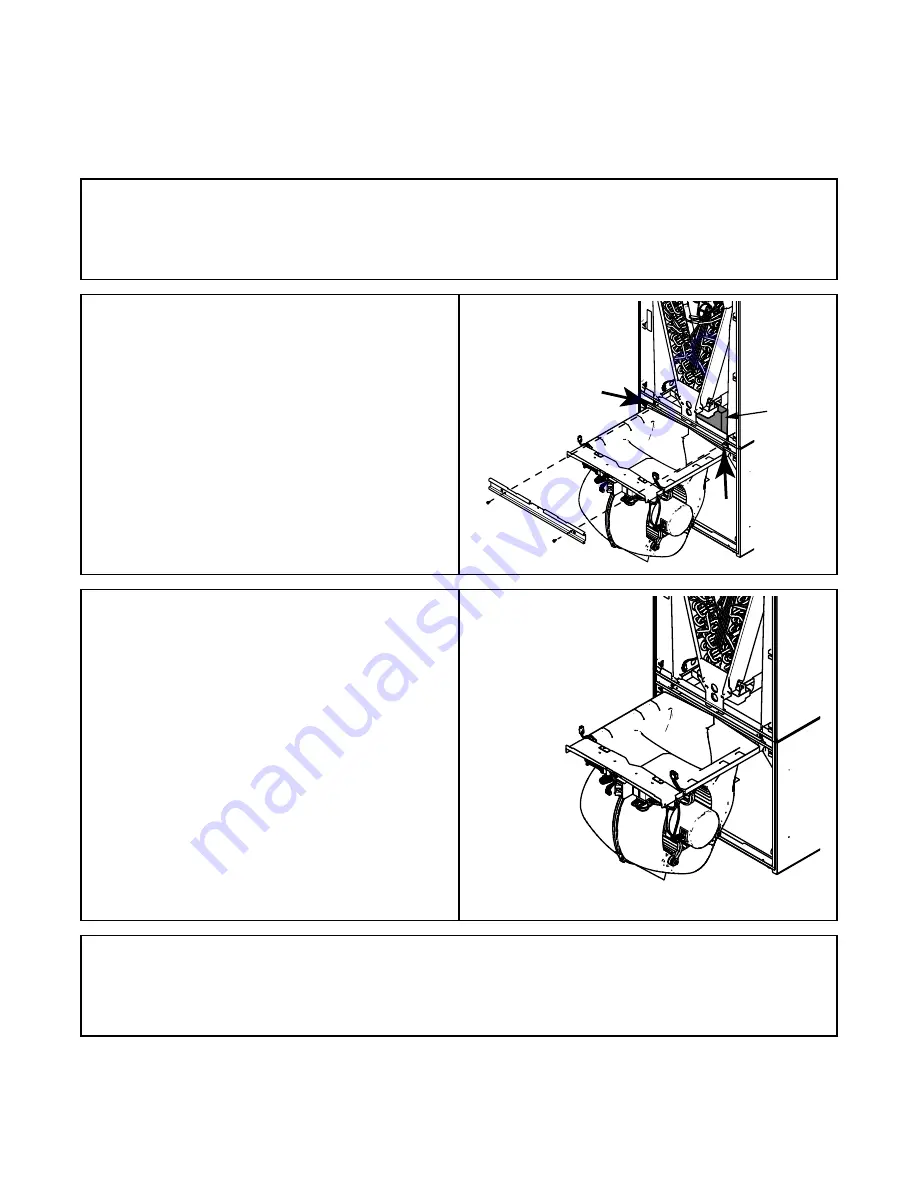
18-GJ89D1-1D-EN
9
Optional Cabinet Disassembly
Note:
If the unit must be transported in a horizontal position, it must be
laid on its back (marked “REAR” on carton).
Note:
To reassemble cabinet, follow the steps in reverse order. Ensure
electrical connections are secure and the plug clips are engaged.
1.
Remove all four front panels.
2.
Remove the two screws on the seal bar and pull the seal bar
straight out.
3.
Disconnect all wiring connections routed to the blower assembly.
a.
Disconnect the air pressure hose.
Note:
Remove the cardboard from the bottom of the blower. Cut the
tie wrap and remove the foam block located at the motor.
Note:
Remove ANA Foam from under the upflow drainpan.
ANA Foam
4.
Slide Blower assembly out of unit using built-in blower support
channels and set aside.
5.
Disconnect wires to the EEV motor and sensors. Cut the wire ties on
those wire harnesses if necessary and replace after re-installing.
Note:
If cut, wire ties that held the sensor must be replaced after the coil is
placed back into the cabinet.