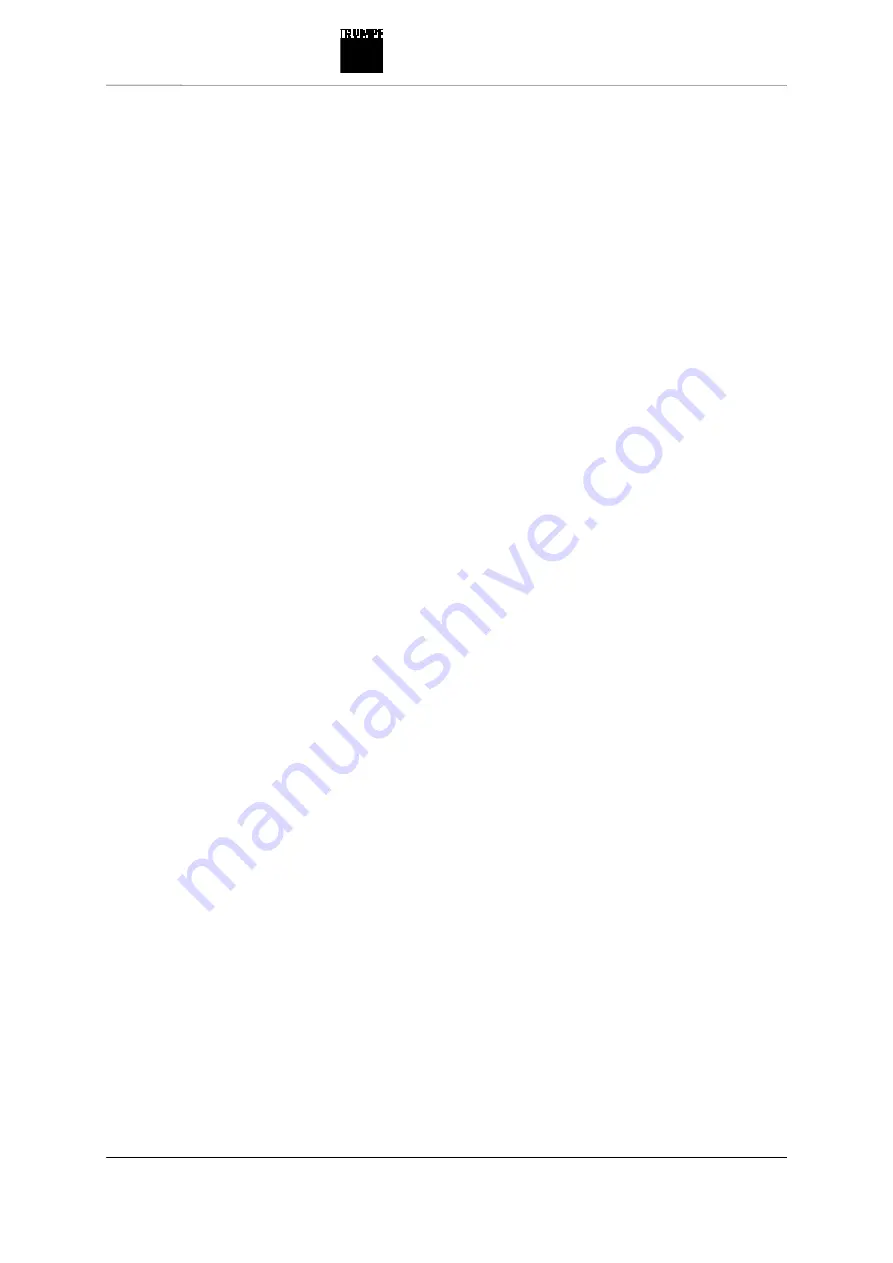
E623EN_01.DOC
Contents
3
Contents
1.
Safety ..................................................................................4
1.1
General safety information...................................................4
1.2
Specific safety information...................................................5
2.
Description .........................................................................6
2.1
Intended use ........................................................................8
2.2
Technical data .....................................................................9
3.
Setting work .....................................................................10
3.1
Selecting the tool ...............................................................10
3.2
Selecting tools for ventilation duct construction.................13
3.3
Loading the rechargeable battery......................................14
3.4
Changing the battery .........................................................17
4.
Operation ..........................................................................18
4.1
Working with the TruTool TF 350 ......................................19
4.2
Joining materials................................................................22
Information concerning the workpiece and the
joint ...............................................................................23
4.3
Selecting processing strategy............................................26
4.4
Slewing ring (optional) .......................................................28
4.5
STAND TruTool TF 350 (optional).....................................29
5.
Maintenance .....................................................................30
5.1
Replacing the tool ..............................................................31
5.2
Lubricating the ram ............................................................37
5.3
Lubricating the coupling.....................................................38
6.
Original accessories and wearing parts........................41
Guarantee
Spare parts list
Addresses