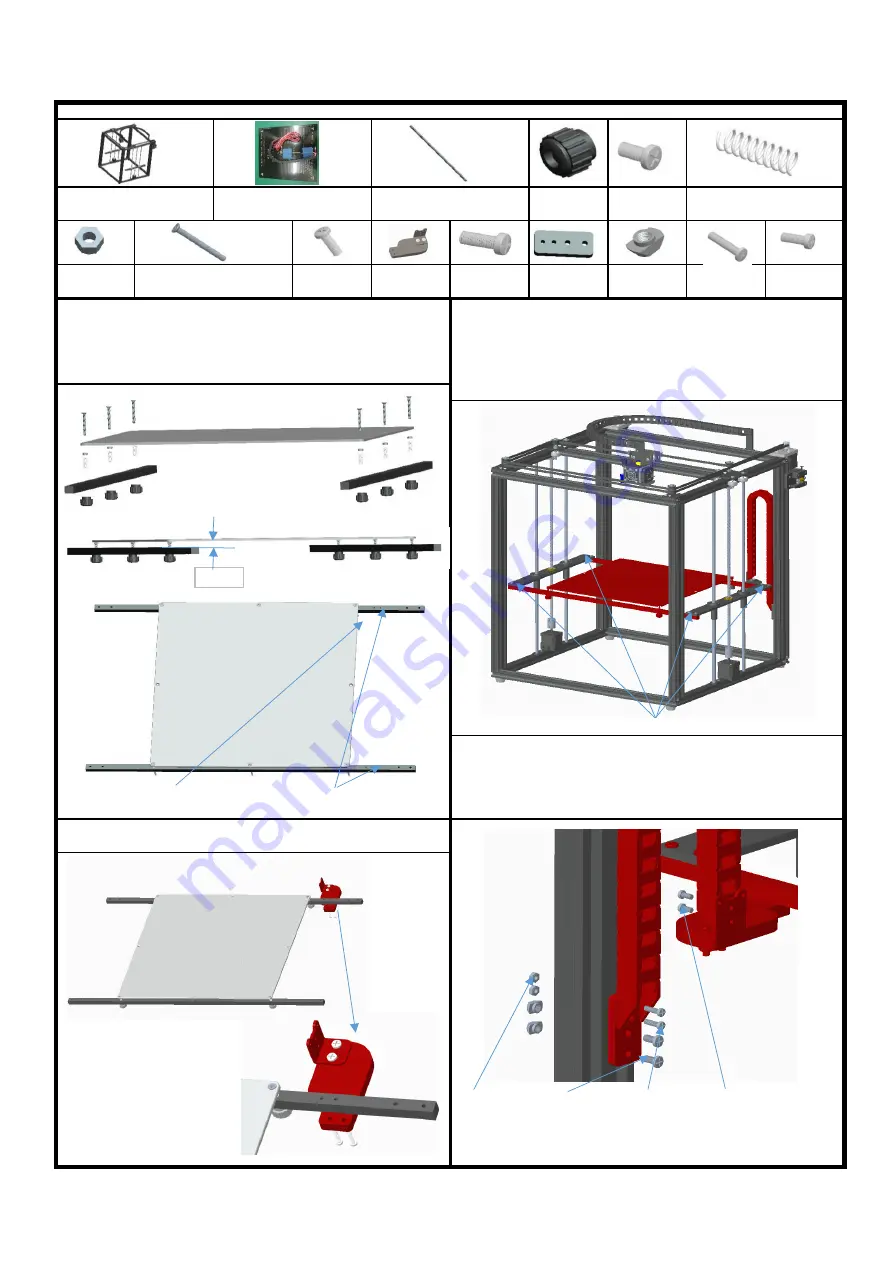
Screws PM4*12
The heatbed wires exit position
The holes
M3 Nut
PM4*8 screw PM3*10 screw PM3*6 screw
2. Place the towline holder to the metal bar by using screw
PM3*16, same as the illustration
4, Assemble the other end of towline and towline base holder by
using PM3*6mm screws , then secure it to right side of
aluminium profile by using 2pcs PM4*8mm screws, same as the
illustration.
1. Put 6pcs KM3 * 30 screws through the heat bed,then lock them with
the nut M3, same as the illustration,put spring through the KM3 * 30
screws
,
then, extending from the hole of the metal bar,screw into M3
butterfly nuts, adjust and keep 10 mm between the heat bed and the
metal bar.
3.Rotate 2pcs lead screws T8*453,keep 2 Z carriage at the same plane,
secure the heat bed component and metal bar with 8pcs screw PM4*12.
The towline bracket is close to the side of the feed motor component,
rotate the screw in the same direction
,
let the platform move up and
down, make sure it can move freely, if not freely, please lossen the
screw PM4*12 to adjust it untill it can move freely
KM3*30 screw 6pcs
PM4*12
screw 8pcs
M4 T nut
2pcs
M3 Nut
8pcs
Towline base
holder 1pcs
Towline
holder 1pcs
PM3*16
screw 2pcs
PM3*10
screw 2pcs
Assemble parts specifications and quantity:
Main framework
Heatbed (with towline)
330x330mm 1pcs
M3 Wing
nut 6pcs
Metal bar 2pcs
Step 9
:
Assemble printer plateform
PM4*8 screw
2pcs
PM3*6
screw 2pcs
Spring 6pcs
10mm