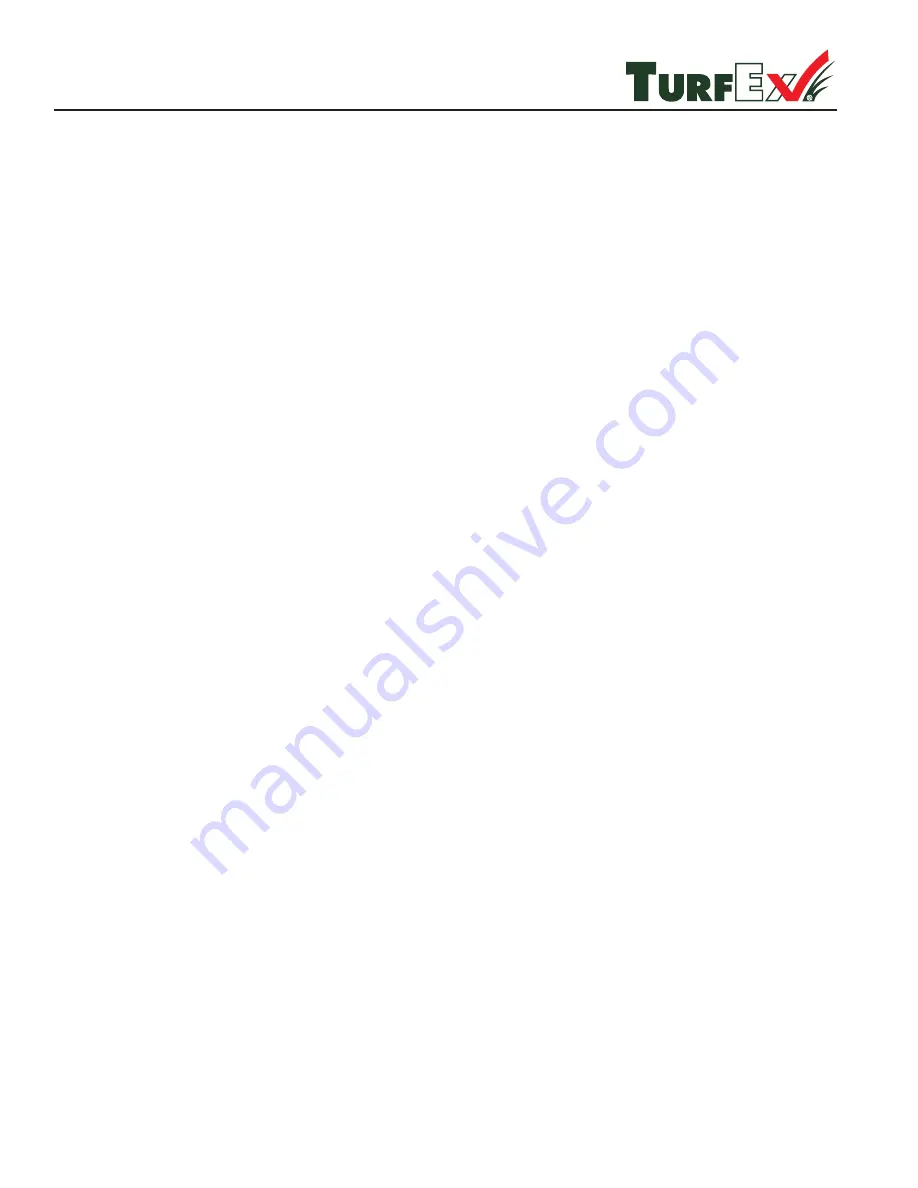
© Trynex International 2012
18
Drivers Training
PHASE V: Driving the machine on hillsides.
Initial hillside training should take place on a slightly hilly open area
free from obstructions with the machine in 1st Gear and the Hopper
and Tanks empty.
• The Trainee must be familiar with the Balance Zone principles and
Driving Techniques before operating on slopes.
• The Trainee must pass the Phases I, II and IV and be totally familiar
with all the WARNINGS and the hillside driving techniques and
principles set forth in the Driver’s Training and Operating Manual
before operating the machine on a slope or incline. Trainee must
never ride the RS7200 on any slopes or inclines greater than 15
degrees.
• As the Trainee is able to demonstrate his ability to control the
machine on hills as well as his understanding of hillside driving
principles and proper techniques; gradually increase the slope.
• As the Trainee progresses, gradually add weight to the Hopper and
Tanks.
Read Safety Manual WARNING “To avoid loss-of-control, tip-over, and
rollover” before operating the RS7200 on an incline or slope.
PHASE VI: Driving over curbs.
• Never attempt to jump a curb at high speed as this may cause a
forward tip-over. Instead:
• Approach the curb or parking block straight on;
• Stop the machine 12 inches away from the curb;
• Shift into 1st gear;
• Gradually accelerate up and over curb.
If machine is unable to climb over a curb:
• Look for a lower section of curb;
• If one is not available, approach the curb on an angle and attempt
to climb over one wheel at a time;
• Use ramps to get over the curb. IMPORTANT: Avoid high curbs
and bottoming out as this can cause machine damage that is not
covered by the Warranty .
Phase VII: Backing Up.
To back up:
• Stop, shift into Reverse, look behind to make sure the path is clear,
and keeping both feet on the operator’s platform and a firm 2
handed grip on the handles gradually pull the Throttle.
To turn right:
• Pull the right Handle toward you and push the left handle away
from you.
To turn left:
• Reverse the procedure.
To stop backing up:
• Release Throttle and apply one or both Brake Levers to stop.
Read Safety Manual WARNING “Reverse Operation” now.
Phase VIII: Completing Daily Service Checklist.
Adjust, Repair, replace, and report any irregularities discovered to
your supervisor.
• Clean machine in a designated area. IMPORTANT: DO NOT
power wash machine. High pressure water will force corrosive
fertilizer residue into bearings, linkages, and other parts.
Corrosion damage is not covered by the Warranty. Instead
use low pressure air regulated to 29 PSI Once a week, or as
necessary, use low pressure water regulated to 29 PSI to wash
machine. Start and run machine and blow dry to remove any
water.
• Empty Hopper. NOTE: Use a dedicated pail or wet /dry vacuum
to remove fertilizer so that it can be recycled.
Clean:
•
Spinner Platter.
• Footpads.
• Nozzles and Nozzle Strainers, If necessary.
• Hopper opening plate, Auxiliary Gate Slide plate and linkage.
• Engine cooling fins, Blower housing inlet (Starter), carburetor,
governor linkage, Honda Throttle Lever, Throttle Lever and cable.
Lubricate and protect the following, using WD-40 or equivalent:
• Operating controls and cables.
• Hopper Opening Plate and Auxiliary Gate Plate.
• Carburetor and all linkages and springs.
• Exposed aluminum.
Check and record Engine Idle Speed (Must not exceed 1650 RPM).
Check and record Engine Top Speed (Must be 3,450 RPM).
Gage, record, and adjust Hopper control settings as necessary,
including:
• Auxiliary Gate Adjustment Plate.
• Hopper opening.
• Rate Adjustment Knob
Check and adjust the Spray Nozzle alignment as necessary.
Check and top off engine oil.
Check and top off clutch oil.
Check for loose or missing fasteners or parts, cracks in metal or
welds.
Read Safety Manual WARNING “Maintenance and Service” now
BEFORE starting or operating machine.
Phase IX: Loading and unloading the machine on a Transport.
Trainee must be instructed how to safely load and unload the
RS7200 from a transporting vehicle.
Read Safety Manual WARNING “Transporting” before attempting
to load or unload the RS7200 from a transport.
Phase X: Additional Service Training
Trainee should be instructed on any additional service he will be
required to perform on the RS7200 such as, changing Engine and
Clutch oil, greasing, etc. Refer to Service Manual for scheduled
service requirements and details.