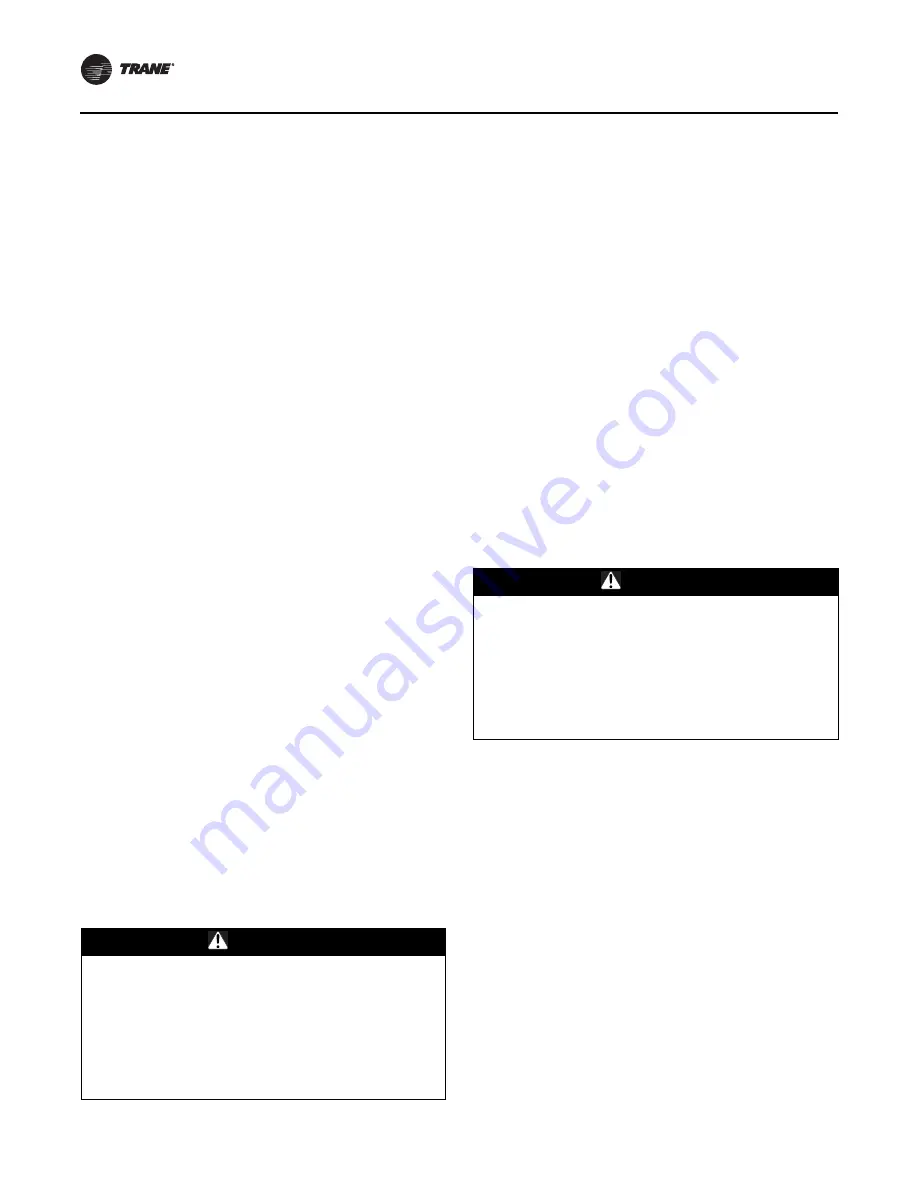
Maintenance Procedures
54
ARTC-SVX002A-EN
6. Clean the strainer inside and out using a soft natural
bristle brush and tap water.
7. Clean the interior of the end cap (or service cap), and
the gasket using a soft natural bristle brush and tap
water. Apply a light coating of lubrication to the gasket.
8. Re-install the strainer in the housing (large end first).
Replace the gasket and end cap and tighten coupling
collar securely.
9. Ensure the water/glycol make-up system is operational
to replenish the water/glycol mixture lost during the
cleaning process.
10. Energize power to the module containing the strainer
by turning power ON at the breaker and/or disconnect.
Evaporator Cleaning Procedure
Fouling of evaporators will result in a gradual decline in
performance of the chiller.
1. Isolate each evaporator using the isolation valves.
2. Back flush using the city water supply forced to a drain.
3. A brazed-plate evaporator is cleaned by back washing
which is forcing a cleansing water/glycol mixture
backwards through it at higher than normal pressures.
4. Flushing should take place across a maximum 30 Mesh
screen filter/strainer with frequent screen cleaning to
remove the debris from the chiller. Flushing should
continue until the screen is clean. After detergent and
chemical cleaning, flush the piping for a minimum of
one hour with fresh water to remove any remaining
cleaning compounds.
Compressor Tasks
The Manhattan™ Gen II Chiller has been designed for ease
of maintenance access. When properly positioned within
a machine room or space, Copeland compressors can be
quickly removed for repair or replacement. (See the
Installation section of this manual for more information.)
Remove Compressor
Verify that power is turned OFF via the chiller module
breaker that is found in the power distribution panel.
Confirm module power is OFF by testing with known
operational voltmeter. Once confirmed, install lockout/
tagout equipment to ensure power is not turned on while
service work is being performed.
1. Close the suction and discharge rotalock valves. Firmly
front-seat both rotalock valves clockwise.
Note:
Do not over-tighten as the valve can become
difficult to loosen if over-tightened.
2. Recover the remaining refrigerant charge from the
compressor using a suitable recovery machine and a
clean recovery cylinder that is pressure rated for the
refrigerant being removed. Weigh refrigerant charge
that was removed.
3. Remove all compressor electrical wiring, as well as
safety and crankcase heater wiring. Make sure to
notate all connection points for the new installation.
Note:
Be sure to document conductor/wire numbers
and their corresponding termination points.
4. Using a spud wrench, remove the rotalock nuts from
the compressor.
5. Remove the four compressor mounting bolts from
frame using two 1/2 inch sockets, or a socket and a
wrench. (Install the nuts underneath the frame.)
6. Remove the compressor from the module.
Install Compressor
Verify that power is disconnected from the chiller.
1. Position the compressor into the chiller and align the
mounting holes. Apply anti-seize compound to the
four mounting bolts, washers, and nuts before
installation. Tighten nuts securely with 1/2 inch socket
and wrench.
2. Remove Schrader valve fittings from old compressor
and install them on new compressor with appropriate
thread sealant.
3. Install the rotalock nuts on the compressor suction and
discharge connections. Tighten with a spud wrench.
4. Charge compressor with 150 psi dry nitrogen and
conduct a bubble and electronic leak check.
5. Evacuate new compressor using the suction and
discharge Schrader valves. Monitor and ensure that at
least a 500 micron or lower vacuum is achieved (250 to
500 micron range would be ideal.)
6. Weigh in amount of refrigerant charge that was
removed.
WARNING
Hazardous Voltage!
Failure to disconnect power before servicing could
result in death or serious injury.
Disconnect all electric power, including remote
disconnects before servicing. Follow proper lockout/
tagout procedures to ensure the power can not be
inadvertently energized. Verify that no power is present
with a voltmeter.
WARNING
Hazardous Voltage!
Failure to disconnect power before servicing could
result in death or serious injury.
Disconnect all electric power, including remote
disconnects before servicing. Follow proper lockout/
tagout procedures to ensure the power can not be
inadvertently energized. Verify that no power is present
with a voltmeter.