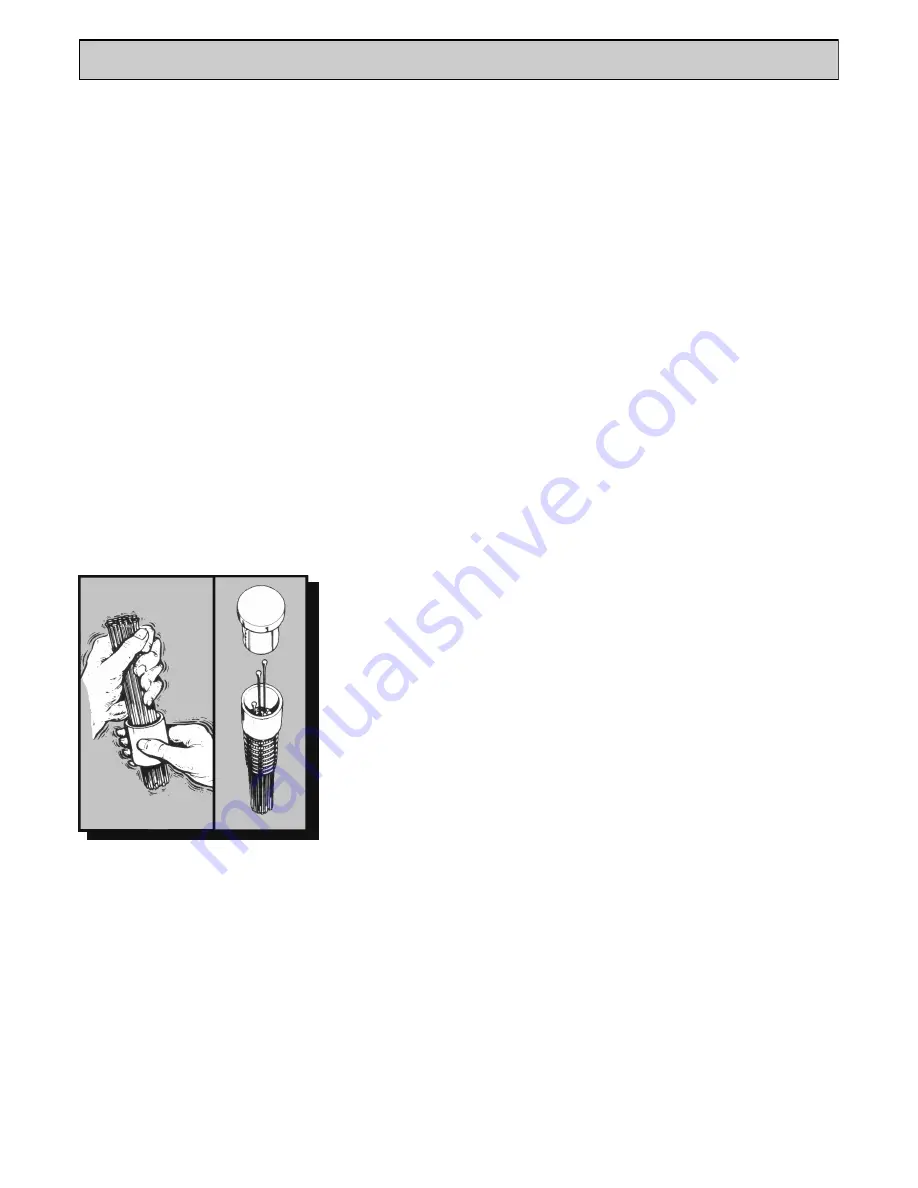
MAINTENANCE
Chisels
Various sizes and types of Chisel are
available.
See parts list for details.
Fitting of Chisel Holder
Before fitting the Chisel Holder (31),
disconnect the tool from the air supply.
To fit the Chisel Holder (31) ensure that the
pinch bolt (30) on the Chisel Holder is loose,
screw the Chisel Holder fully on to the
Cylinder (10).
Turn the knurled collar on the Chisel Holder
(31) until the retaining ball is fully visible.
Insert the Chisel (32) into the Chisel Holder
(31) and select the nearest position to align
the blade with the Throttle Lever (7).
Turn the collar half a turn to lock the Chisel
(32) in place.
If the Chisel (32) does not line up, it may
require the Chisel Holder (31) to be
unscrewed slightly.
Tighten the pinch bolt (30) using a 6mm AF
Allen key. To release the Chisel (32), rotate
the knurled collar until the retaining ball is fully
visible and remove the Chisel (32).
Needle Holder Attachment
Before fitting the Needle Scaler Attachment,
disconnect the air supply to the tool.
Assemble the component parts of the Needle
Scaler attachment in the following order;
insert the Needles (26) into the Needle Holder
(25), place the Spring (27) over the Needles,
Pointed tip needles
Sharpened to a nail point, these are most
effective in breaking through very hard scale
on surfaces where some surface indentation
is permissible - or where keying (i.e. profile) of
the surface is desirable.
Pointed tip needles are available in 3mm and
4mm only.
Chisel tip needles
These are general purpose needles, flattened
to a chisel like blade and are most effective in
the removal of thicker material, while leaving a
less pitted surface than the Pointed tip
needles but still giving some surface
indentation (i.e. profile).
Chisel tip needles are available in 3mm only.
Flat tip needles
Machined to a flat tip, these needles will leave
slight marking (i.e. profile) on the surface; the
2mm needles can have a burnishing effect.
2mm Needles are recommended for use on
thin gauge metals and any surface where light
treatment is desired.
Flat tip needles are available in three sizes -
2mm, 3mm and 4mm.
Maintenance
Only a competent person, in a suitably
equipped workshop, must carry out
maintenance.
Disconnect the tool from the air supply
before carrying out any maintenance or
any of the operations in the next sections.
Clean all debris from the exterior of the tool.
Cleaning
At intervals of no more than 40 hours or if
operation becomes unproductive and the
Piston shows signs of sticking, dismantle and
clean with a highly refined paraffin.
Replace worn components as necessary.
Immediately after cleaning, thoroughly oil the
tool with one of the recommended lubricants.
Piston and Cylinder Removal
Remove the Chisel Holder (31) or Needle
Attachment as previously described. Clamp
the Cylinder (10) firmly in a vice using the flats
provided. Using a suitable wrench and the
spanner flats provided, unscrew the Cover
(14) from the Cylinder (10). This may initially
need some extra effort to break the bond.
With the Cylinder (10) free of the Cover, push
the Piston (9) out of the Cylinder (10).
Remove the Cylinder (10) from the vice and
inspect all parts for wear, particularly the
Piston (9) and the Cylinder’s bores. Remove
the two O’ Rings (11)(12) from the Cylinder
(10).
Valve Body Servicing
Clamp the Valve Body Assembly firmly in a
vice at the Valve Body (6) using the flats
provided, with the Throttle Lever (7)
uppermost. Using a 3mm diameter pin punch
and small hammer, remove the Throttle Lever
Roll Pin (8), and remove the Throttle Lever
(7). Rotate the Valve Body (6) 180 degrees in
the vice to gain access the Valve Cap (1).
Unscrew the Valve Cap (1) using a
screwdriver, check the Valve Cap 'O' Ring (2)
for signs of deterioration, remove the Spring
(3), push out the Valve Stem (4) and remove
the valve seat 'O' Ring (5). Check the Valve
Stem (4) and 'O' Ring (5) for wear.
Assembly
Before any assembly takes place, ensure all
parts are clean and are coated in a thin film of
recommended air tool lubricant.
It is strongly recommended that all the
O’Rings and any other worn parts be replaced
using only genuine Trelawny spares.
Valve Body Assembly
Clamp the Valve Body firmly in a vice, using
the flats provided, and with the threaded hole
uppermost.
Insert the valve seat 'O' Ring (5) into Valve
Body (6), followed by the Valve Stem (4),
Spring (3), then the Valve Cap (1) complete
with its 'O' Ring (2), tighten the Valve Cap (1)
with a screwdriver.
Rotate assembly 180 degrees in the vice.
Using a 3mm diameter pin punch locate and
align the Throttle Lever (7) in position, then
drive in the Throttle Lever Roll Pin (8) into the
pin location.
Piston and Cylinder Assembly
Fit new O’Rings (11)(12) to the Cylinder (10),
Lubricate the Piston (9) and Cylinder bore,
insert the Piston (9) into the Cylinder bore.
Ensure that the threads on the Cylinder (10)
and in the Cover are clean and dry.
Clamp the Cylinder (10) in a vice using the
flats provided.
Then using a suitable wrench on the spanner
flats provided, tighten the Cover onto the
Cylinder (10) and torque to 135Nm (100lbs/ft).
Refit the Chisel Holder/Needle Scaling
Attachment as described previously.
Recommended
Lubricants
Oil the tool daily before use. Put a few drops
of one of the following zinc free air tool
lubricants through the air inlet.
SHELL
S22 or R10
CASTROL
Hyspin ZZ32
Disposal
When the tool and its accessories are taken
out of service for disposal, it is recommended
that: -
They are rendered unusable to prevent
improper re-use.
They are dismantled into component form,
segregated according to material composition
and disposed of using waste recycling
processes specified by local regulations.
Machinery Directive
Information
This tool has been designed and produced in
accordance with the following directive:
2006/42/EC
Machinery Directive
and applicable harmonised standard:
EN ISO 1 1148-4:2010
insert the Anvil (24) into the Needle Holder
(25), then place the assembly into the
Intermediate Tube (28). Check the service
layout for clarification. Screw the assembly
fully onto the Cylinder (10) and tighten the
pinch bolt (30) using a 6mm AF Allen key.
Slide the Front Tube (29) on to the
Intermediate Tube (28) until approximately
25mm (1”) of Needle protrudes from the Front
Tube (29). Tighten the pinch bolt (30) using a
6mm AF Allen key.
As the Needles wear, adjust the Front Tube
by loosening the Allen Screw and adjusting
the Front Tube so that approximately
1” (25mm) of Needle protrudes from the Front
Tube (29) and then retighten the Allen Screw.
The correct
position of parts
when changing
needles
Hold the needles loosely
and shake the holder,
needles will fall into location
holes
Summary of Contents for LR2
Page 1: ...Long Reach Scalers Operation and Maintenance Manual www trelawnyspt co uk ...
Page 2: ......
Page 3: ......
Page 6: ...SERVICE LAYOUT Standard Scaler ...
Page 7: ...SERVICE LAYOUT Lite Scaler ...
Page 10: ...NOTES ...
Page 11: ...NOTES ...