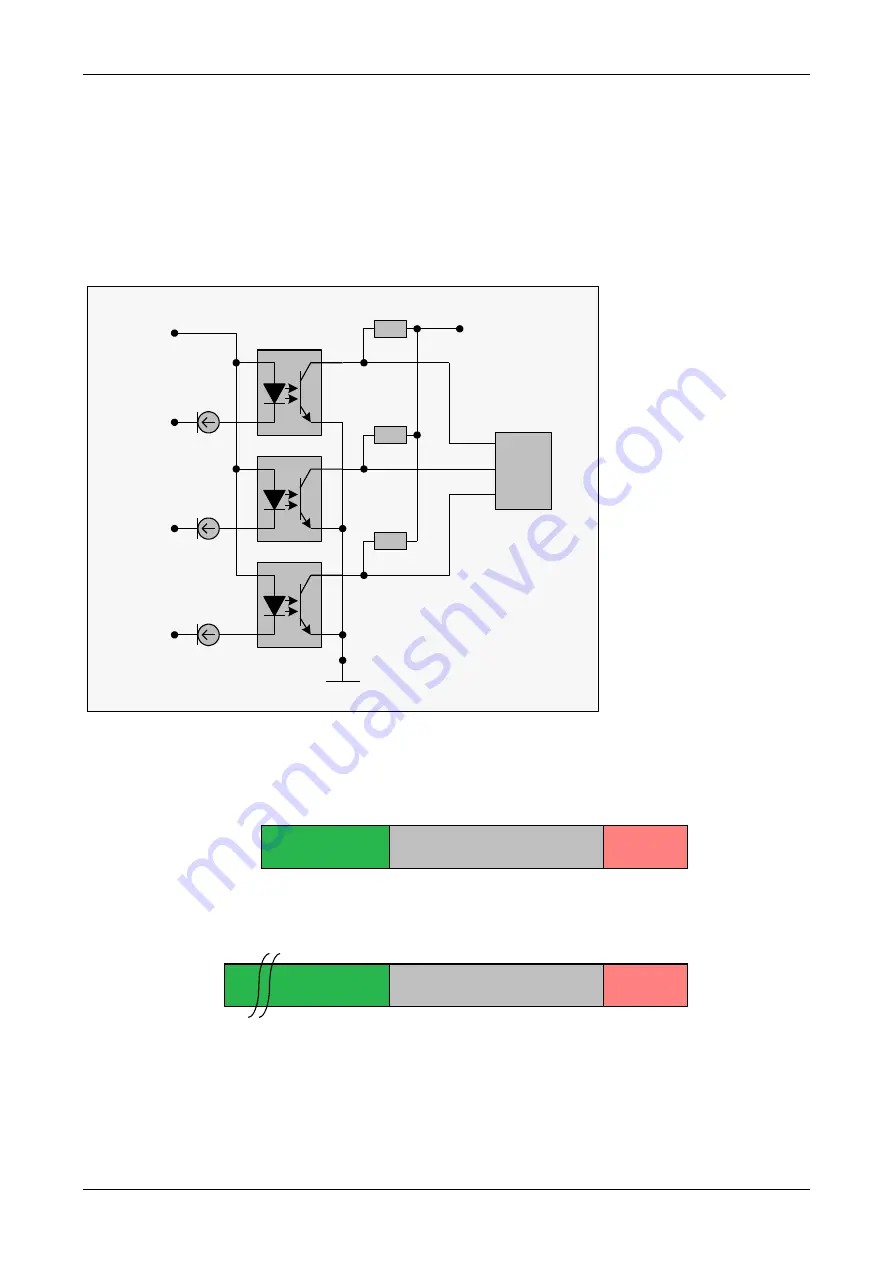
PD-013-42 / TMCM-110-42 Manual (V1.24/2011-NOV-25)
9
Copyright © 2011, TRINAMIC Motion Control GmbH & Co. KG
5.1
Step, direction and disable inputs
The inputs disable, dir and step are electrically isolated from the module. The inputs are related to V
COM
. In a
typical application, U
COM
shall be tied to the positive supply voltage of the master and the inputs are driven
by open collector or push / pull outputs. V
OPTOFF
and V
OPTON
must not exceed VCOM to avoid reverse polavity
for the optocouplers.
OFF: V
COM
- V
IN
< 1.0V
ON:
V
COM
- V
IN
>= 3.5V
U
COM
5..24V
Disable
Dir
Step
C
E
A
C
C
E
A
C
C
E
A
C
GND
µC
A: Anode
C: Cathode
C: Collector
E: Emitter
+5V
Figure 5.1: Step, direction and disable inputs
Examples:
V
OPTOFF
V
OPTON
V
STEP
= 0V
1.5V
4.0V
5V
undefined
20V
19.0V
16.5V
V
OPTON
V
OPTOFF
undefined
V
COM
= 5V
V
COM
= 20V
V
STEP
= 0V