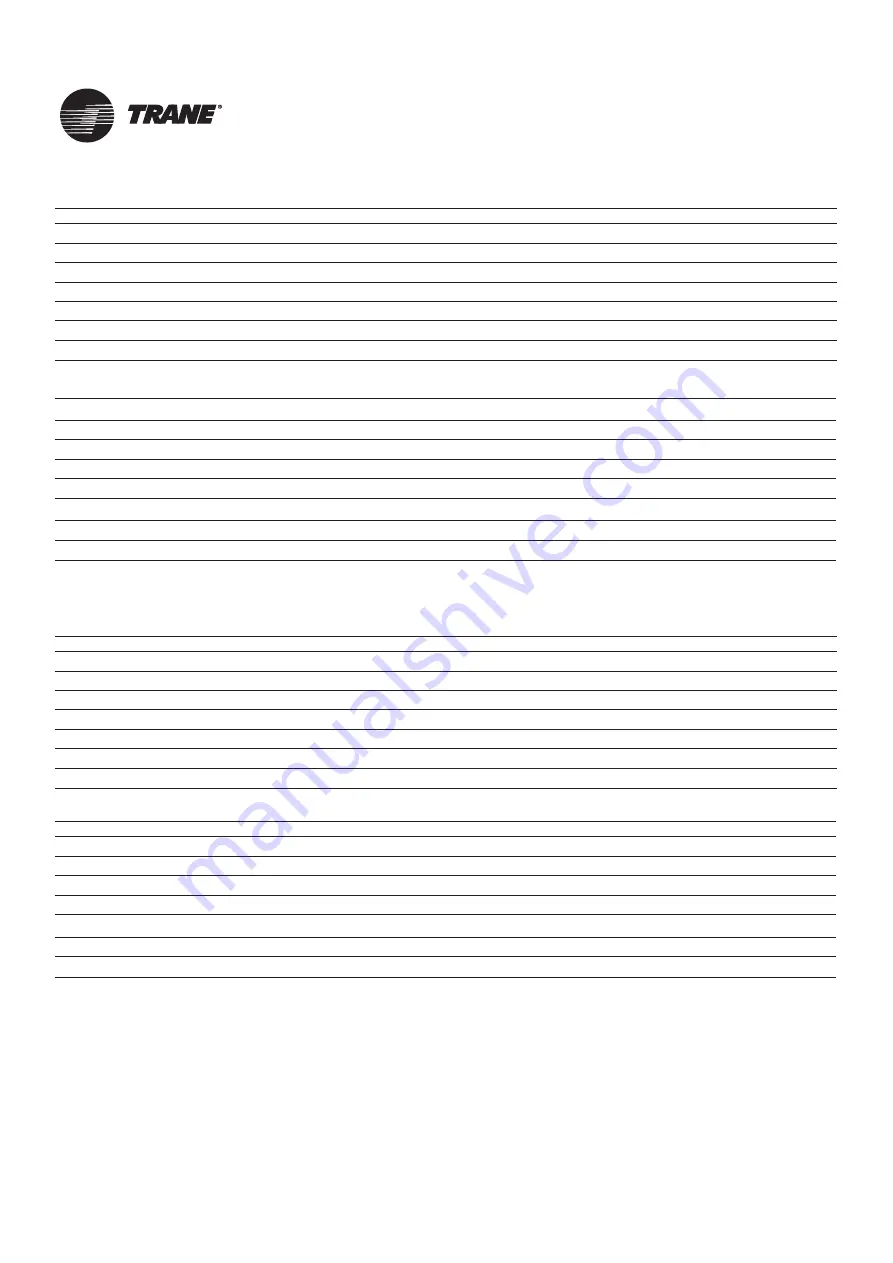
PKG-SVX19B-E4
12
CHILLED WATER DIRECT EXPANSION UNITS WITH EC BACKWARD CURVED BLADE FANS
Model EDWV - EUWV
1106A
2109A
2113A
2216A
2218A
Height
mm
1960
1960
1960
1960
1960
Width
mm
1010
1310
1720
2171
2171
Depth
mm
750
865
865
865
865
Weight
kg
280
430
575
714
714
Number of refrigerant circuits
1
1
1
2
2
Number of compressors
1
2
2
2
2
Power supply voltage
V
400V/3ph+N/50Hz
Model EDWV
4222A
4225A
4228A
Height
mm
2175
2175
2175
Width
mm
2580
2580
2580
Depth
mm
865
865
865
Weight
kg
996
1020
1120
Number of refrigerant circuits
2
2
2
Number of compressors
4
4
4
Power supply volatge
V
400V / 3 ph+N / 50 Hz
CHILLED WATER DIRECT EXPANSION UNITS WITH BACKWARD CURVED BLADE FANS
Model EDWB - EUWB
1106A
2109A
2113A
2216A
2218A
Height
mm
1960
1960
1960
1960
1960
Width
mm
1010
1310
1720
2171
2171
Depth
mm
750
865
865
865
865
Weight
kg
310
430
575
714
714
Number of refrigerant circuits
1
1
1
2
2
Number of compressors
1
2
2
2
2
Power supply voltage
V
400V/3ph+N/50Hz
Model EDWB
4222A
4225A
4228A
Height
mm
2175
2175
2175
Width
mm
2580
2580
2580
Depth
mm
865
865
865
Weight
kg
996
1020
1120
Number of refrigerant circuits
2
2
2
Number of compressors
4
4
4
Power supply volatge
V
400V/3ph+N/50Hz