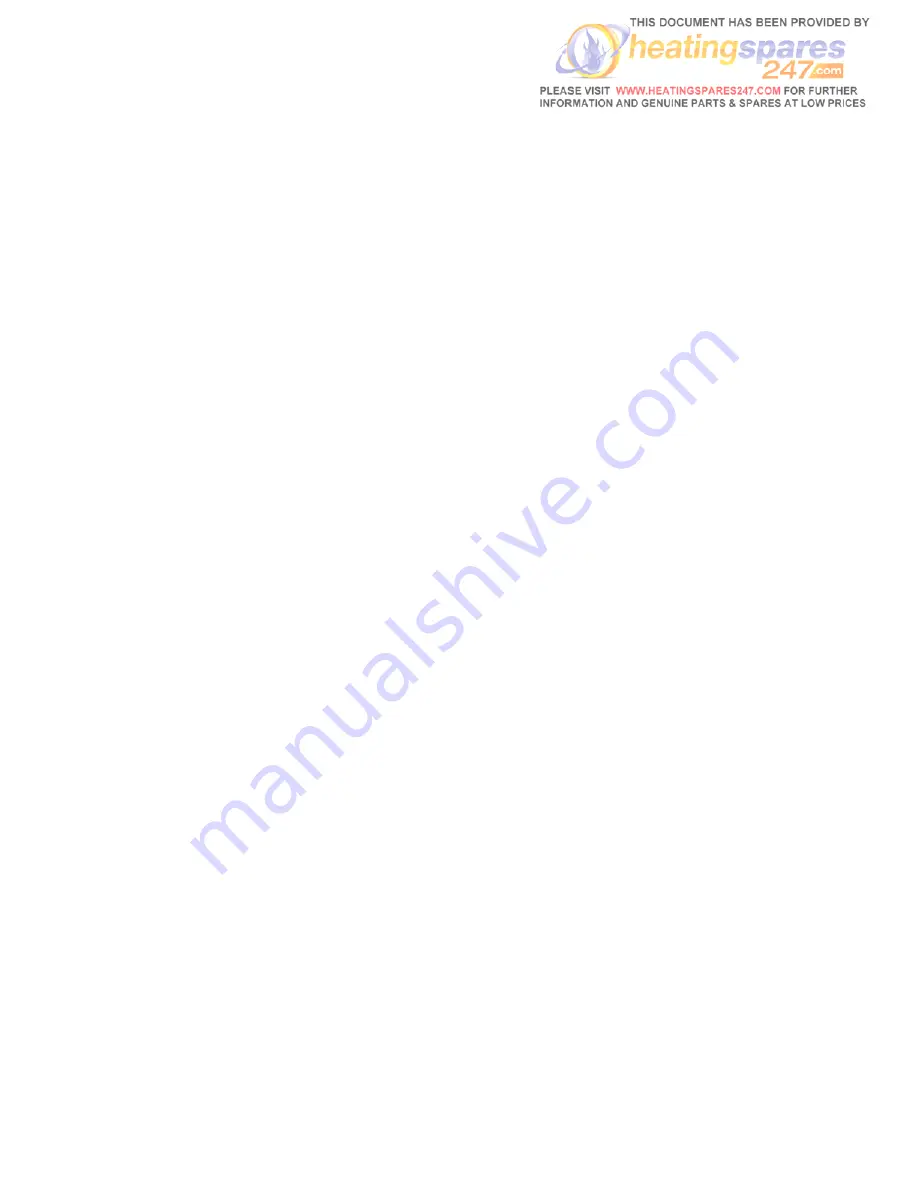
10
Steel Tanks
Steel tanks should comply with the requirements BS 799,
Pt. 5: 1987 and mounted on brick or block piers with a
waterproof membrane between the piers and tank.
The tank should be fitted with fill and vent connections
(weather protected), a drain-off cock, shut-off valve and
an oil level indicator.
Plastic Tanks
Polyethylene tanks are now widely used because of their
advantages over traditional steel tanks:
(a) They do not need pier supports and can be mounted
directly on any flat surface giving uniform support for
the tank base.
(b) They do not corrode and therefore never need
painting.
(c) They are easier to handle because of their lower
weight.
(d) They have a 10 year manufacturer’s guarantee.
Plastic tanks should be fitted with similar components to
those used with steel tanks.
Fire Protection
To comply with building regulation
Section J5:
1
Where a storage tank is close to a dwelling, fire
cladding must be provided to the eaves, if less than
1.8m from the top of the tank.
2
The cladding must extend 300mm beyond the tank.
3
The tank must be sited on a non-combustible base.
Pollution Protection
To comply with building regulation
section J6
, the tank
must be ‘bunded’ (i.e. double walled) if:
1
The tank is less than 10m from a stream.
2
The tank is less than 50m from a well, spring, or drinking
water.
3
The tank cannot be viewed from the delivery point.
4
In the event of a leak, there is a risk of oil reaching a
manhole cover or drain.
5
The tank capacity exceeds 2500 Litres.
Oil supply line
A long life flexible oil hose is supplied with the boiler.
A filter and shut-off valve are also required. These should
be fitted as shown if Figs. 4 and 5.
The oil shut-off valve should be fitted as close to the
burner as practicable to enable the burner to be
disconnected without undue loss of oil. The filter must be
connected in the oil supply pipe and positioned as close
to the oil tank as possible.
Fire Valve
A fire-valve must be fitted in the oil line outside the
building with its sensing phial positioned within the boiler
casing below the control panel. A clip is provided for
retaining the phial.
All oil line joints must be completely sealed and the total
pipe run thoroughly flushed out before connecting to the
burner. No soldered joints are permitted in the oil line.
The oil line can be fed into the back of the boiler base tray
or through the holes at the side.
Single pipe oil supply (Fig. 4 )
When, the bottom of the oil supply tank is above the
burner, a single pipe gravity system can be used. The oil
supply pipe must be connected to the suction port on the
burner pump via the flexible hose.
Two pipe oil supply (Fig. 5)
Where, the bottom of the oil storage tank is below the
burner, a two pipe suction lift system is necessary.
When using a two pipe system, it is important that the
by-pass screw is fitted, on the BFP II pump remove the
end cover and filter, then remove the ‘U’ washer by
unscrewing the bottom screw, then replace the screw
ensuring it is fully inserted. An additional flexible hose is
also required.
A spring loaded non- return valve must be fitted in the
suction line to stop the oil running back to the tank.
A filter, shut-off valve and fire valve must also be fitted in
the line.
No valves are permitted in the return line which must
remain unobstructed at all times.
Notes:
(1) The pump suction should not exceed 0.4 bar, other
wise dissolved gas will be released from the oil to
affect combustion.
(2) The return pipe must end at the same level as the
suction outlet to prevent loss of prime.
(3) The outlet from the tank should be approximately
75mm (3 in) above the bottom to prevent sediment
and water being drawn into the supply pipe.
Oil De-aerator -
Single pipe supply (Fig. 6)
Where a two pipe suction lift system is required, but the
return pipe is too long, or impractical to run, an Oil De-
aerator can be used. The burner is piped as for a two
pipe system up to the Oil De-aerator but only a single
pipe is required to be run back to the oil storage tank. A
none-return valve is not required with this system but the
bypass plug must be fitted in the pump as for a two pipe
system.