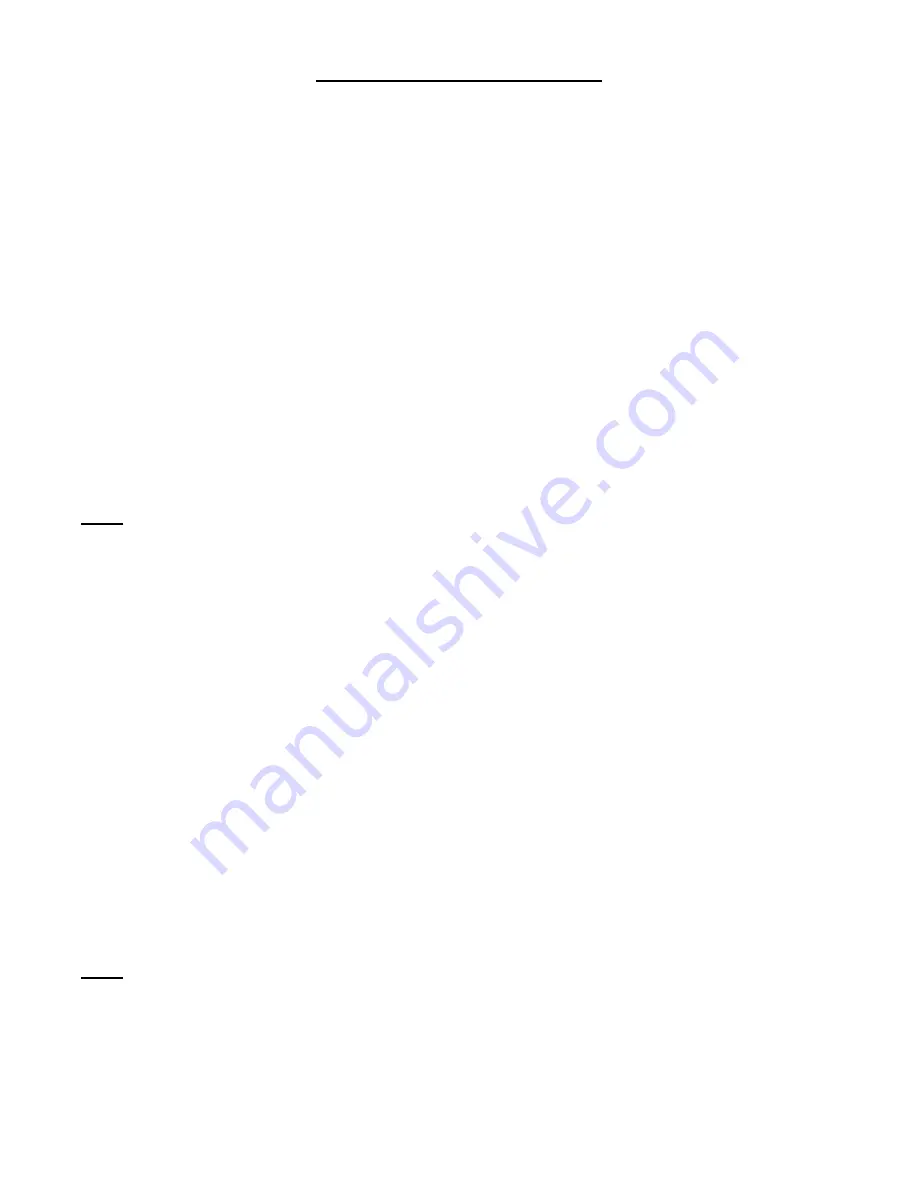
14
TP9KAC-TUX
Mar 2019
OPERATION INSTRUCTIONS
RAISE LIFT
1. Read operating and safety manuals before using lift.
2. Always lift a vehicle according to the manufacturers recommended lifting points
3. Position vehicle between columns, as equally as possible.
4. Adjust swing arms so that the vehicle is positioned with the center of gravity midway between pads.
5. Use truck adapters as needed. Never exceed 9
” of pad height.
6. Raise the lift by pressing button on power unit until support pads contact the underside of the vehicle
and re-check to make sure vehicle is secure.
7. Raise vehicle to desired working height. The latch mechanism will
‘trip over’ when the lift raises and drop
into each latch stop.
8. Press lowering
‘release’ lever on Power Unit to lower lift onto latches, to lock the lift in the proper safety
position.
Note: Always lock the lift before going under the vehicle. Never allow anyone to go under the lift
when raising or lowering. Read the safety procedures in the manual.
LOWER LIFT
1. Ensure tools, trays, stands and/or personnel are removed from under vehicle.
2. Slightly raise lift until the safety latches clear column locks.
3. Pull latch release cables on both sides.
WARNING:
ALWAYS RELEASE BOTH SAFETY LATCHES ON EACH SIDE
4. Press the release lever on the power unit to lower the lift.
5. Before removing vehicle from lift area, position lift arms and supports to provide an unobstructed exit.
WARNING:
NEVER DRIVE OVER LIFT’S ARMS.
Note: It is normal for an empty lift to lower slowly, it may be necessary to add weight.