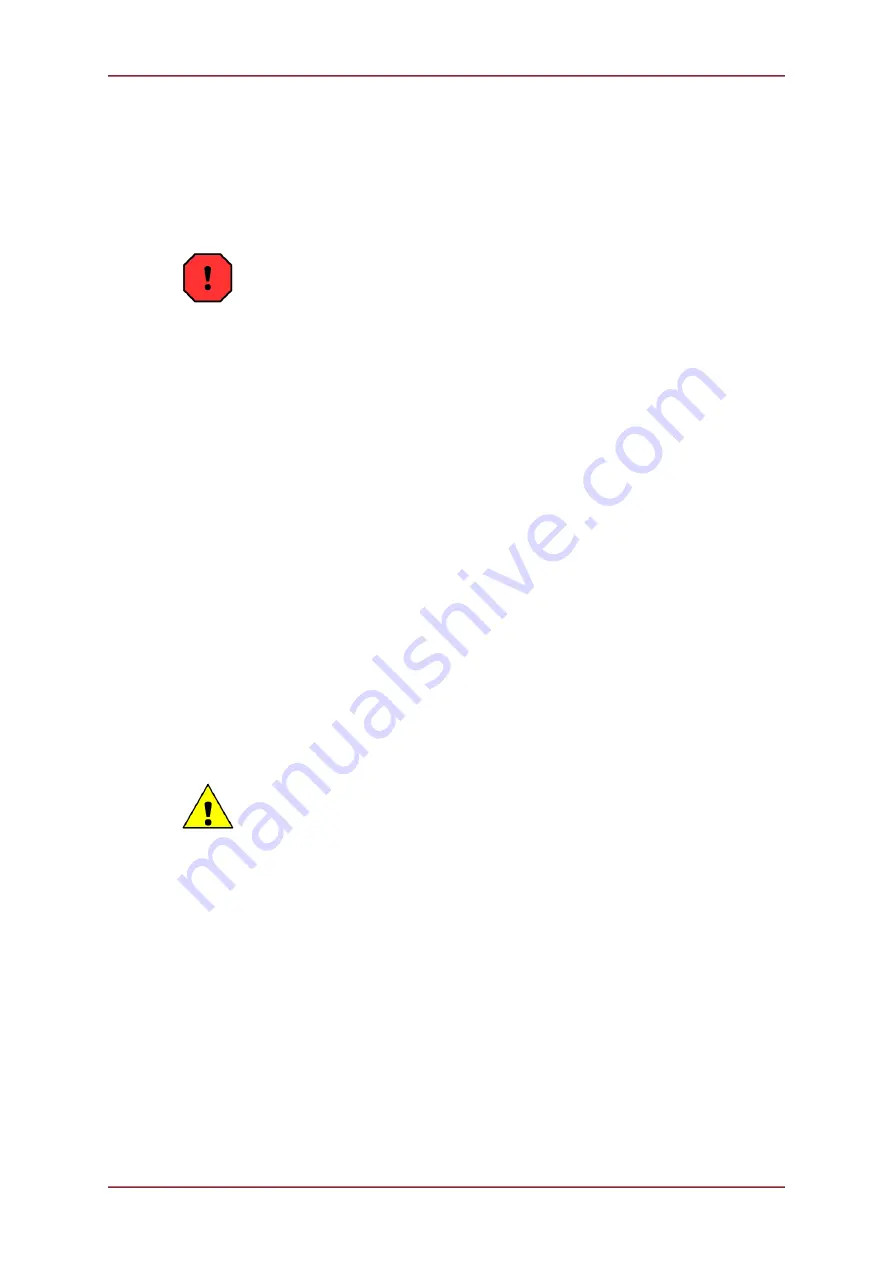
Intelligent Gyro Compass (iGC)
0707-SOM-00004-7
7
© Tritech International Ltd.
1. Safety Notices
1.1. General
Warning
The iGC may contain fluid or gas under pressure and electrical systems at
potentially hazardous voltages.
All installation, operation, maintenance and repair works must be carried out by
competent personnel.
The installation of the iGC and associated components is fully the responsibility
of the user.
The iGC shall be installed, commissioned, operated and maintained in
accordance with this instruction manual, including staying within the maximum
operating conditions given in Appendix A,
Appendix
A - iGC Supply Specification. Failure to do so may lead to safety hazards or
equipment failure.
Before starting installation, commissioning, operation or maintenance of the iGC,
personnel should read and understand all relevant sections of this manual.
Any queries, comments or suggestions regarding the content of this manual or
the safe installation, operation or maintenance of the iGC should be referred to
Tritech.
1.2. Pressure
Caution
If a seal has failed AND then acts as a one-way check during flooding, it is
possible that pressurised fluid and gas has been trapped inside the iGC pressure
vessel. This may be indicated by one or more of the following:
1. The iGC has ceased to function after flooding
2. A water-ingress alarm has been generated
3. If the iGC is shaken fluid can be heard or felt moving around inside the housing
4. During removal, the pressure dome is very tight on its threads
5. During removal of the pressure dome there is fluid leakage at the joint
The pressure housing has been designed so that the main seal will cease
to function whilst there is still sufficient thread engagement to prevent the
components from flying apart. The correct procedure for disassembly is given
in Chapter 8,