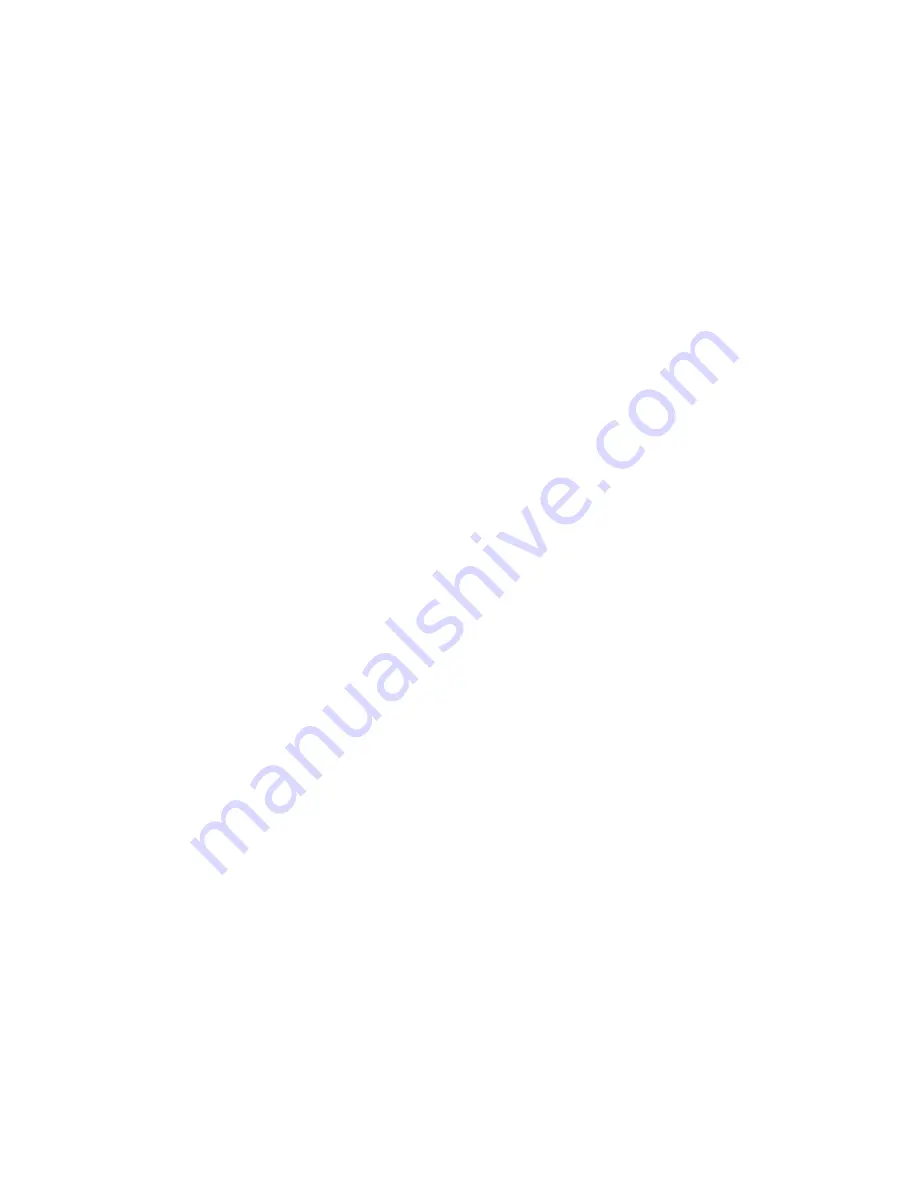
18
TP9KACX / TP9KSCX
Jan 2017
Only trained maintenance experts should perform lift service for the following items.
•
Replace hydraulic hoses
•
Replace chains and rollers.
•
Replace cables and sheaves.
•
Replace or rebuild air and hydraulic cylinders as required.
•
Replace or rebuild pumps / motors as required.
•
Check hydraulic and air cylinder rod and rod end (threads) for deformation or damage.
•
Check cylinder mount for looseness and damage.
Relocating or changing components may cause problems. Each component in the system must
be compatible; an undersized or restricted line will cause a drop in pressure. All valve, pump,
and hose connections should be sealed and / or capped until just prior to use. Air hoses can be
used to clean fittings and other components. However, the air supply must be filtered and dry
to prevent contamination. Contamination is the most frequent cause of malfunction or hydraulic
equipment.
Summary of Contents for TP9KACX
Page 4: ...4 TP9KACX TP9KSCX Jan 2017 ...
Page 6: ...6 TP9KACX TP9KSCX Jan 2017 Fig 2a TP9KACX Asymmetric Lift Fig 2b TP9KSCX Symmetric Lift ...
Page 21: ...21 TP9KACX TP9KSCX Jan 2017 EXPLODED VIEW 1 ...
Page 22: ...22 TP9KACX TP9KSCX Jan 2017 EXPLODED VIEW 2 ...
Page 26: ...26 TP9KACX TP9KSCX Jan 2017 ...