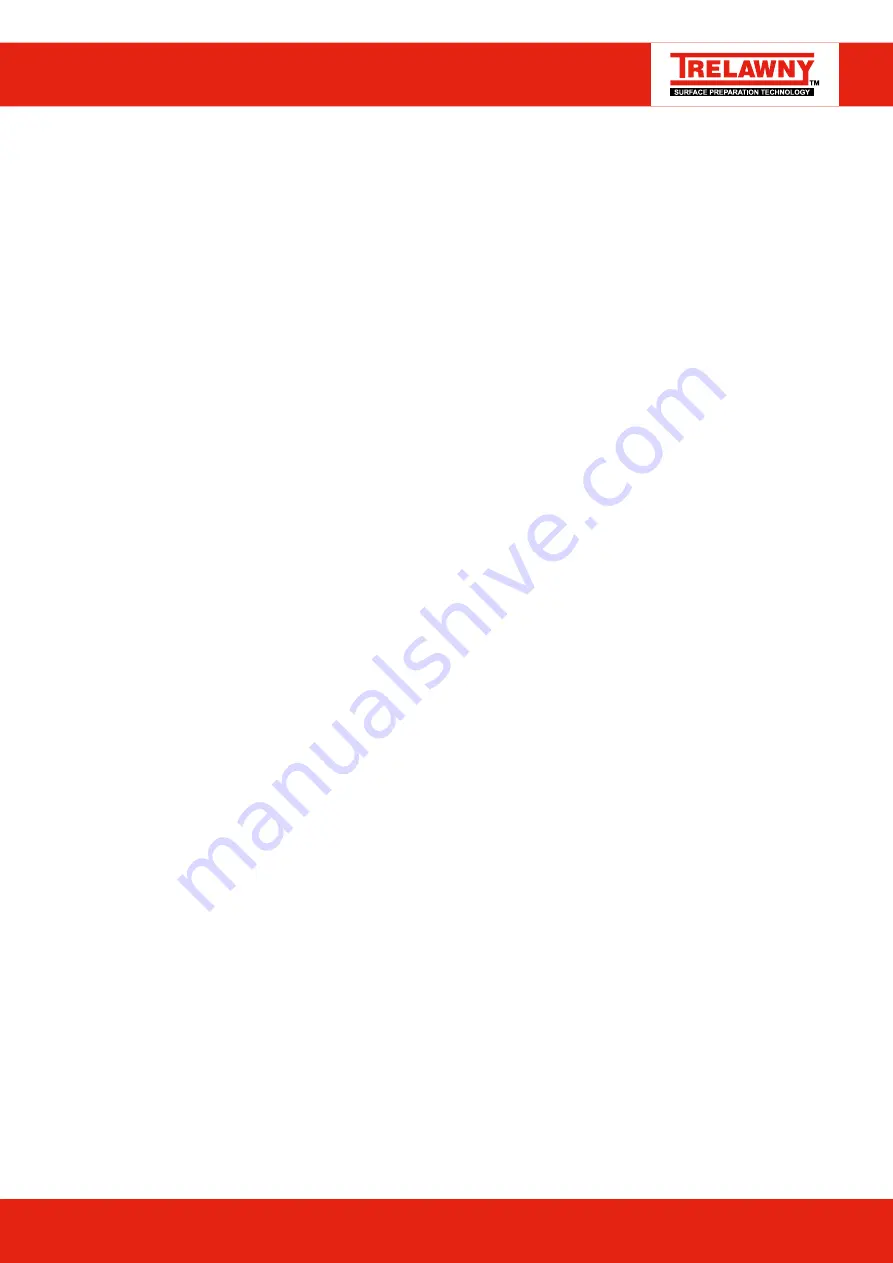
www.trelawny.co.uk
maintenance
Grinding Block Replacement
Switch off the engine-powered versions and allow the
engine to cool completely, disconnect electric-motor-
powered versions from its power supply
. Place the machine
on a flat and level surface. Raise the front skirt by loosening
the four 10mm guard retaining bolts on either side of the
machine and slide the guard up to the top of the slots, tighten
the bolts temporarily.
Electric Machines
Tilt the machine backwards to rest on its handle bar.
Place a heavy object (10kg sand bag, etc.) across the upper
part of the handle bar or tie down for additional security.
Take note how the grinding blocks and wedges have been
assembled, using a suitable wooden drift, knock out the
grinding block, not the wooden wedge. Dispose of the used
grinding blocks according to local legislation.
Fit each new grinding block squarely into the grinding plate
location corner at the outer flat face of the grinding disc.
Secure with a new wooden wedge, between the block and
the inner face of the grinding block, knock the wedge into
position using a suitable drift.
Note:
Do not use a mix of old and new grinding blocks, this will
cause rapid wear of the new blocks and could cause the
machine to become uncontrollable, unstable and dangerous
in use. Re-adjust the lower guard and tighten the bolts.
Petrol/Gasoline Machines
Switch off the engine-powered versions and allow the engine
to cool completely, disconnect electric-motor-powered
versions from its power supply.
Place the machine on a flat and level surface.
Raise the front skirt by loosening the four 10mm guard
retaining bolts on either side of the machine and slide the
guard up to the top of the slots, tighten the bolts temporarily.
It is not recommended that petrol/gasoline-powered
machines are tilted back such that they rest on their handles.
This may cause leakage of fuel and is therefore a hazardous
operation.
Remove the four countersunk M12 screws from the disc,
ensuring that the disc is supported as the last two are
removed. The disc now will come away from the drive plate.
Dispose of the used item according to local legislation.
Offer the new disc up to the drive plate and align the holes.
Loosely fit the four bolts and then tighten in a diagonal
sequence to 40lb/ft. Re-adjust the lower guard and tighten
the bolts
Brush Seal Replacement
The machine is fitted with a flexible brush seal which will
need replacement from time to time to maintain the efficiency
of the dust control system. Follow the first five steps from the
above procedure for changing discs. Drill out rivets and to
remove the brush simply grasp one end and pull, the brush
will come off the guard. To fit the new brush, align one end of
the brush with the end of the guard and use a suitable drift to
knock the brush onto the metal guard, working along until it
is securely fitted.
operating range
Summary of Contents for TCG 250
Page 1: ...www trelawny co uk www trelawny co uk OPERATION AND MAINTENANCE MANUAL ...
Page 17: ...www trelawny co uk EXPLODED DIAGRAM EXPLODED VIEW ...
Page 23: ...www trelawny co uk wiring diagrams ...
Page 25: ...www trelawny co uk notes ...
Page 26: ...PAGE 26 TCG250 Floor Grinder notes ...
Page 27: ...www trelawny co uk notes ...