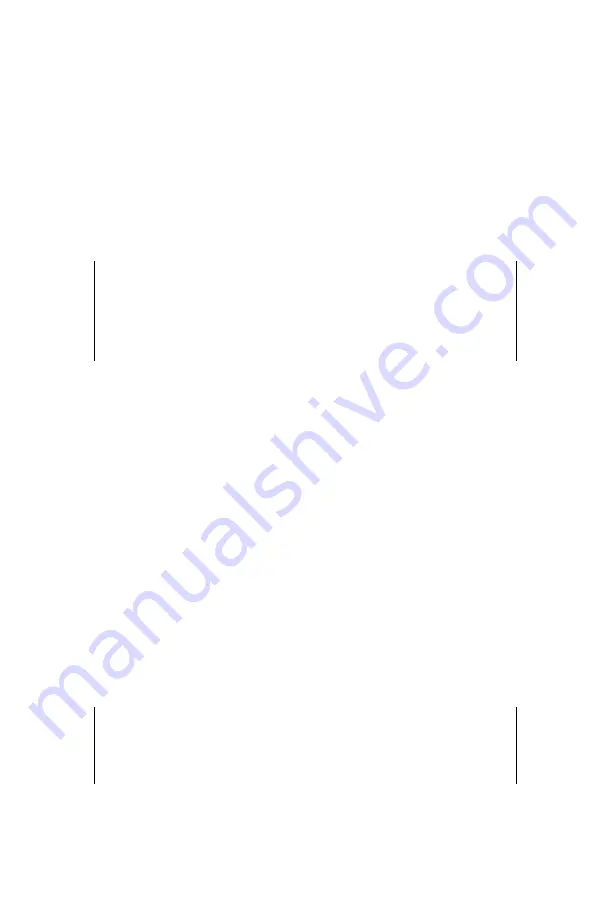
ICO
5-25
♦
Auto-Timer
status (
Enabled
,
Disabled
, or
Suspended
) and
settings (if enabled)
♦
Auto-Tare
,
Auto-Store
, and
Auto-Status Print
status (
ON
or
OFF
)
Use the up and down arrows to scroll through the various
screens. To return to the
Status Menu
, press
(
ESC
)
.
NOTE
The system status display can also be viewed directly
from the default display by pressing the
(
STATUS
)
key.
To return to the default display, press
(
ESC
)
.
PRINT STATUS
To print system status information to the internal printer, press
(
2
)
at the
Status Menu
. While printing, the oven displays
Printing data please wait...
When finished, the oven returns
to the
Status Menu
.
DOWNLOAD STATUS
To download the system status information from the oven,
connect the serial communications port to a computer or other
serial device. The serial communications port is the leftmost of
the two serial ports on the rear panel, as viewed from the rear of
the oven.
NOTE
To ensure proper data transfer, the cable connected
to the serial communications port should not exceed
3 m (10 ft) in length.
Check the baud rate as described on page 5-34. Press
(
3
)
at the
Status Menu
. While downloading the system status
information, the oven displays
Downloading data please
Summary of Contents for ICO 4740
Page 2: ......
Page 13: ...ICO xi Figure 21 Disengage Paper Spindle A 10 Figure 22 Insert New Paper Roll A 11...
Page 14: ......
Page 22: ...1 8 Figure 1 Parts and Accessories...
Page 138: ......
Page 152: ......
Page 161: ...ICO C 1 Appendix C SPECIFICATIONS This appendix contains specifications for the ICO...
Page 166: ......
Page 170: ......