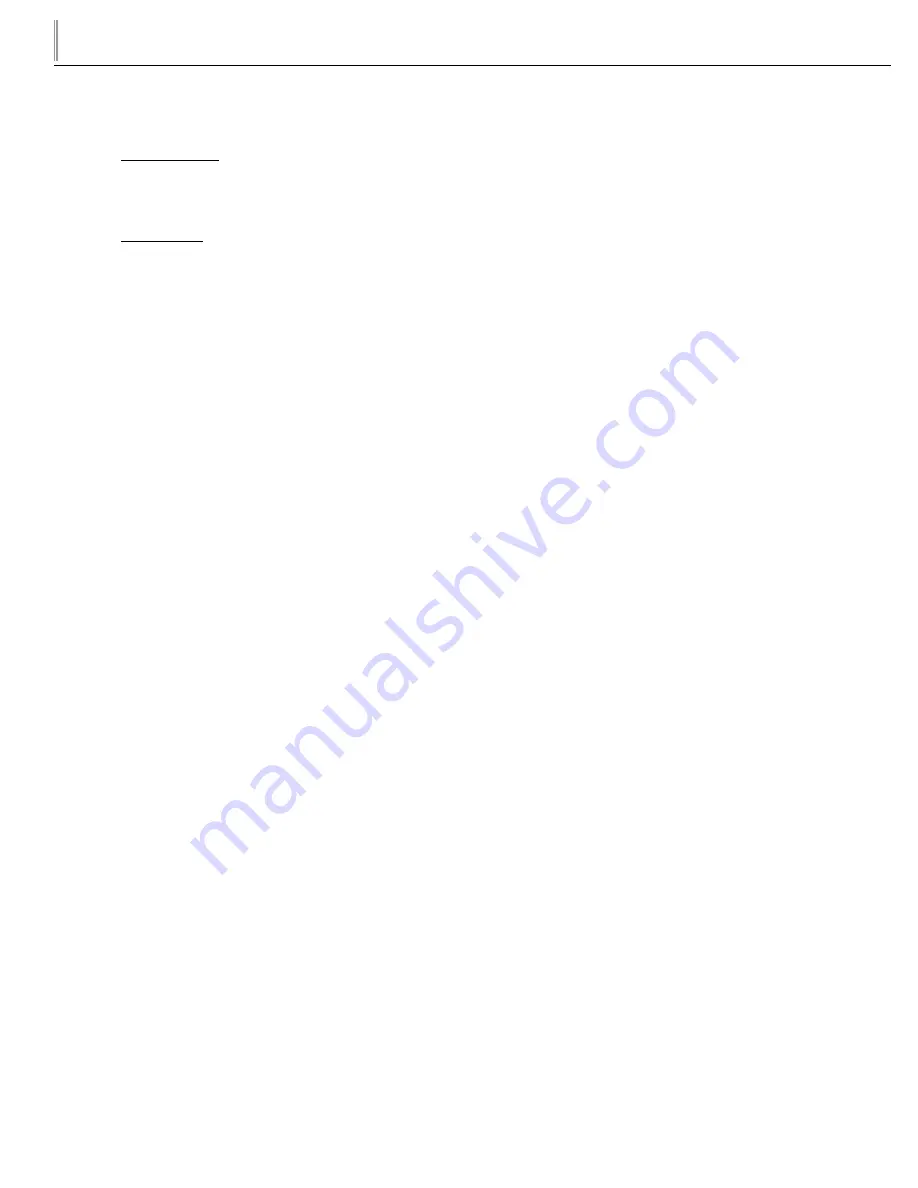
6
TRUE
gdim
www
.
truemfg
.
com
SEALING CABINET TO FLOOR
STEP 1
- Position Cabinet - Allow one inch between the wall and
rear of the refrigerator to assure proper ventilation. For freezers 3
inches between the wall and rear of the cabinet will assure proper
ventilation.
STEP 2
- Level Cabinet - Cabinet should be level, side to side and
front to back. Place a carpenter’s level in the interior floor in four
places:
A. Position level in the inside floor of the unit near the doors.
(Level should be parallel to cabinet front). Level cabinet.
B. Position level at the inside rear of cabinet. (Again level should
be placed parallel to cabinet back).
C. Perform similar procedures to steps A & B by placing the level
on inside floor (left and right sides - parallel to the depth of the
cooler). Level cabinet.
STEP 3
- Draw an outline on the base on the floor.
STEP 4
- Raise and block the front side of the cabinet.
STEP 5
- Apply a bead of “NSF Approved Sealant”, (see list below),
to floor on half inch inside the outline drawn. The bead must be heavy
enough to seal the entire cabinet surface when it is down on the
sealant.
STEP 6
- Raise and block the rear of the cabinet
STEP 7
- Apply sealant on floor as outlined in Step 5 on other
three sides.
STEP 8
- Examine to see that cabinet is sealed to floor around
entire perimeter.
NOTE:
Asphalt floors are very susceptible to chemical attack. A
layer of tape on the floor prior to applying the sealant will protect
the floor.
NSF APPROVED SEALANTS:
1. Minnesota Mining #ECU800 Caulk
2. Minnesota Mining #ECU2185 Caulk
3. Minnesota Mining #ECU1055 Bead
4. Minnesota Mining #ECU1202 Bead
5. Armstrong Cork - Rubber Caulk
6. Products Research Co. #5000 Rubber Caulk
7. G.E. Silicone Sealer
8. Dow Corning Silicone Sealer