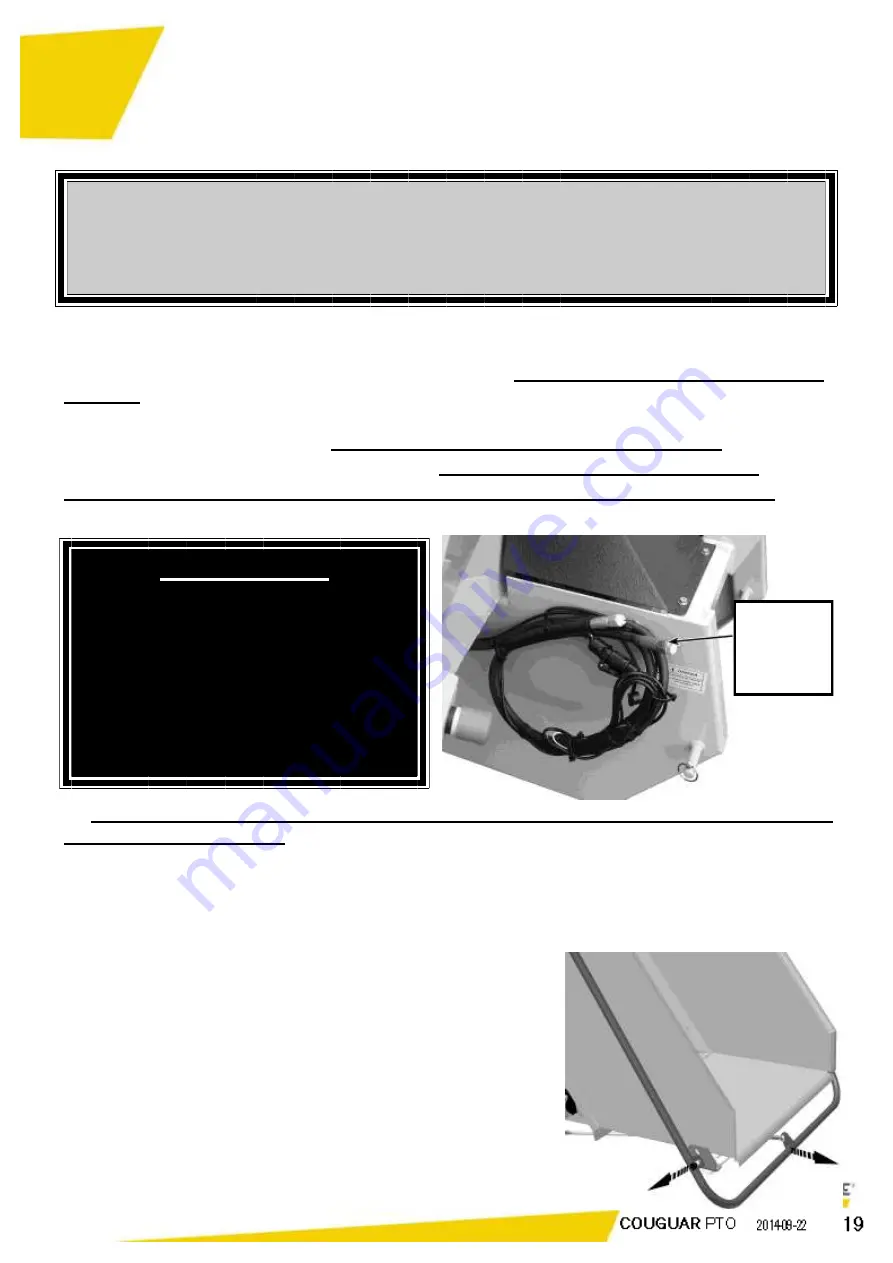
PUTTING INTO SERVICE
Mount at the end of the crusher’s flexible tubes hydraulic plugs suited for the tractor
1) Connect the plugs to a single-effect distributor; the flexible tube marked red to the
pressure and the other flexible tube to a free return
OR
to a double-effect distributor, the flexible tube marked red to the pressure and the
unmarked flexible tube to the other plug;
always respect the distributor’s
engaging direction directionistributor'enclenchement du distributeur.
Flexible
tube with
red marking
= Pressure
ATTENTION !
In order for the feeder roller
to be able to run in forward, it
is essential that the crusher’s
electric supply cable be
connected to the tractor via a
12-volt power supply source
and be at maximum speed.
2) Connect the power supply cable of the VarioStress system to the tractor, while
respecting the polarities:
- white wire: +12 volt
- blue wire: negative
3)
Check whether the emergency stop buttons and the “VarioStress” anti-jamming system
are working.
4)
Check that the cap at the top of the discharge shaft is
open
5) Gradually
engage the clutch of the tractor’s power take
-off.
6)
Increase the engine speed to maximum.
7)
U n l o c k i n g t h e f i n g e r i n d e x i n g and put
the feed roller into rotation by pulling the control bar.
8) Adapt the speed of the feeder roller according to the
oil flow produced by the tractor by playing on the
adjusting wheel of the distributor on the crusher.
9)
Start the shredding.
WARNING!
If for any unknown reason the shredder has difficulty shredding the material and you
have to stop it:
only restart the engine once the cause has been removed and the
material has been cleared from the shredding rotor!
O P E R A T I N G
P R O C E D U R E S
Summary of Contents for Saelen GS/COUGAR PTO
Page 1: ...TECHNICAL MANUAL...
Page 2: ...MAJ 09 2008...
Page 34: ......
Page 35: ......
Page 36: ...CONNECTION OF THE HYDRAULIC HOSES HYDRAULIC COUPLING...
Page 38: ......