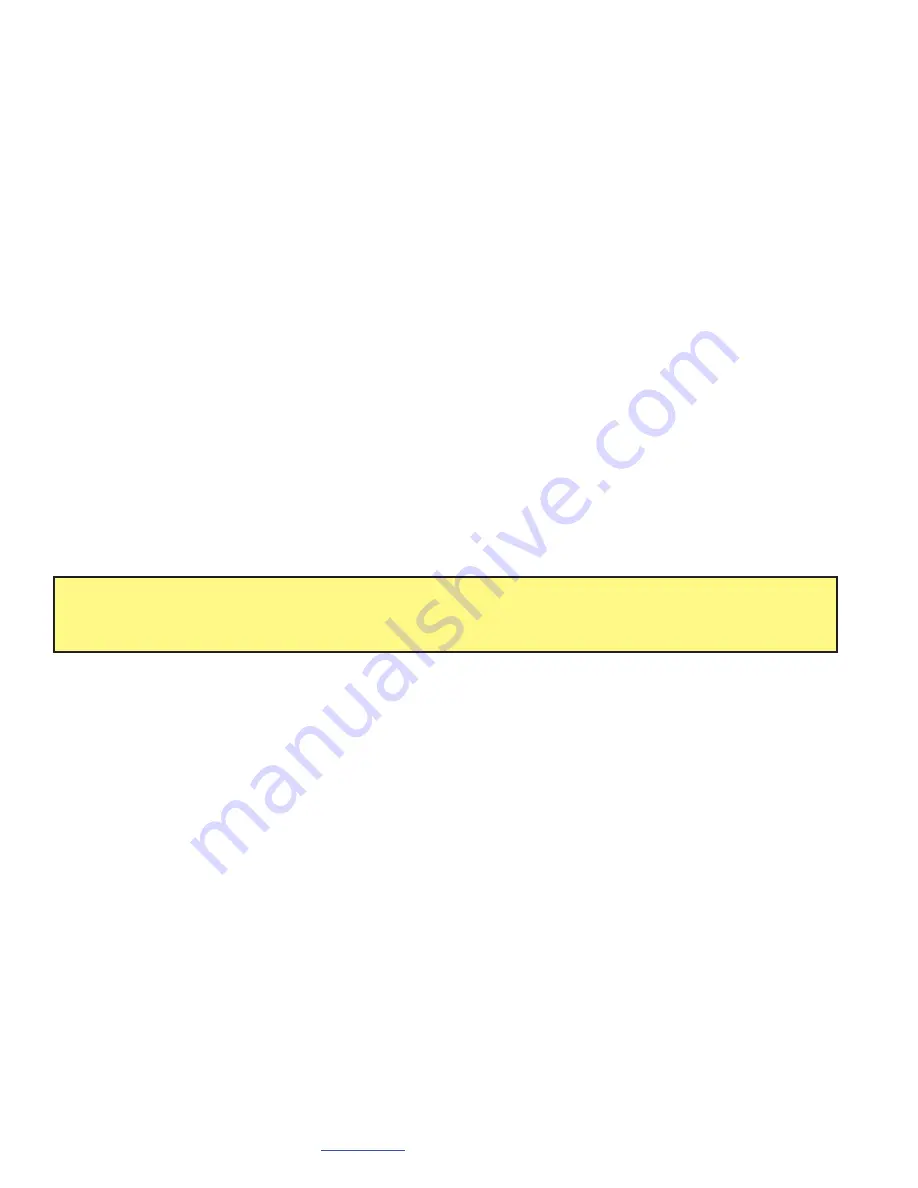
24
www.turck.com
• 1-800-544-7769 • Fax:
(763)
553-0708 • TURCK
• Minneapolis,
MN
55441
www.turck.com
• 1-800-544-7769
• Fax: (763) 553-0708
• TURCK • Minneapolis, MN 55441
25
TURCK
RM-89
Restoring Parameter Values
Changes to parameter values that have not been saved to Flash can be overwritten by restoring them to the values previously
saved in Flash . This is done by using the Class Instance Editor . Open the Class Instance Editor as shown in the Saving
Parameter Values section on the previous page .
With the Class Instance Editor open:
1) In the Service Code section of the window, click on the
Description
drop down list, select the “Restore”
option . The
Value
field will change to “15” .
1) In the Object Address section, set Class: to a value of “23” and
Instance
: to a value of “0” . Also, make sure
the
Send the Attribute ID
checkbox is unchecked .
2) Click on the [Execute] button . The RM-89 will respond with the message “The execution was completed”
in the Receive Data text box .
Resetting Parameter Values
Parameter values can be reset to their factory default values by using the Class Instance Editor . Open the Class Instance Editor
as shown in the Saving Parameter Values section on the previous page .
With the Class Instance Editor open:
1) In the Service Code section of the window, click on the Description drop down list, select the “Reset”
option . The Value field will change to “5” .
1) In the Object Address section, set Class: to a value of “23” and Instance: to a value of “0” . Also, make sure
the Send the Attribute ID checkbox is unchecked .
2) Click on the [Execute] button . The RM-89 will respond with the message “The execution was completed”
in the Receive Data text box .
Note:
These values are not automatically saved in Flash after they have been reset with this command . If you want the parameters
to be at their factory default values after cycling power, you must save these values to Flash as described in the Saving
Parameter Values section on the previous page .
Reading Parameter Values
The present values of the parameters can be read by using the Class Instance Editor . The most common parameters are
available under the Parameters tab of the Properties window as shown in the Setting Parameters section on page 21, and
that method should be used when setting these values . The Class Instance Editor can be used to read the values that are not
available in the Properties tab . To begin, open the Class Instance Editor as shown in the Saving Parameter Values section on
the previous page .
With the Class Instance Editor open:
1) In the Service Code section of the window, click on the
Description
drop down list, select the “Get Single
Attribute” option . The
Value
field will change to “E” .
2) In the Object Address section, set
Class
: to a value of “23”, the
Instance
: to a value of “1”, and
Attribute
:
to the hexadecimal value of the attribute you wish to read . A full list of attributes is available in the
Supported Instance Attributes section of the manual, starting on page 39 . For example, to read the
Actual Sensor Reading, set the Attribute field to “70” .
3) Click on the [Execute] button . The RM-89 will respond with the raw, 16 bit position value of the resolver in
the Receive Data text box (if the attribute field was set to "70") . This value is displayed in hexadecimal, with the
least significant byte first .
Summary of Contents for DeviceNet RM-89
Page 1: ...USER MANUAL MA1007 REV B Published 4 15 2015 RM 89 DeviceNet Resolver...
Page 14: ...14 www turck com 1 800 544 7769 Fax 763 553 0708 TURCK Minneapolis MN 55441 TURCK RM 89 Notes...
Page 38: ...38 www turck com 1 800 544 7769 Fax 763 553 0708 TURCK Minneapolis MN 55441 TURCK RM 89 Notes...