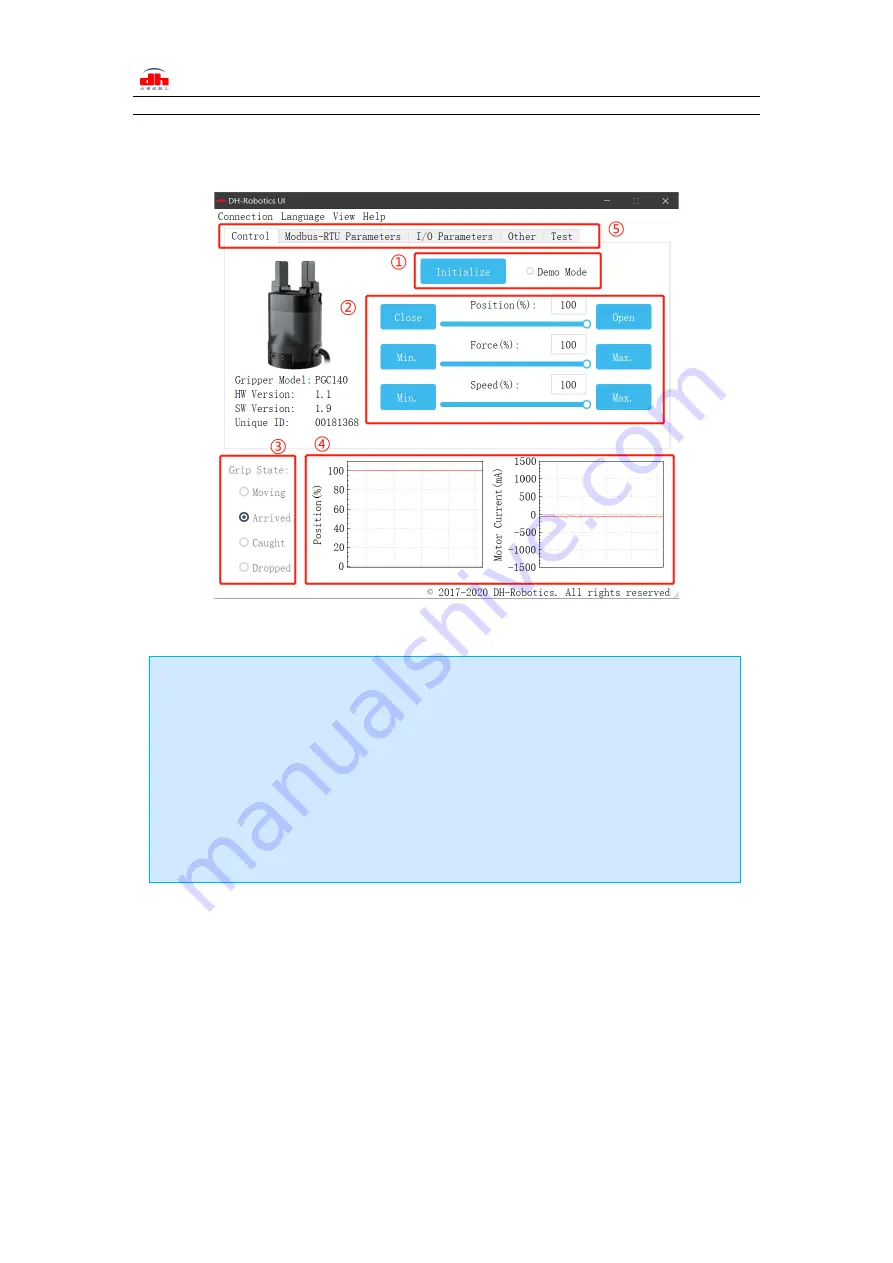
Tel/Fax: 0755-82734836
www.dh-robotics.com
10
(see 2.1.1 Installation and wiring of debugging software).
Open the software, the software will automatically identify the serial port, baud rate, ID number
and other information of the gripper for automatic connection. As shown in the figure below:
Figure 2.3 main control interface
The specific interface description is as follows:
The gripper body uses Modbus RTU for communication, and can read and write data into the
register. The data can be read and written at the view register. The data includes control, feedback,
user parameters and I/O parameters as shown in the following figure:
Interface description
·
①
Initialization and demonstration mode:
the gripper needs to be initialized before
operation to calibrate the zero point. The demonstration mode is a cyclic program.
·
②
Control interface:
it can control the position, force and speed of the gripper.
·
③
Clamping status:
real time display of clamping status of clamping claw.
·
④
Position current real time graph:
real time display position and current. The
current represents the current of the internal motor, not the current actually consumed by
the gripper. The current real-time graph can reflect the stability of clamping force.
·
⑤
Parameter setting:
the configuration parameters of Modbus RTU, such as baud rate
and check bit, can be configured; IO mode is to configure the parameters related to IO
mode;