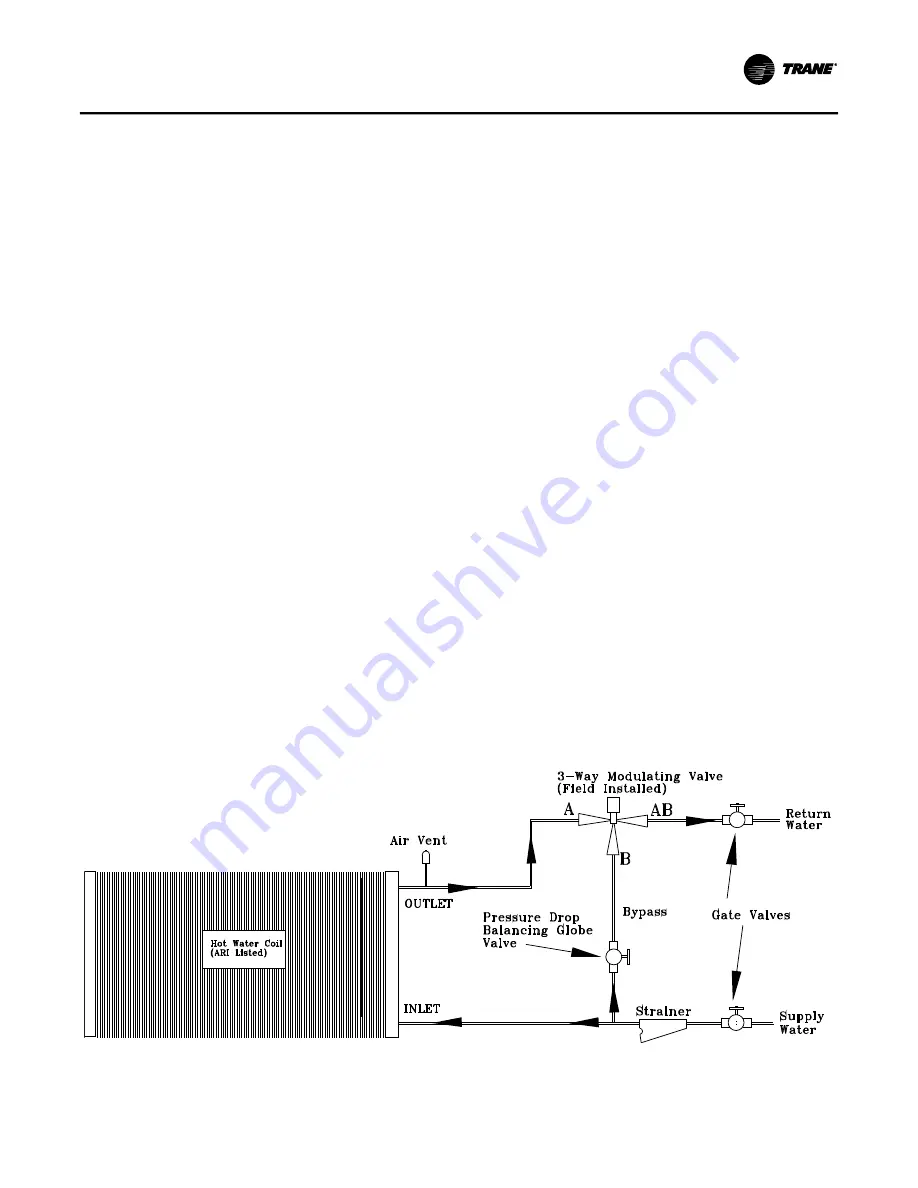
Installation
RT-SVX35H-EN
39
Important:
The valve actuators are not waterproof.
Failure to protect the valve from moisture
may result in the loss of heating control.
1. Support all field-installed piping independently from
the heating coil.
2. Use swing joints or flexible connectors adjacent to the
heating coil. (These devices will absorb the strains of
expansion and contraction.)
3. Install the 2-way valve in an upright position. Ensure
that the valve’s location lends itself to serviceability.
4. Pitch the supply and return steam piping downward 1"
per 10' of run in the direction of flow.
5. All return lines and fittings must be equal to the
diameter of the "outlet" connection on the steam
coil(s). If the steam trap connection is smaller than the
coil "outlet" diameter, reduce the pipe size between the
strainer and the steam trap connections only.
6. Install a 1/2" 15 degree swing-check vacuum breaker at
the top of the return coil header using the tapped pipe
connection. Position the vacuum breaker as close to
the coil as possible.
Note:
Vacuum breakers should have extended lines from
the vent ports to the atmosphere or connect each
vent line to the return pipe on the discharge side of
the steam traps.
7. Install a "Gate" type valve in the supply branch line as
close as possible to the steam main and upstream of
any other device.
8. Install a "Gate" type valve in the return branch line as
close as possible to the condensate return main and
downstream of any other device.
9. Install a strainer as close as possible to the inlet of the
control valve and steam trap(s).
10. Steam trap selection should be based on the
maximum possible condensate flow and the
recommended load factors.
11. Install a Float-and-Thermostatic (FT) type trap to
maintain proper flow. They provide gravity drains and
continuous discharge operation. FT type traps are
required if the system includes either;
a. An atmospheric pressure/gravity condensate
return;
or,
b. A potentially low pressure steam supply.
12. Position the outlet or discharge port of the steam trap
at least 12" below the outlet connection on the coil(s).
This will provide adequate hydrostatic head pressure
to overcome the trap losses and assure complete
condensate removal.
Casings 4, 5, 6 and 9 units
Utilizes two steam coils stacked together. These two coils
must be piped in a parallel arrangement. The steps listed
below should be used in addition to the previous steps.
illustrates the recommended piping
configuration for the steam coils.
13. Install a strainer in each return line before the steam
trap.
14. Trap each steam coil separately as described in
to prevent condensate backup in one or
both coils.
15. In order to prevent condensate backup in the piping
header suppling both coil sections, a drain must be
installed utilizing a strainer and a steam trap as shown
in
Figure 22. Hot water piping configuration for W_HE casings 2 - 6
Summary of Contents for IntelliPak WEHE Series
Page 15: ...General Information RT SVX35H EN 15 Figure 1 Unit component layout and ship with locations...
Page 17: ...Installation RT SVX35H EN 17 Figure 2 Typical control module location...
Page 44: ...Installation 44 RT SVX35H EN Figure 27 Typical field power wiring for W_HE casings 2 through 6...
Page 56: ...Installation 56 RT SVX35H EN Figure 32 Wiring notes for CV controls...
Page 60: ...Installation 60 RT SVX35H EN Figure 35 Wiring notes VAV...
Page 68: ...System Start up 68 RT SVX35H EN Figure 38 Typical fenwall ignition control system...
Page 69: ...System Start up RT SVX35H EN 69 Figure 39 Typical Fenwall ignition control system...