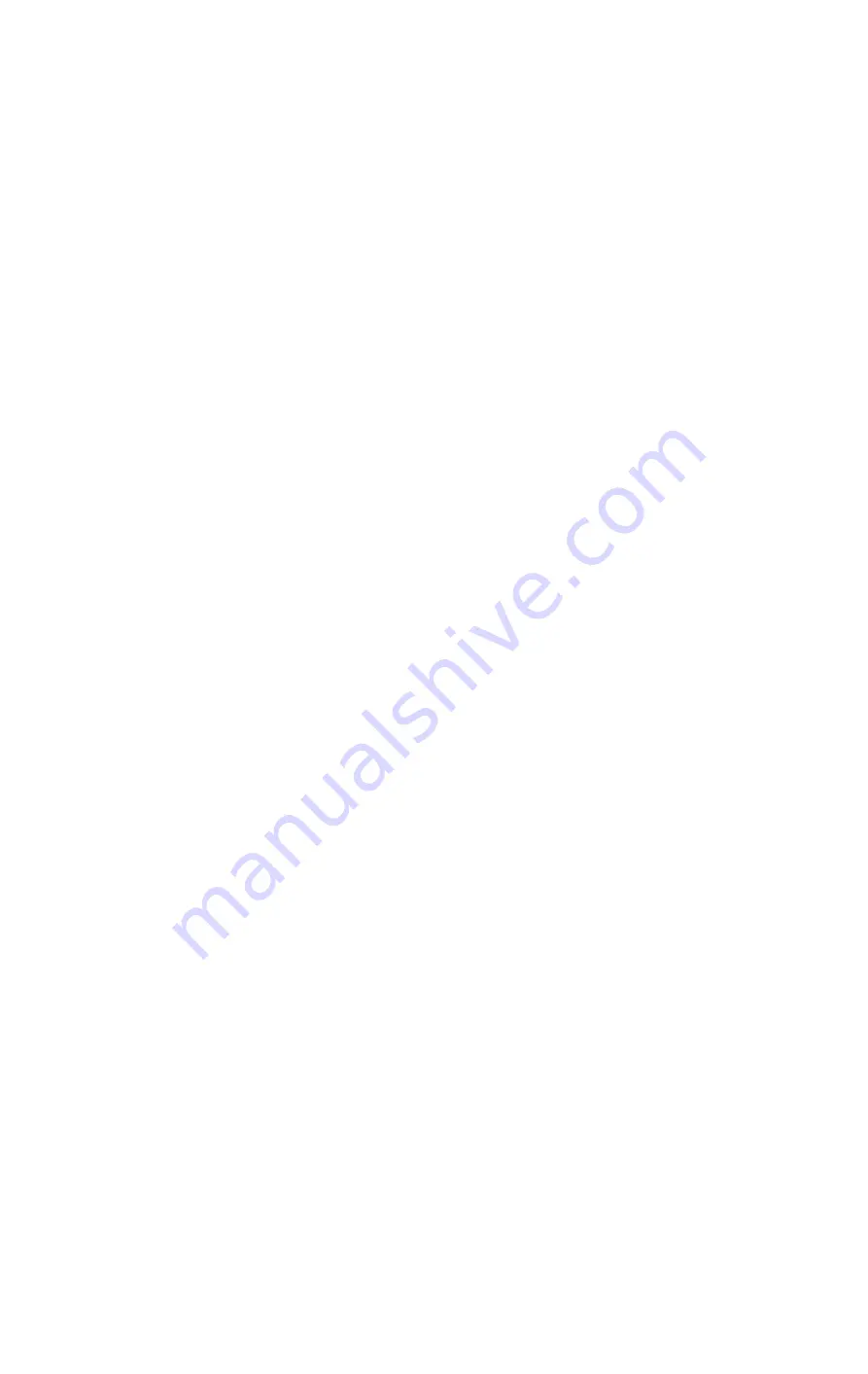
3
Residual energy: After the gas source or hydraulic pump is turned off, there are
residual gases/liquids in the pneumatic/hydraulic system. These gases/liquids have a
certain amount of energy. Certain measures must be taken to prevent the residual energy
from harming the human body and equipment. Before servicing pneumatic and hydraulic
components, the energy remaining in the system needs to be released.
Safety design: Prevent components from falling off and hydraulic oil from flowing
out;
Safety valve shall be installed to prevent accidents;
Maintenance tools need to be prevented from falling.
7) Risks during operation
Overview: Industrial robot is a flexible system that can be applied in many industrial
fields. All the work must be operated by professional personnel and follow certain safety
guidelines. Always be careful when operating.
High-quality operators: Industrial robots must be operated by professionals who are
familiar with the whole system and understand the risks in each subsystem.
Abnormal risk: If an abnormality occurs under normal working procedures, take extra
care.
8) Electrical risks
Overview: 1. Although it is necessary to turn on the power during fault diagnosis in
many cases, it is necessary to turn off the power and cut off other power
connections when actually repairing the robot.
2. The main power supply of the robot needs to be installed outside the
working range of the robot, so that even if the robot is out of control,
the operator can turn off the robot outside the working range of the
robot.
Operator's electrical hazard:
Operators need to pay attention to high voltage hazards:
1. The power line of the servo motor;
2. Connect fixtures and other external equipment. After the robot is turned off, the
external equipment of the robot may still be running, so the power cord of the external
equipment may also cause personal injury or damage to the power cable.
1.2.3 Safety behavior
1) Safety measures
Overview: Fences and warning signs should be installed around the working area of
the robot to ensure the safe work of the robot, prevent the entry of other people and prevent
the robot from injuring others.
Safety measures: When setting up safety protection measures, it is necessary to
consider that the workpiece held by the robot can cause injury to people.
2) Remove the robot arm in an emergency
Description: In an emergency, any arm of the robot is caught by the operator and
needs to be removed. (Refer to Chapter 5 Maintenance for the dismantling steps.) Small
robot arms can be removed manually, but large robots need to be lifted by cranes or other
equipment.
Secondary damage: Before releasing the joint brake, the mechanical arm needs to be
fixed first to ensure that the mechanical arm will not cause secondary injury to the trapped
person under the action of gravity.
3) Brake detection
Why it should be tested: In normal operation, the brake is usually worn out, so it is
necessary to test the brake.
Check brake steps: 1. Let each joint of the robot move to the position where the
joint bears the maximum load;
2. Turn off the robot and open the lock brake;