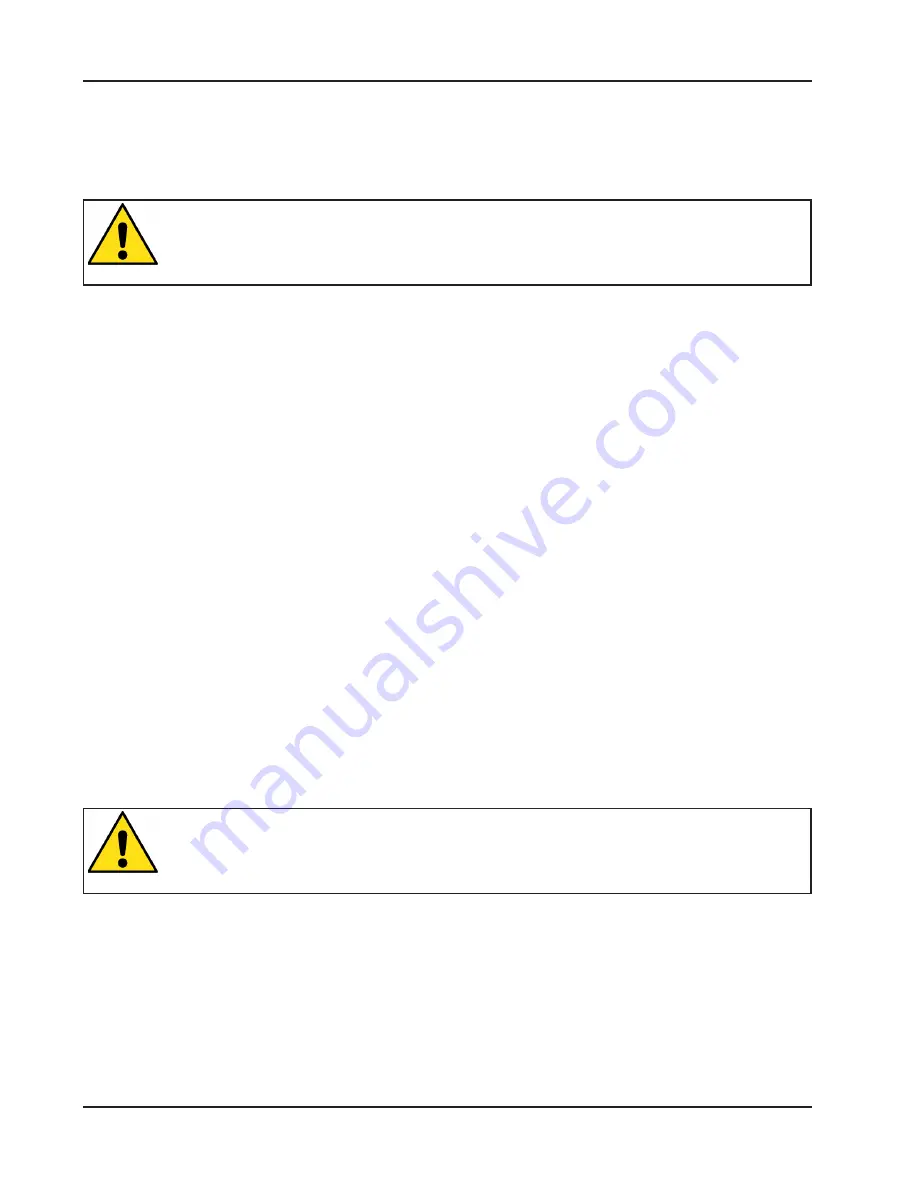
TRI TOOL INC.
92-1942 Orig. 210625
14
6. OPERATION
• Select a tool bit according to the tubing material, tubing size, and how critical it is
to have a near burr free end.
• A standard entrance angle tool bit is recommended for carbon steel. These tool
bits also work well with some stainless steel applications where a near burr free
end is not a critical requirement.
• A high entrance angle tool bit is recommended for most stainless steels. Generally,
this is the most suitable edge geometry for about 90% of all the stainless steel
tubing applications.
• An extra hook angle tool bit is recommended for stainless steels that are very
soft. These stainless steels include materials like 316L, which have been bright
hydrogen annealed, vacuum annealed or annealed and Electro-polished. Electro-
polished stainless steel has a micro-thin surface, which is high in Cr and Ni, which
makes it very soft, but tough and difficult to cut without a burr.
• The M-42 tool bits are for use with the exotic alloys where the high heat resistance
is required to avoid burning the cutting edge of the tool bit. M-42 can improve the
life expectancy of the tool bit under some conditions on stainless steel. Since M-42
tool bits are more brittle than the standard M-2 tool bits, there is a much greater
risk of damaging the M-42 tool bit when installing the tubing in the Tube Squaring
Machine. Loss of tool bits from damaged edges may not offset the improved
cutting life that those tool bits may provide. Some exotic alloys may require tool bits
with both the extra hook angle as well as the M-42 tool steel for heat resistance.
CAUTION
CAUTION: The use of dull or improperly designed Tool Bits or Tool Bits not manufactured
by Tri Tool Inc. may result in poor performance and may constitute abuse of this machine
and therefore void the Tri Tool Inc. factory warranty.
GUIDELINES FOR SELECTING A TOOL BIT
CAUTION
CAUTION: Make sure that the Model 300STS is disconnected from the power source
before you install a tool bit.
INSTALL THE TOOL BIT
1.
Insert the Tool Bit into the slot in the Cutting Head, Refer to Fig. 7. Make sure the
cutting edge of the tool bit is facing toward the center of the cutting head. Do not
install the tool bit backwards.
•
The standard tool bit position, shown below in Fig. 7, is used for 1.000” (25.4mm)
and smaller diameter tubing. This is the designed working position of the tool bit
and will leave virtually no burr with standard tubing. When working with Electro-
polished stainless steel tubing, use slow cutting speeds to minimize the ID burr.