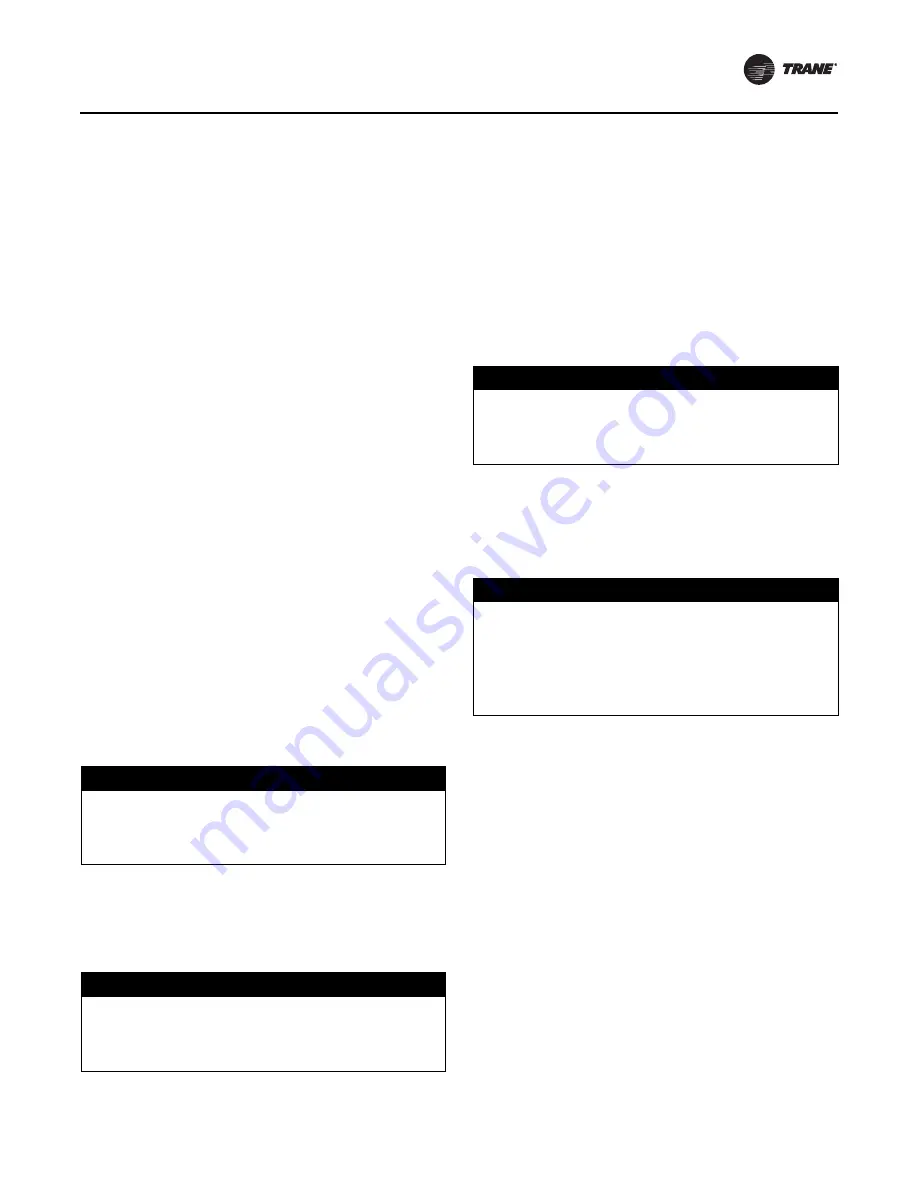
Maintenance Procedures
ARTC-SVX002A-EN
51
Weekly
Weekly inspection is a continuation and elaboration of
daily best practice:
•
Inspect touchscreen interface panel for alarm status
and additions to the alarm history. (Do not clear
alarms as this is a very important performance
record if troubleshooting problems occur.)
•
Listen for excessive vibrations or motor noise. This
usually signals a loose brace or section of piping.
•
Measure all refrigerant static pressure on any idle
circuits. Record any significant changes or
reductions in pressure.
•
Clean strainers weekly during initial weeks after
initial start up until water quality has been reliably
established. Thereafter, inspect and clean strainers
at least monthly.
Monthly
The monthly maintenance inspection examines many
items that generally require frequent attention. This
routine event identifies small problems early before they
can become big problems requiring serious repair and
refurbishment:
1. Remove the strainer on the inlet water pipe to the
chiller and verify that it is clean and free of debris.
2. Clean the strainer’s mesh screen by back-washing with
high water velocity. If fine particles cannot be removed
with the water stream, use a mild detergent and a non-
abrasive brush to remove them.
3. Check the compressor oil level sight glass. The oil
should always be clear and watery. Any milky or “slow
rolling” effect indicates that liquid refrigerant is
making its way back into the compressor and will cause
premature compressor failure.
4. When the compressor is not operating, the oil level
should be at least at the bottom of the sight glass, up
to two-thirds full. When the compressor is operating,
the oil level will normally be at the bottom of the sight
glass, or even below, but it must be visible.
5. Low oil sight glass conditions could signify a short
cycling, an oil leak, or an undercharged chiller that
lacks proper refrigerant velocity to return oil to the
compressor sump. Eventually, dry compressor starts
could occur causing premature compressor failure.
This may indicate that some oil has been lost from a
previous refrigerant leak repair. The compressor data
label indicates the correct oil type and quantity with
which it should be filled.
Note:
A flashlight may be required to see the oil churning
in the sump of the compressor. Adjusting the line of
sight may be necessary to visually inspect the oil in
the compressor sump during operation. At a
minimum, the oil must be seen churning in the
compressor sump. It should be clear.
6. Check the glycol concentration using a refractometer.
7. Check the refrigeration pressures. For R410A
refrigerant, low pressure refrigeration gauge should
read 120 to 160 psi and high pressure refrigeration
gauge should read 300 to 450 psi.
Important:
Extended operation with suction pressures
below 80 psi is a clear sign of insufficient
refrigerant charge, refrigeration
obstruction, or valve closed. This can cause
extensive damage to a compressor.
8. Check the refrigeration liquid line sight glass for
persistent bubbles (“flashing”).
Note:
Bubbles in the sight glass do not necessarily
indicate loss or lack of refrigerant charge. Bubbles
(commonly know as “flashing”) will occur
whenever the condenser fans cycle until the
expansion valve settles out the refrigerant flow.
Occasional bubbles also form when the condenser
head pressure control valve bypasses hot gas
around the condenser coil in low ambient
operation. If the refrigeration pressures are in the
normal range, the unit is most likely adequately
charged. “Flashing” could also indicate excessive
superheat adjustment of the thermal expansion
valve.
NOTICE
Equipment Damage!
Failure to remove moisture from system could cause
corrosion within the chiller/heater components, and
degrade performance.
NOTICE
Compressor Failure!
Failure to follow instructions below could result in
catastrophic compressor failure. Do not operate with
insufficient oil.
NOTICE
Compressor Failure!
Failure to follow instructions below could result in
catastrophic compressor failure. Do not operate with
insufficient oil.
NOTICE
Compressor Damage!
Failure to following instructions below could result in
extensive compressor damage.
Verify that suction pressure is sufficient. Secure the
circuit or module offline until status can be examined in
detail.