achieved, it will shut off the gas valve and lock out the
system.
3. POWER FAILURE
If there is a power failure during a heating cycle, the
system will restart the ignition sequence automatically
when power is restored, if the thermostat still calls for heat.
4. GAS SUPPLY FAILURE
If loss of flame occurs during a heating cycle, the system
integrated control module will recycle the ignition
sequence, then if ignition is not achieved, the integrated
control module will shut off the gas valve and lock out
the system.
5. INDUCED DRAFT BLOWER FAILURE
If pressure is not sensed by the pressure switch, the
contacts will remain open and not allow the gas valve to
open, therefore the unit will not start. If failure occurs
during a running cycle, the pressure switch contacts will
open and the gas valve will close to shut the unit down.
6. RESET AFTER LOCKOUT
When the integrated control module has shut the system
down and gone into lockout, the system must be manu-
ally reset before the unit will restart. To reset, turn the
system power off, then on, then off and then on again
within 30 seconds. This may be done at the unit’s power
source or at the thermostat.
The system will not reset
unless the procedure off-on-off-on is completed within
30 seconds.
Carbon monoxide, fire or smoke can cause serious bodily
injury, death, and/or property damage.
A variety of potential sources of carbon monoxide can be
found in a building or dwelling such as gas-fired clothes
dryers, gas cooking stoves, water heaters, furnaces and
fireplaces. The U.S. Consumer Product Safety Commission
recommends that users of gas-burning appliances install
carbon monoxide detectors as well as fire and smoke detec-
tors per the manufacturers installation instructions to help
alert dwelling occupants of the presence of fire, smoke or
unsafe levels of carbon monoxide. These devices should be
listed by Underwriters Laboratories, Inc.
Standards for
Single and Multiple Station Carbon Monoxide Alarms,
UL 2034
or CSA International Standard,
Residential
Carbon Monoxide Alarming Devices,
CSA 6.19
NOTE:
The manufacturer of your furnace does not test any detec-
tors and makes no representations regarding any brand or
type of detector.
▲
WARNING
!
The following warning complies with State of California law, Proposition 65.
This product contains fiberglass wool insulation!
Fiberglass dust and ceramic fibers are believed by the
State of California to cause cancer through inhalation.
Glasswool fibers may also cause respiratory, skin, or
eye irritation.
PRECAUTIONARY MEASURES
●
Avoid breathing fiberglass dust.
●
Use a NIOSH approved dust/mist respirator.
●
Avoid contact with the skin or eyes. Wear long-sleeved,
loose-fitting clothing, gloves, and eye protection.
●
Wash clothes separately from other clothing: rinse
washer thoroughly.
●
Operations such as sawing, blowing, tear-out, and
spraying may generate fiber concentrations requiring
additional respiratory protection. Use the appropriate
NIOSH approved respirator in these situations.
FIRST AID MEASURES
Eye Contact
–
Flush eyes with water to remove dust.
If symptoms persist, seek medical
attention.
Skin Contact –
Wash affected areas gently with soap
and warm water after handling.