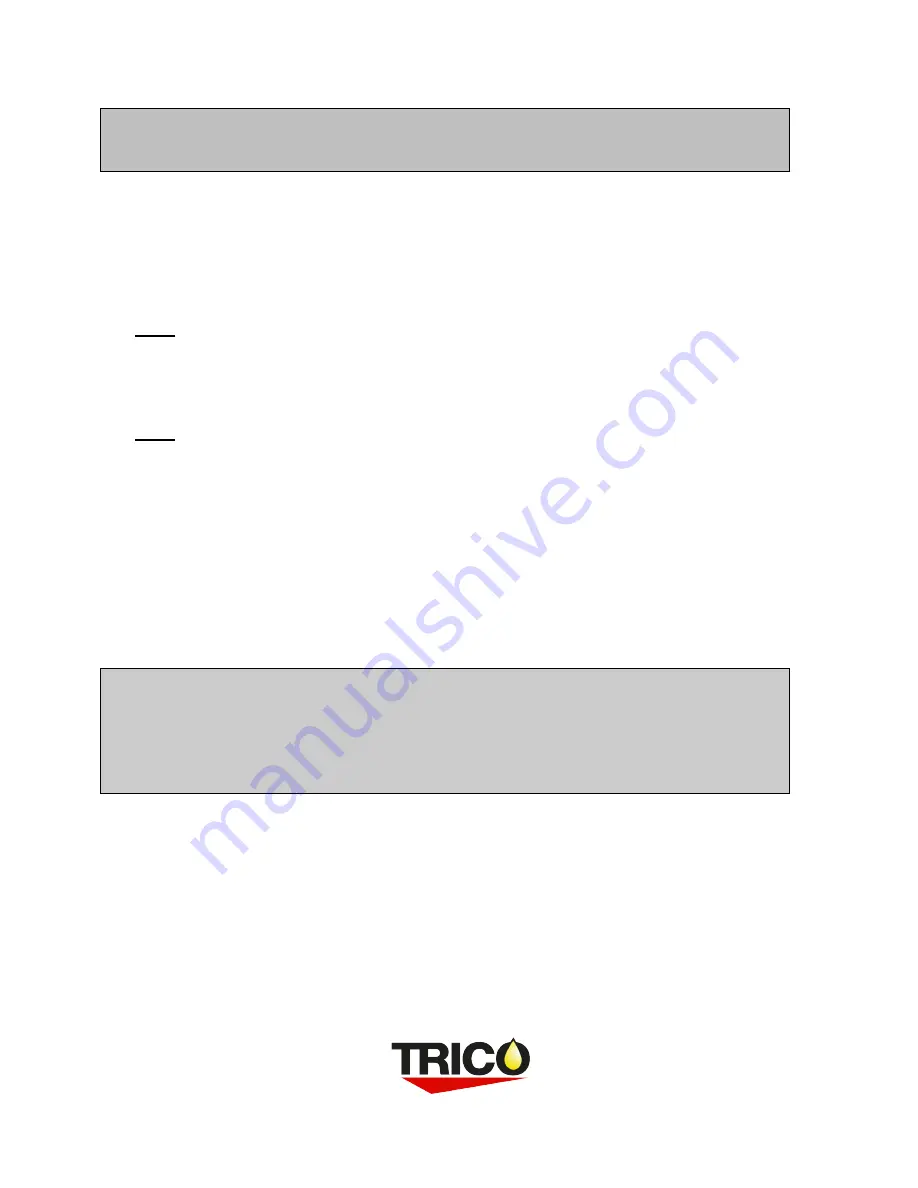
1235 Hickory Street; Pewaukee, WI 53072
For Customer Support: 800-558-7008
WARNING:
The maximum surface temperature of the air motor should not exceed
266ºF/130ºC. Do not continue to operate the motor if the measured surface
temperature exceeds temperature stated.
11. Check air motor intake and exhaust filters after first 500 hours of operation. Clean
filters and determine how frequently filters should be checked during future
operation. This one procedure will help assure the motor’s performance and service
life.
12. Verify that air supply is maintained at 100psi or below by reading the pressure gage
located on the FRL unit. Regulators are preset at 100psi operating pressure. They
are lock and unable to be adjusted.
Note
: tampering with the locked FRL regulator will void product warranty.
13. It is helpful to install an inline ball valve before the connection to the FRL to quickly
turn the air supply to the motor on and off. Different fluid viscosities will apply
different resistance to the pump and motor assembly in turn motor speed will
fluctuate.
Note
: Motor will gradually increase in speed at startup until maximum torque is
applied at operating flow. Motor RPM will increase and decrease with the increase or
decrease of suction and lift head.
14. The condition of the filter elements should be monitored by the pressure gages
located on the filter head or on the gage panel. When the differential pressure
between these gauges equals 40 psi differential the filter element needs to be
changed out. If filter elements are not changed before the specified pressure, the
system pressure will continue to increase until the built-in pressure relief valve
opens. The filter heads go into bypass at 43 psi differential and at this point oil is
bypassing the filter media and is no longer being filtered. The pump has a built-in
pressure relief at 105psi at the inlet, at this point the pump will run in bypass
relieving the built-up pressure.
WARNING:
Failure to monitor the system and change filter elements may cause
filter media to collapse at 80psi differential which may produce further contamination
by inducing filter media into reservoir or container at fluid exit point. Maintain
monitoring of the
High Viscosity Pneumatic Filtration system
while in operation.
Continued running of the pump in pump bypass due to pressure will cause excess
heat generation and/or cavitation, reducing the life of the filtration unit.
15. Trico
High Viscosity Pneumatic Filtration systems
are equipped with sample ports.
For most accurate results, do not sample into an open bottle. Use a vacuum bottle
sampler with plunger removed.
16. The 3 GPM filter cart (36933) is equipped with a bypass valve and piping. This valve
should be kept in the fully closed position when using the filters. Use the bypass for
removal of old/used oil only.
Turn Handle until it is parallel with the cart frame for
filtration mode. Turn handle until it is fully perpendicular to the cart frame for by-pass
mode.
17. When finished filtering/transferring fluid, turn the air off and disconnect the air supply
connection. Wipe any excess oil from the unit that might have spilled during the
filtering/transferring process.