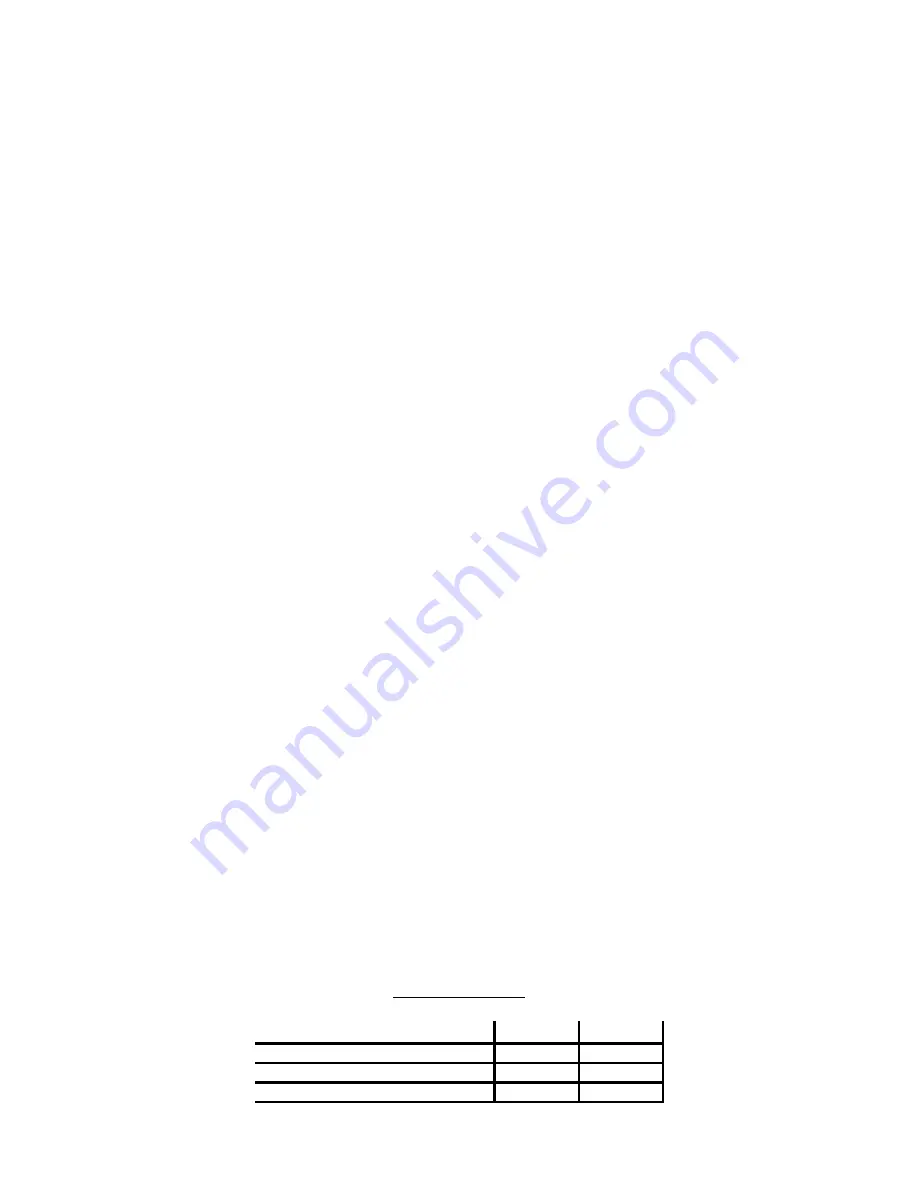
I N T RODU CT I ON AN D T H EORY OF OPERAT I ON
The 3541RL series planetary winch is designed to use a roller-vane gerotor motor, driving through a multiple
disc brake, spring assisted air operated clutch and two planet sets to the cable drum.
The multiple disc brake is spring applied and hydraulically released through a port in the brake housing.
During inhaul, the brake is not released since the load is driven through the one-way cam clutch, bypassing
the brake. When the load comes to a stop, the cam clutch locks up and the load is prevented from moving by
the brake.
The brake and brake valve receives its signal any time the winch is in pay out. With the brake fully open at
about 340 PSI the brake valve will open and dynamically control the lowering of the load.
M AI N T EN AN CE
Tulsa 3541RL series planetary winches, like any other piece of machinery, need to be periodically serviced
and well maintained to insure proper operation.
Good maintenance consists of three steps.
1. A daily inspection to insure that there are no oil leaks present, that all mounting bolts and other fasteners
are tight, and that the wire rope is in good condition.
2. Periodic servicing of the winch includes changing the oil in both the gearboxes and the brake section.
Severity of use will determine the need for oil changes but it should be checked at a minimum of every 500
hours. Factors such as extremely dirty conditions or widely varying temperature changes may dictate
even more frequent servicing.
3. Complete teardowns and component inspections. Again, severity and frequency of use will determine
how often this should be done. If the equipment that this winch is mounted on is subject to standards for
this type of inspection, then those standards must be followed. If oil changes reveal significant metallic
particles then a teardown and inspection must be made to determine the source of wear.
Tulsa 3541RL series of winches are shipped from the factory with SAE 90 EP gear lube in the gearboxes and
automatic transmission fluid in the brake section. This oil should be satisfactory for operation in ambient
temperatures from -10
°
F to +110
°
F. If your work calls for operation in temperatures outside this range, contact
Tulsa Winch for recommendations.
Gearbox oil in gear section is drained by removing the fill and drain plugs (items 79) located on the gearbox
cover (item 61). Gearbox oil in the drum section is drained by removing the plug (item 45) located on the
barrel of the drum (item 1). Examine the used oil for signs of significant metal deposits and then dispose of it
in a proper manner. Reinstall the plugs and fill the gearboxes with the proper amount of new SAE 90 EP gear
lube through the fill hole. Make sure the breather (item 78) is operational and replace if necessary.
Drain the brake section by removing the drain plug (item 32) and breather (item 31) in the brake cover (item
28). Inspect the oil for signs of metallic particles and/or burning and re-install the drain plug. Fill brake section
with automatic transmission fluid, or hydraulic oil.
OIL CAPACITIES
QTY TYPE
GEAR LUBE (DRUM SECTION)
3/4 qt.
EP 90
BRAKE OIL
1/2-1 pt.
ATF
GEAR LUBE (GEAR SECTION)
1-1/2 qts.
EP 90
4
Summary of Contents for Rufnek Intelliguard 3541RL
Page 16: ...16 VISCOSITY CHART...
Page 18: ......