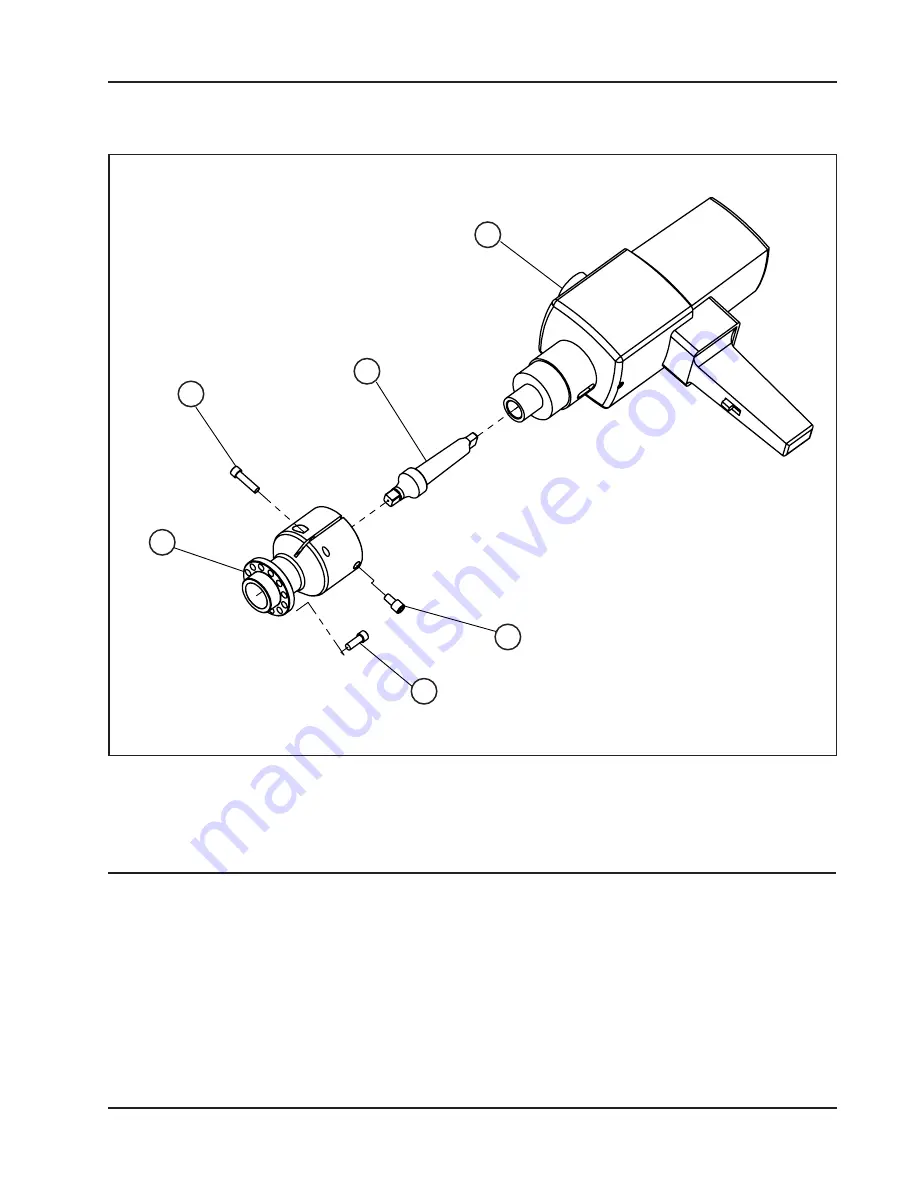
51
Model 208B BEVELMASTER
®
92-1482 Rev. 190410
MOTOR ASSEMBLY, ELECTRIC DRIVE, 230V HD (P/N 58-0174)
3
5
1
4
2
6
Parts List, Motor Assembly, Electric Drive, 230V HD (P/N 58-0174)
Item
No
Part
No.
Description
Qty
1.
27-0826
ADAPTER, DRIVE
1
2.
30-3143
1/2" SQUARE DRIVE
1
3.
33-0055
SCREW, CAP, 5/16-18 7/8" LG.
3
4.
33-0057
SCREW, CAP, 5/16-18 X 1 1/4" LG.
1
5.
33-1874
SCREW, ANTI-ROTATION
2
6.
58-0173
MOTOR, ELECTRIC, 230V, MODIFIED
1