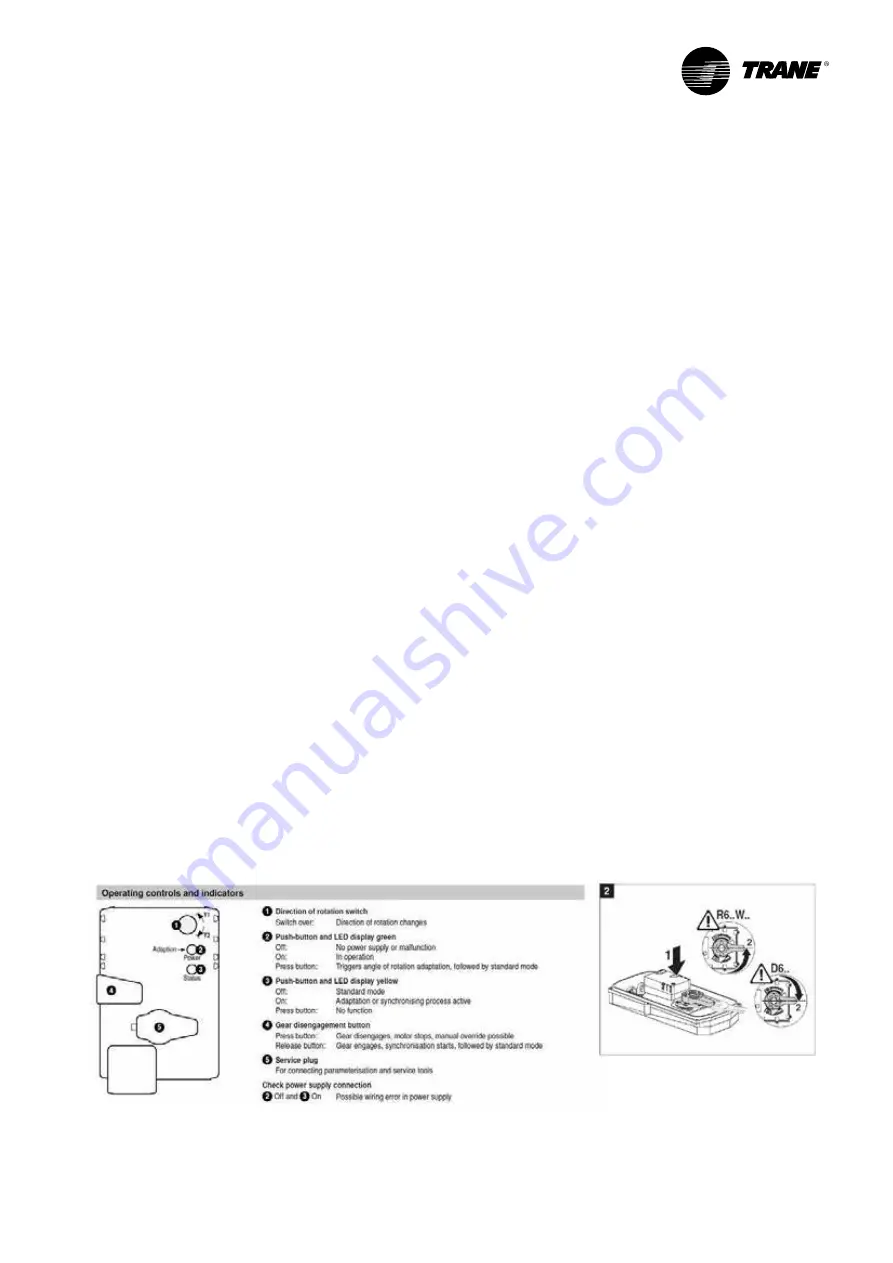
CTV-SVX009D-GB
31
11
UNT-PRC002-GB
Sound power levels
Discharge
Measurement conditions:
Measurements taken in a room adjacent to the room containing the FWD, at the outlet of the rectangular duct (1.5 m
long) fixed to its discharge opening.
Fan
Power level in dB(A), per Hz frequency band
Overall power
Unit
speed
125
250
500
1000
2000
4000
8000
dB(A)
1
55
50
42
37
37
31
30
46
FWD 08
2
57
54
47
40
30
38
40
50
3
58
57
50
42
32
40
43
53
1
57
51
45
42
34
33
28
48
FWD 10
2
58
54
48
45
38
39
35
51
3
60
58
50
48
40
42
39
54
1
57
51
45
42
34
33
28
48
FWD 12
2
58
54
48
45
38
39
35
51
3
60
58
50
48
40
42
39
54
1
56
62
50
48
39
38
36
56
FWD 14
2
61
66
55
53
47
46
45
60
3
63
69
58
56
50
50
49
63
1
57
63
51
49
40
39
37
57
FWD 20
2
61
66
55
53
47
46
45
60
3
63
69
58
56
50
50
49
63
Intake
Measurement conditions:
Measurements taken at the horizontal air intake.
Fan
Power level in dB(A), per Hz frequency band
Overall power
Unit
speed
125
250
500
1000
2000
4000
8000
dB(A)
1
56
55
55
53
46
45
42
57
FWD 08
2
63
62
60
60
53
53
53
64
3
66
65
63
62
56
55
57
67
1
62
58
55
58
51
48
44
61
FWD 10
2
66
63
60
62
56
55
52
66
3
70
67
63
65
59
59
57
69
1
62
58
55
58
51
48
44
61
FWD 12
2
66
63
60
62
56
55
52
66
3
70
67
63
65
59
59
57
69
1
66
65
65
65
57
50
46
68
FWD 14
2
73
72
69
71
64
59
57
74
3
78
76
73
75
69
64
63
78
1
68
72
64
64
56
52
50
69
FWD 20
2
76
76
68
71
65
61
61
75
3
78
79
71
74
69
66
66
78
Optional Free-Cooling
Note for installation
All Submittal, lifting diagram, neoprene pads positioning
and wiring diagrams have been supplied with chiller
order.
The maximum pressure of the Glycol side when unit
is equipped with free cooling is 400 kPa for Glycol
free option or 600kPa for Direct free cooling except on
evaporator side for glycol free 1000 kPa Refer to unit
nameplate for rated value.
Pump operation with Glycol free : it is requested to have
a minimum water side pressure of 250 kPa to avoid
cavitation.
Glycol free option : To avoid component damage, a filter
(1 mm mesh) must be supplied by the customer and
installed at the unit inlet.
Unit is shipped without glycol content on the free cooling
circuit.
Free cooling loop venting must be performed by using
Manual override mode to run the free cooling pump and
opening free cooling and closing bypass valve.
At 10 to 20°C ambient, the expansion shall be pressurized
at 250 kpa. It should be checked when glycol loop is not
yet filled or glycol pressure is near zero.
All Free-cooling units must be freeze-protected with at
least 30% Ethylene Glycol in the cooling loop circuit
which is the most convenient percentage in order to
protect the unit against freezing. Upon receipt, make sure
that there is no remaining test water in the free cooling
circuit as it may freeze during winter periods.
Protection coverage with 30% Ethylene Glycol:
- Freezing point without burst effect = -13°C
- Freezing point with burst effect = -50°C.
Water can be trapped in BPHE and specific care must be
taken to remove it completly from BPHE during off mode
if drainage is the winter protection chosen.
The free cooling option circuit consists of copper,
carbon steel, cast iron, zinc, synthetic rubber, brass, and
Aluminum AA3102, AA3003, AA4045 in addition to other
materials that may be in the building loop connected
to the chiller. The inhibited glycol solution should be
selected at desired concentration to ensure adequate
inhibitor content. It is not advised to dilute a stronger
concentrate due to inhibitor dilution. Glycol fluid should
be free from foreign solid particles. A maintenance
schedule should be selected per the glycol manufacturer’s
requirements to insure adequate protection during
product usage.
Notice: Equipment Damage!
Failure to follow instructions below could cause
equipment damage.
DO NOT USE UNTREATED WATER. Glycol solution
must be utilised with the Direct Free Cooling option.
Glycol percentage should be based on freeze avoidance
requirements. The glycol solution requires an inhibitor
package to be carefully chosen with the aid of a qualified
water treatment specialist to abate corrosion in a mixed
metal system.
The building glycol loop should not be vented to
atmosphere. A closed system is required to limit
oxidation potential within the loop.
Make-up water should be avoided.
Free cooler by-pass valve adjustment
For intervention on free cooler by-pass valve it is
recommended to consult the valve service literature.
For every new referencing of the motor end travel, an
adaptation of the motor should be done by pushing
button 2.
To change the bypass percentage follows below
procedure:
− No tuning is needed on free cooling valve which
always stays on full opening/closure.
− For bypass valve Belimo, minimum opening
can be adjusted by pushing the release button
(4) and by turning handle 5 to 50% opening for
instance (45°)