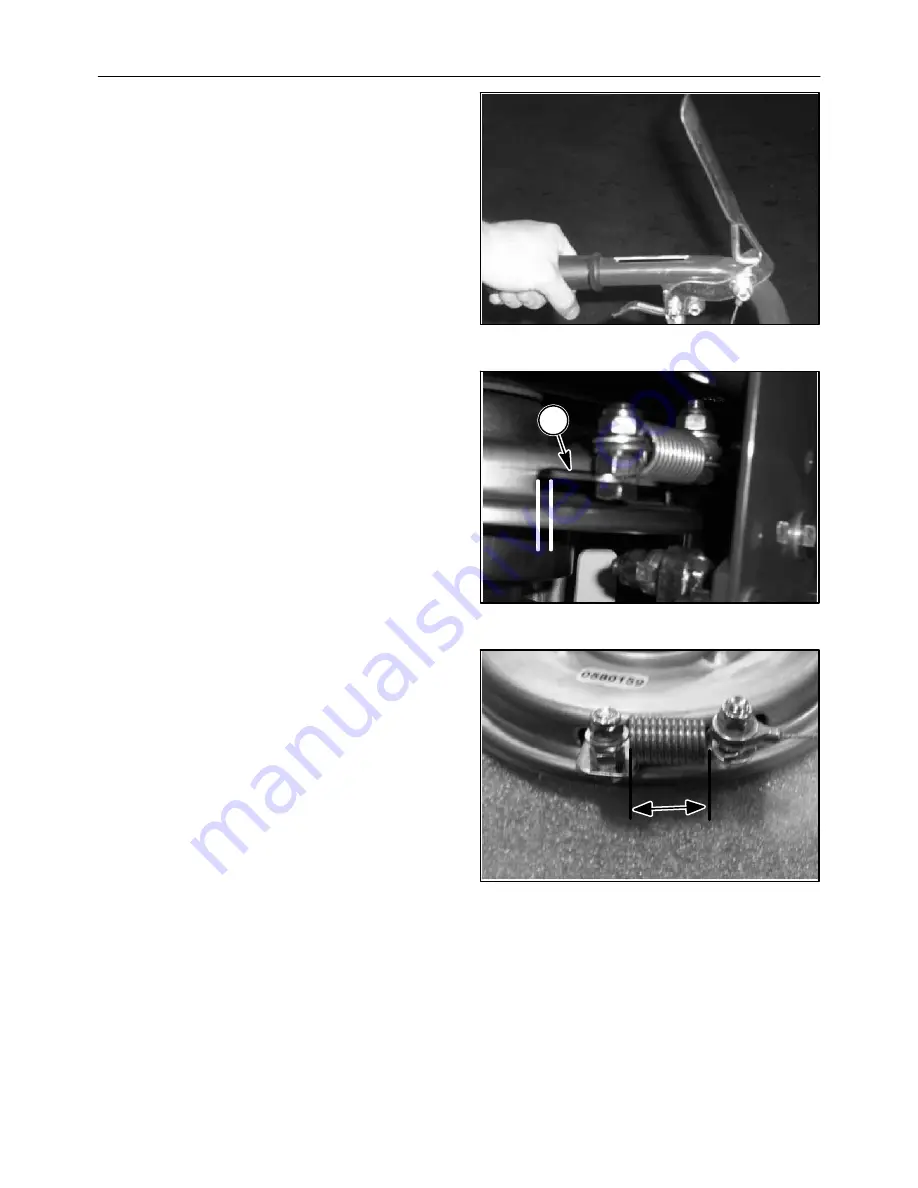
49
CLUTCH CABLE ADJUSTMENT
NOTE: Before checking clutch cable adjustment,
check that when the clutch handle released is
released, the clutch spring must not have tension on
it and the lever, A, must be within 1/4 inch of the clutch
housing as shown.
78
A
79
1. Measure the length of the spring in the
disengaged position as shown.
NOTE: The spring must not have tension on it in the
released position.
80
Summary of Contents for 1305B
Page 1: ...OPERATOR S MANUAL MODEL 1305BC BRUSH CUTTER ...
Page 89: ......
Page 90: ...BC02 1009 Printed in U S A ...