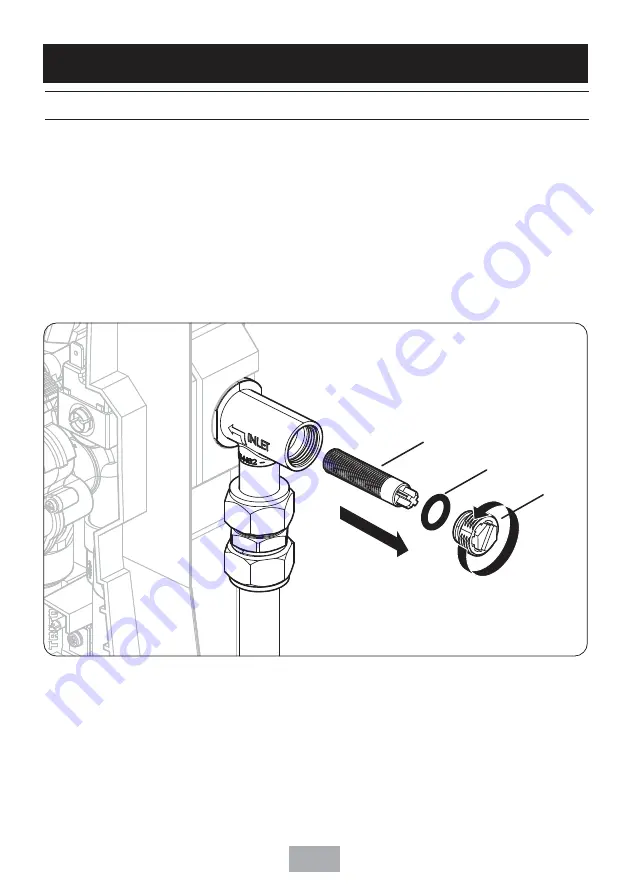
28
Instructions for installers and service engineers only
INSTRUCTIONS FOR INSTALLERS AND SERVICE ENGINEERS ONLY
Instructions for installers and service engineers only
It is recommended that the filter is periodically cleaned in order to maintain the performance of the
shower. It is essential that this operation is carried out by a competent person.
Switch off the electricity and water supply at the mains.
The inlet filter is situated inside the water inlet fitting.
To gain access to the filter remove the cover. Unscrew the inlet filter cap on the water inlet fitting.
Inspect the o-ring for damage when the filter is removed. Do not over tighten the filter cap on
reassembly.
When cleaning the filter,
DO NOT
use a sharp object as it will cause damage. It is preferable to use
an old toothbrush or similar.
Cleaning the Filter
MAINTENANCE
Filter
O Ring
Inlet Filter
Cap