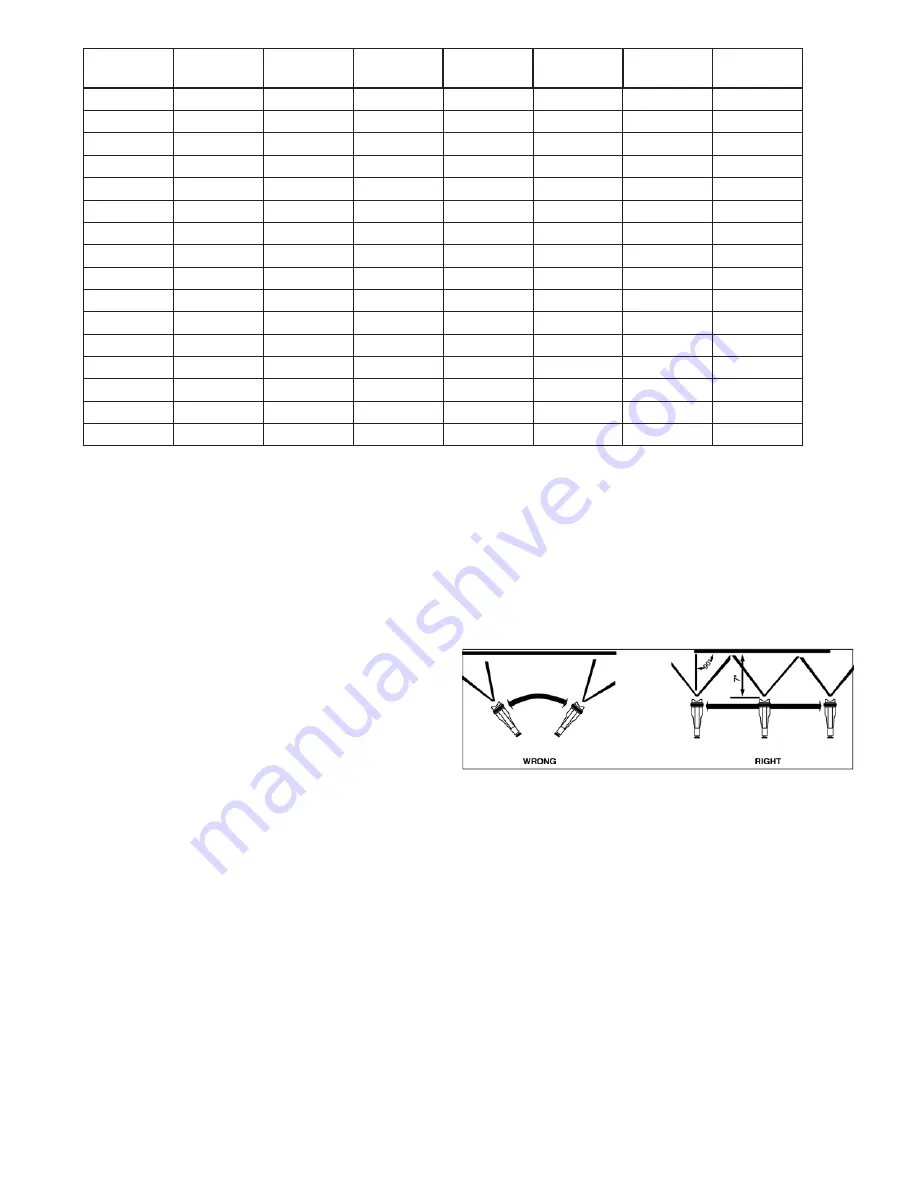
Zahn Cup
sec (#2)
Zahn Cup
sec (#4)
Ford cup
sec (#3)
Ford cup
sec (#4)
Poise P
Centi-poise
cP
Krebs
KU
Saybolt
SSU
16
5
0.1
10
60
17
8
15
80
18
12
10
0.2
20
100
19
15
12
25
130
20
19
15
0.3
30
150
22
25
17
0.4
40
210
24
29
19
0.5
50
30
250
27
33
21
0.6
60
33
320
30
36
23
0.7
70
35
370
34
41
26
0.8
80
37
430
37
45
29
0.9
90
38
480
41
10
50
31
1
100
40
530
49
11
58
36
1.2
120
43
580
53
13
66
41
1.4
140
46
690
56
14
67
45
1.6
160
48
790
74
16
51
1.8
180
50
900
Connect the appropriate air hose to the spray gun. Begin turning the material flow screw (#19, page 33) anti or counter
clockwise 1 – 2 full turns. Look at the size of the fluid pattern and flow volume. Adjust before applying material to your
substrate. If you have too much fluid flow turn the material flow screw clockwise. If you do not have enough fluid flow, adjust
the material flow screw anti/counter clockwise. Hold spray gun 4” – 8” (10cm-20cm) from your work surface depending on
the size of your substrate. Closer is generally preferred for highest efficiency and the least amount of overspray. Follow the
proper spray technique as outlined in the spray technique diagram. You can increase or decrease the fluid flow as desired
as well as the distance from your work surface as necessary. Adjust the Fan Pattern Control Ring as desired.
4.2 Spray Gun Technique
Like any skill, practice makes perfect. Never try to rush the
spray finishing process. Learn the characteristics of the
coating you will be spraying. Build up layers of material (3—4
applications or more if necessary). Sand between coats and
allow proper drying time between applications. It is important
to remember to always keep the distance of the spray gun
the same when moving across your work (or up and down).
(Called a “pass”). Do not rotate or turn your wrist from side to side. Move the spray gun across your work from end to end.
Be sure to maintain the same speed of movement. This will ensure an even application of coating. Always release the trigger
at the end of a “pass”. Continue spraying in the opposite direction overlapping your previous coat by 1/3rd to 1/2. When
finished you should have an even wet coat on your work. If you have dry spots you have overlapped too wide. If you have
heavy or wet spots, or runs you have overlapped too much. When spraying a large or preassembled piece, start at the top
and work down. Try to spray the hard to reach and underneath surfaces first. Common sense and some forethought will
prevent errors.
Remember, that a light wet film will generally produce better results than a heavy wet coat. When spraying a vertical surface
it is advisable to spray a thin/light “tack” coat first, followed by a normal light wet coat. This technique will help prevent “runs”
and “sags”. When using your APOLLO spray gun you control five variables:
1. Fluid Flow
2. Distance of the spray gun from your substrate (4”-8” avg., closer if necessary).
3. Pattern Direction (Vertical, Horizontal & Round fan)
4. Speed of application
5. Fan Pattern Size (adjust fan control ring)
Items 1, 2 & 4 directly relate to each other.
Summary of Contents for Apollo 7500 AtomiZer
Page 32: ...8 Diagram Parts List...