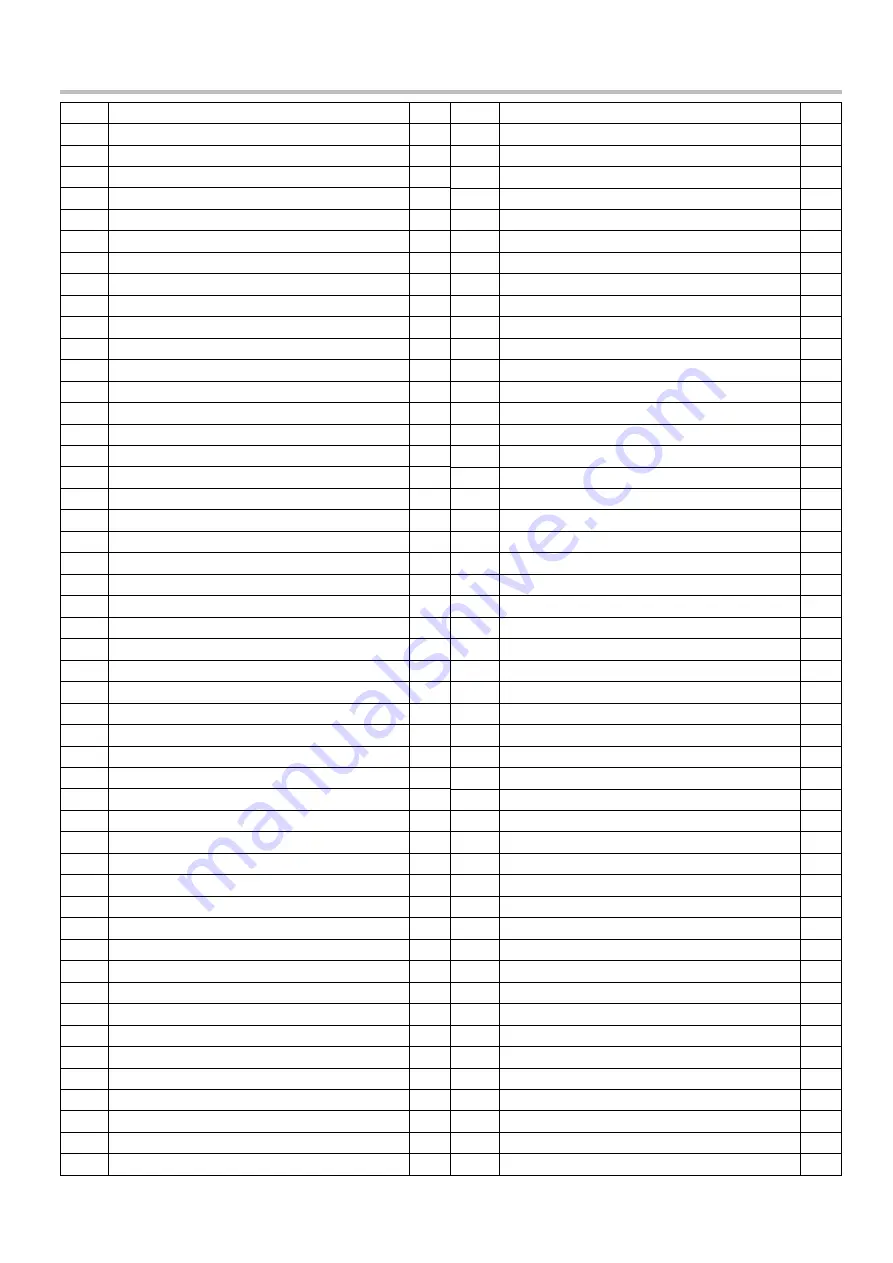
17
Parts List
(4 Speed Models)
NO.
Parts Name
Q'TY
1
POWER SUPPLY CABLE
1
2
PRCD INTERRUPTER PROTECTION (220V)
1
3
CORD ARMOR
1
4
EXTERNAL STAR WASHER (M4)
1
5
PANHEAD MACHINE SCREW (M4x10xP0.7)
1
6~7 N/A
-
8
SWITCH (110V/220V
1
9
SWITCH BOOT
1
10
PANHEAD TAPPING SCREW (M4x25)
4
11
COVER (110V/220V
1
12
PANHEAD MACHINE SCREW (M4x12xP0.7)
6
13
ELECTRONICS UNIT (110V/220V)
1
14
SOCKET CAP SCREW (M5x25xP0.8)
6
15
FLAT WASHER (Ø5xØ12x1)
2
16
TOP HANDLE
1
17
MOTOR END CASTING
1
18
BRUSH SPRING (0.4x4x3T)
2
19
NYLOCK NUT (M5xP0.8)
2
20
PANHEAD MACHINE SCREW (M4x6xP0.7)
2
21
CARBON BRUSH 7x17x19 /110V, 7x17x20/220V
2
22
BRUSH HOLDER PLATE ASSY.
1
23
MOTOR HOUSING
1
24
SOCKET CAP SCREW (M6x75xP1.0)
4
25
MOTOR INSULATION SLEEVE
1
26
STATOR (110V/220V-100x54.1x75)
1
27
PANHEAD MACHINE SCREW (M5x110xP0.8)
2
28
FAN SHROUD
1
29
BALL BEARING (6200)
1
30
ARMATURE (110V-220V-100x54.1x75)
1
31
BALL BEARING (6202)
1
32
OIL SEAL (Ø14xØ25x7)
1
33
GEAR PLATE
1
34
GASKET
1
35
NEEDLE BEARING (HK 0810)
1
36
CLUTCH NUT (M12xP1.75x9T)
1
37
N/A
-
38
PRESSURE DISC (Ø34.8xØ16x2.5)
2
39~40 N/A
-
41
INPUT GEAR (M1.25x44T)
1
42
BUSHING (Ø15.9xØ22x4.7)
1
43
INPUT SHAFT (M1.75x13TxM1.5x12T)
1
44
BALL BEARING (6200)
2
45
NEEDLE BEARING (HK 1010)
1
46
INTERNAL CIRCLIP (IS18)
2
47
SLIDER GEAR-CD (M1.75x36T)
1
48
LAY GEAR (M1.5x46T)
1
49
COUNTERSHAFT GEAR (M2.0x26T)
1
50
PARALLEL KEY (5x5x25)
1
51
PARALLEL KEY (6x6x15)
1
NO.
Parts Name
Q'TY
52~53 N/A
-
54
NEEDLE BEARING (TA1815)
1
55
INTERNAL CIRCLIP (IS25)
2
56
SLIDER GEAR-AB (M2.0x28T)
1
57
OUTPUT GEAR (M2.0x40T)
1
58
CLUTCH NUT (M27xP1.0x7.8T)
1
59
THRUST BEARING (N AS3047)
1
60
N/A
-
61
GEAR HOUSING
1
62
SOCKET CAP SCREW (M5x12xP0.8)
2
63~66 N/A
-
67
O-RING (Ø20x3)
2
68
N/A
-
69
NEEDLE BEARING (TA3020)
1
70
THRUST BEARING (51106)
1
71
OIL SEAL (Ø40xØ50x7)
1
72
WATER FEED COLLAR
1
73
WATER FEED CONNECTOR KIT (1/2")
1
74
WATER COUPLING
1
75
SOCKET CAP SCREW (M5x40xP0.8)
3
76
OIL SEAL (Ø40xØ52x7)
2
77
N/A
-
78
DOWEL PIN (Ø4x11.8)
2
79
ANTI-SEIZE CUP
1
80
O-RING (Ø32x1.5)
2
81
THRUST RING (3252)
1
82
ANTI-SEIZE RING
1
83
O-RING (Ø49x1.5)
1
84~87 N/A
-
88
TERMINAL CONNECTOR BLOCK (PA-12-H)
4/12
89~93 N/A
-
94
CLUTCH DISC SET
1
95
GASKET
1
96
SWITCH BOOT
1
97
GEAR SELECTOR
2
98
SPRING (Ø0.6xØ3.8xØ5x11Tx35L)
2
99
RELEASE PIN
2
100
COUNTERSHAFT SET
1
101
N/A
-
102
BULLS-EYE LEVEL
1
103
SELECTOR DISC
1
104
SELECTOR DISC
1
105
SPINDLE SET (1 1/4"-7 x 1/2"BSP-300.5MM)
1
106
STAINLESS BUSHING
1
107
LED OVERLOAD LAMP (110V&220V)
1
108
LAMP COVER
1
109
SWITCH WIRES
2
GEAR OIL (625cc)
1
A1
EXTENSION SPACER
1